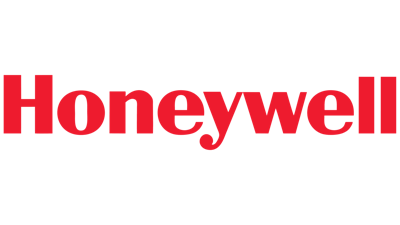
This content was written and submitted by the supplier. It has only been modified to comply with this publication’s space and style.
Production is anticipated to begin in 2025 and is projected to be the first commercialized waste plastics recycling facility to use Honeywell’s UpCycle Process Technology in Korea. The planned advanced recycling plant is expected to have the capacity to transform 30,000 metric tons of mixed waste plastics into Honeywell RPF per year.
“Honeywell’s UpCycle Process Technology not only allows us to reduce waste by expanding the types of plastics that can be recycled, but also displaces the need for fossil fuels in the creation of virgin plastics,” said Woo-Hyun Shim, vice president, GE Technology. “Enabling a circular economy for plastics in Korea is now possible through our licensure with Honeywell and their UpCycle Process Technology.”
Honeywell’s UpCycle Process Technology is a ready-now technology that utilizes molecular conversion, pyrolysis, and contaminants management technology to convert waste plastic to Honeywell RPF, which is then used to create new plastics. The UpCycle Process Technology expands the types of plastics that can be recycled to include waste plastic that would otherwise go unrecycled, including colored, flexible, multilayered packaging, and polystyrene. When used in conjunction with other chemical and mechanical recycling processes - along with improvements to collection and sorting - Honeywell's UpCycle Process Technology has the potential to help recycle nearly 90% of waste plastics. This would represent a considerable increase in the amount of waste plastics that can be turned into polymer feedstock1,2.
"GE Technology is the first company in Korea to license Honeywell’s UpCycle Process Technology, which will build upon GE Technology’s existing capability in waste collection and mechanical recycling," said Barry Glickman, vice president and general manager, Honeywell Sustainable Technology Solutions. "Honeywell’s technology can play a key role in driving a circular plastics economy to tackle the global challenge of plastic waste."
1 Assuming sorting and collection improves to recover most waste plastic, and chemical recycling, including Honeywell UOP UpCycle Process, is widely deployed. The 90 percent of waste plastics that could be recycled may change depending on the number of consumers or communities that have access to recycle waste plastics or the availability of recycle facilities.
2 Honeywell UOP analysis of US EPA Advancing Sustainable Materials Management: Facts and Figures 2018 and IHSMarkit 2019 world polymer consumption data.