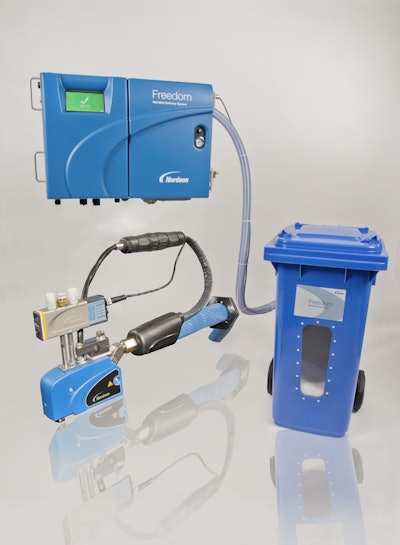
The Freedom Solution provides six “freedoms,” and the solution is said to recover equipment cost in less than 12 months.
The six freedoms include:
Freedom from adhesive availability concerns. Technomelt Freedom-certified, adhesives use readily available polymers that are less affected by petrochemical feed stock demands and shortages than traditional packaging EVA adhesives;
Freedom from downtime associated with char and contamination. Tankless melting prevents the adhesive degradation and char that can occur in conventional melter tanks while the temperature stability of Freedom-certified adhesives further reduces char potential. Reduced char minimizes clogged filters, applicators, and nozzles as well as the resulting maintenance, downtime, and lost production;
Freedom from manual adhesive filling. The integrated automatic fill system supplies room-temperature adhesive to the melter, minimizing operator involvement and labor costs while preventing missed adhesive beads from dry melter tanks. Operator exposure to molten adhesive is minimized, as is the potential for bending and lifting injuries associated with manual melter filling;
Freedom from parent machine mounting and integration limitations. Unlike traditional cube-shaped melters, the Freedom melter saves space using a vertical footprint that also allows it to be mounted almost anywhere within parent machinery, on a wall, or on available fixed or moveable mounting stands;
Freedom from confusing controls and diagnostics. A simple, intuitive, touch-screen minimizes the need for skilled operators and training;
Freedom from excessive adhesive use. Improved adhesive density reduces adhesive consumption while intermittent bead dispensing capability saves up to 50% adhesive. Waste associated with manual spilling and overfilling is also minimized.