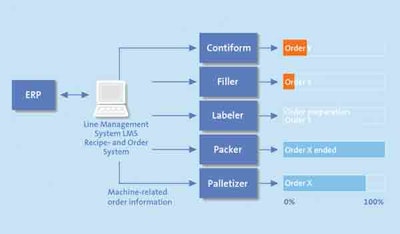
In-line blowing and filling of refrigerated flavored milk drinks into single-serve PET bottles is taken to a whole new level of automation at Mueller Sachsen GmbH in Leppersdorf, Germany. Just five operators are required to run two lines capable of in-line blowing and filling of PET bottles at a combined speed of 1,200 bottles/min.
Bottle sizes include 330-, 400-, 500-, and 750-mL (11.6-, 13.53-, 16.91-, and 25.36-oz). When all the different flavors are factored in, the number of SKUs involved is about 90. Faced with so much variety—driven, of course, by widely varying retailer preferences—changeover has to be optimized, and indeed it is. Changeover that includes a new bottle size requires about 3 hours, as blow molds have to be changed. But when going to a new flavor or label or a different bottle-count in a tray, which occurs far more frequently than a change in bottle size, changeover takes about 20 minutes. That compares to the two hours or so typically required on lines that are not so cleverly integrated. Even more impressive is that one of the lines is able to draw product from four different tanks and fill bottles in, for example, a chocolate, vanilla, strawberry, banana sequence. The different-flavored bottles are then united in equal ratios in a corrugated tray in quantities of 8, 12, or 24.
The secret to all this flexible automation is that production orders flow automatically from the firm’s Enterprise Resource Planning (ERP) system to a recently developed automated order system and thence out to packaging machines on three different floors of this sprawling and impressive facility. The ERP system comes from SAP (www.sap.com) and the automated order system, called Line Management System (LMS), comes from Krones (www.krones.com). Krones also supplied most of the packaging machines in the two lines, with the exception of two tray packers from Schubert (www.ckungsmaschinen.de), two palletizers from A+F Automation (www.afautomation.com), and a pallet stretch wrapper from Haloila (www.haloila.com). Krones was also responsible for line integration of the entire package. Mueller was the first to implement Krones’ LMS solution, and Mueller’s lines represent the culmination of more than three years’ work. The Mueller installation remains among the most sophisticated automated order systems in the world of packaging.
It should be noted that this kind of Information Technology is designed specifically for packaging lines where changeovers are common. In such an environment, it pays big dividends. This is especially true at Mueller, because not only is changeover frequent but the packaging lines are spread across three floors. Blowing and filling is done on the ground floor, labeling and tray packing is done on the third floor, and palletizing/stretchwrapping is done on the second floor.
“The LMS helps a lot,” says Mueller project engineer Hagen Riedel. “We gain tremendous visibility into what machines are doing throughout both lines, even though the machines sit on three different floors.” Without such visibility, he adds, 20-minute changeovers would not be possible.
At the touchscreen of each packaging machine, says Riedel, the operator is informed what the equipment must do for the current order and the following one, too. He knows the planned number of containers in each batch, and he knows what preform, cap, label, and corrugated tray need to be made available so he can have them ready before they’re even needed. With the press of a button, packaging materials that are going to be needed for the next order are automatically delivered by the warehouse management system.
Comparison of old and new
In a more conventional scheme, there’s a tendency to consider each machine in the line as an individual entity. When changing over to a different SKU, in most cases the entire line is emptied before the next order commences, following any necessary make-ready adjustments. The requirements for the operator include ordering the raw materials and supplies in good time, manually selecting the product and parameters at the machines, and starting up the line. This laundry list of tasks demands a lot from the operators, and the difficulty of executing these tasks is magnified when product diversity is as great as it is at Mueller and when filling and secondary packaging don’t even take place on the same floor.
Thanks to Krones’ LMS, the lines at Mueller operate in anything but a conventional scheme. They’re controlled as tightly integrated systems running sequential batches in an optimized manner. They obtain all production-relevant information not from shift managers wielding clip boards or from operators entering it at a touch screen panel. Instead, it comes down from the ERP system. This includes all requisite data for tracking, such as sell-by date, filling time, and filling valve assignment. Operators on the line see two batches at a time: the current one and the next one. This enables them to perform forward planning at their machines. “Mueller wanted to take automation as far as they could, even to the point of having orders transmitted automatically from the customer’s ERP to the Mueller ERP and right on out to the packaging lines on the plant floor,” says Holger Bissbort, Information Technology project manager at Krones.