The Xtrax impurities extraction system is designed to function as a stand-alone pulp line in a facility next to a conventional recycling plant. Xtrax has been tested successfully at Thermo Black Clawson's $5 million Technology Center in Middletown, OH, described by the company as a "full-scale plant that demonstrates processes for virgin and secondary pulp processing," according to Jon Kerr, TBC's director of business development. TBC and Inland Paperboard and Packaging are joint patent holders of the Xtrax process. The process begins as waxed boxes, as well as curbside and office paper, are placed on a conveyor that carries them into a batch hydropulper. The batch process, says Kerr, is important because it accepts curbside materials, which are readily available. Those materials, however, can include magazine stock, ground wood and wet-strength papers. Yet the system can handle that mixture by gradually separating waste, first by larger pieces, then to the point where it washes out short fibers and smaller particles or fines, as well as ash or clay. Kerr says that the Xtrax system controls the fiber at a level between 8% and 11%, with roughly 90% water. The two key aspects to the Xtrax process are reverse cleaning/screening and the use of elevated temperatures. "We want to control the temperature in the hydropulper at about one-hundred and fifty degrees Fahrenheit," says Kerr. "That's higher than the normal one-hundred ten to one-hundred twenty degrees in normal OCC repulping. The higher temperatures emulsify the wax and move it into the water phase. "Other systems have separated the wax so that it floats on top of the water, and that never worked," he continues, "because at lower temperatures the wax would stay with the fibers." Above its 125°F to 145°F melt range, TBC contends the wax stays with the water rather than clinging to the fiber. A hydrapurge pressurized screen filters out large contaminants. These are rejected through an extruder. Acceptable material is pumped, under pressure, through liquid cyclone cleaners that spin out additional rejects. The pulp fiber/waxy water mash then reaches a three-stage counter-current reverse screening system. The mash enters the first cylindrical screen from one end, with the water/wax mixture passing through to a clarifier that floats out the wax and any fines. Before passing through the first screen, designated P1, the mash contains approximately 35% wax; afterwards, wax is reduced to 10%. After P2, it's down to 5%. After passing through P3, and two additional cleaning systems, the wax content is less than 1%, according to TBC. "The counter-current, or reverse screening/washing at high temperature separates the wax from the filter," Kerr explains. "Washing removes the fines that tend to clog up the material. The whole phenomenon of what holds paper together are the bonding sites between the fibers as they overlap." The Xtrax process, he contends, "exposes more long fibers that give the material greater tensile strength. The longer the fiber is, the more opportunity it has to cross over other fibers and create a strong bond. Fiber is nothing more than a cellulose polymer, and those polymer chains interlink and bond through their hydrogen sites. That's what holds them together."
Paper companies wax eloquent about wax separation process (sidebar)
'Reverse-cleaning' separates wax from fiber
Jul 31, 1998
Companies in this press-release
Machinery Basics
2024 PACK EXPO Innovations Reports
Exclusive access: Packaging World editor-curated reports revealing PACK EXPO's most groundbreaking technologies across food, healthcare, and machinery sectors. Each report features truly innovative solutions selected from hundreds of exhibitors by our expert team. Transform your operations with just one click.
Access Now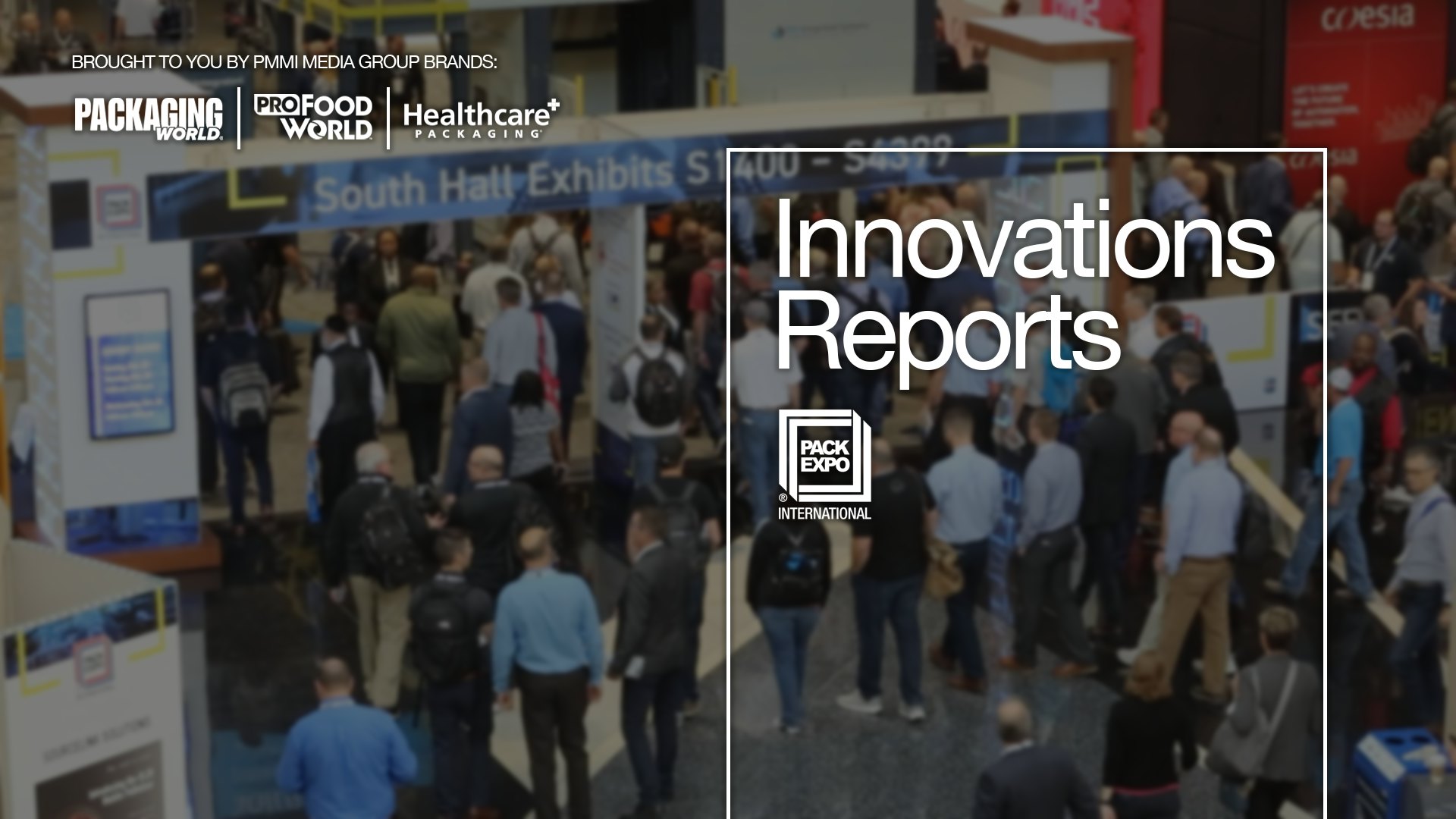
Annual Outlook Report: Automation & Robotics
What's in store for CPGs in 2025 and beyond? Packaging World editors explore the survey responses from 118 brand owners, CPG, and FMCG Packaging World readers for its new Annual Outlook Report.
Download