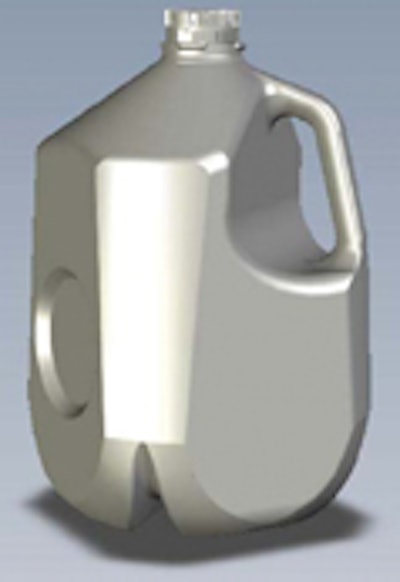
These bottles are shown below and were identified as original (A), cube (B), and stackable (C). The original and cube designs require reusable plastic crates and one-time use band straps for unitization, whereas the “stackable” design requires one-time use corrugated fiberboard slip sheets as well as stretch wrap for the same process.
This study considered a functional unit of one-gallon of packaged liquid milk for delivery to institutional customers (on-site users) and retailers within 250 miles from the processing and packing plant. Data related to milk production and processing was not included in this study. Environmental burdens of green house gases (GHG), energy, and solid waste were investigated based on material, process and transportation factors associated with the system boundary selected. The LCI-based results were used to compare and contrast these burdens and to provide a decision tool for adopting the primary container for the selected system with the lowest environmental impact.
As related to the raw materials, the stackable design contributed 34% and 26% higher GHGs and used 36% and 28% more energy per unit than the original and cube designs respectively. With respect to processing of these raw materials, the stackable design’s GHG and energy contributions were 8% and 10% higher as compared to the original and cube containers. These results can be attributed primarily to more resin used per container for the stackable container for enabling distribution without any crates. This disadvantage was overcome by the stackable container in the GHG and energy contributions as related to transportation where the original container’s contribution was 9% and that of the cube containers was 19% higher than stackable containers.