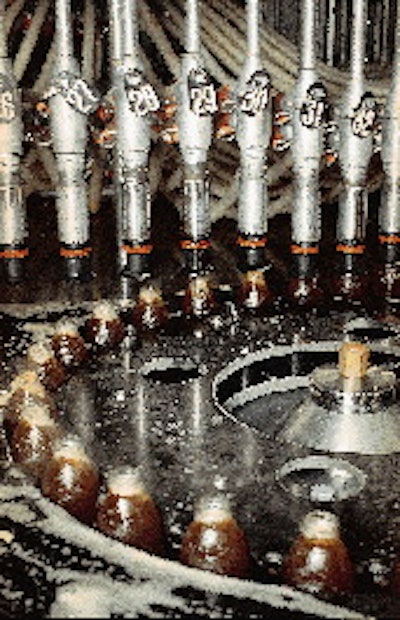
The Fogg (Holland, MI) 78-valve pressure-gravity filler reduces product giveaway by reducing spillage. Previously, the firm had to tolerate a small amount of spillage due to bottles passing through sharp turns at the starwheels that transfer bottles onto and off its other fillers.
On the 78-valve Fogg filler, the bottle transfer points are engineered to greatly minimize spillage. Like a conventional rotary filler, bottles pass through an entry starwheel, are carried around the filler, and exit through a discharge star. But unlike a conventional filler, there are no bottle "platforms" that convey the bottles; nor do the starwheels do the conveying. Instead, a single serpentine conveyor carries the bottles through the starwheels, around the filler turret, and through the discharge, literally carrying the bottles throughout the entire bottling process. (The starwheels remain for bottle stability and spacing.)
"It stays on the same chain from start to finish, and we don't have that loss during transfer," says Frank Hyatt, maintenance supervisor. Current filling speeds are about 725 bottles/min.