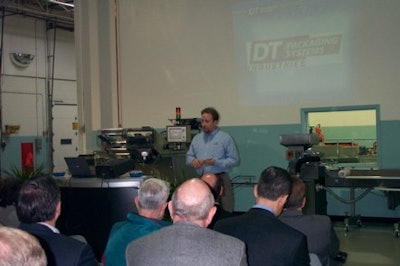
At the plant, DT was manufacturing packaging lines for several major pharmaceutical firms, though confidentiality agreements prevented DT from identifying those firms.
The 105ꯠ sq’ plant went online just after last Thanksgiving, said DT president Jim Ririe. The plant houses engineering and manufacturing for Lakso, Merrill, and Kalish equipment, as well as sales, service, change parts, systems integration, and validation services. "The move to the new, larger plant gives us more room to assemble large, integrated packaging lines," said Ririe. "And with everyone in one location, it’s much easier for customers to reach the people they need."
Along one wall in the plant, DT built customer "suites" with phone, Internet, and e-mail access. "This allows them to electronically convey drawings, design changes, and CAD files back and forth with management to move along the acceptance process," said Michael Gould during a tour of the plant. Gould was recently appointed director of sales of all Lakso, Merrill, Kalish, Swiftpack, and King equipment in North America.
The customer suites are located on the shop floor, close to where the packaging lines are manufactured. That permits customers to inspect the equipment and conduct "F.A.T." (Factory Acceptance Testing) to make sure the equipment meets their specifications.
At Leominster, DT demonstrated its first "Valu Line," an integrated tablet-bottling line built for an unnamed customer in 12 weeks. The 30 bpm line shown included two rotary tables, a Swiftpack SV2 electronic tablet counter, a capper from D.L.-Tech (www.dl-tech.net), a Pillar Technologies (www.pillartech.com) induction sealer, Kalish Torquit retorquer, and D.L.-Tech pressure-sensitive labeler. The Valu Line concept was introduced at Pack Expo 2002.
Also demonstrated was a 100% accurate hybrid slat filler, the DT Merrill 72-39HY, for pharmaceutical and nutraceutical bottle packaging. The filler was shown as part of an integrated 300 bpm line that included the slat filler, a Lakso Model 300 cottoner, and an "S" module, connecting two conveyors.
Separately, DT also announced the availability of Radius top slats, a new style for slat filler change parts. Designed to eliminate "shortcounts" for small tablet applications, the radius top slats are curved to match the divider assembly or upper manifold of the slat filler. DT says it was recently awarded a U.S. Patent for the Radius top slat design.