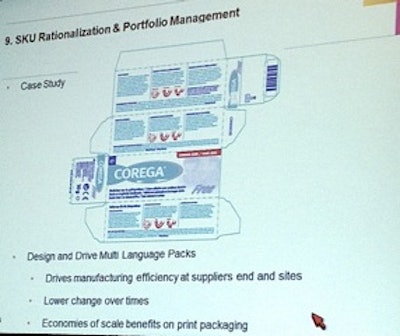
"Packaging supply chain efficiency is a mix of engineering, material science, standardization and logistics," Sriman Banjeree, head of packaging development for GlaxoSmithKline, Parsipanny, NJ., presented 10 packaging factors as they relate to manufacturing and supply chain efficiency. The points he made at Pack Expo 2012 go beyond the usual supply chain bullets; in addition to being an IoPP Certified Packaging Professional, Banjeree is a mechanical engineer with post graduate studies in packaging, holds a Master's degree in financial management.
1. Building new packaging design deficiencies in supply chain: Design to value: Whether you are improving an existing package or designing a new one, consider best practices from industries such as automobile and consumer electronics to design a package based on the best consumer insight and requirements. Consumer insights can drive tear-down and benchmarking and analysis of pack functions to enhance improve efficiency and reduce cost of goods.
Banjeree pointed to the example of a bag-in-container package that was redesigned to a direct-fill rigid container. The new container reduced size, materials and weight from the primary package for savings beyond materials, including greater transportation and retail shelf space savings--more units fit in the same space.
2. Packaging components manufacturing strategy: Taking advantage of "volumes of scale typically play a dry important role in bringing down your cost of goods," he says, pointing to the use of cube mold technology, which has offered many products greater economies of scale, faster cycle times, reduced manufacturing steps and transportation benefits. Reducing steps "leads to not only more time to manufacture; it leads to wastefulness, it can create bottlenecks, and all this definitely has an effect on your efficiency," said Banjeree.
Process selection is also is important; consider your options. While injection molding and compression injection molding can "give you the same result," Banjeree said, "each of them have their own pros and cons." Be willing to question past assumptions.
3. Packaging procurement efficiencies: How do you source components? Consider how to streamline your operation from the most expensive part of a given component to how you source and standardize raw materials. If your company is global, you'll likely benefit from suppliers who also have a global footprint, and efficient supply chains. But if you have five or six suppliers serving your markets with good, targeted efficiency, this can also be the best option. Treat inventory management and working capital as important requirements in sourcing materials and components.
4. Manufacturing online efficiencies and strategy: Standardize package sizes that can be used for multiple products; Banjeree noted one company that reduced nine separate blister packs to three, which greatly streamlined purchasing and overall manufacturing planning; reduced change-over times, and produced higher line utilization. Machines could then be standardized as well. Likewise, three diameters of bottles, or sizes of cartons can produce other benefits. Other tips include optimizing pack layout for higher throughput, and apply Kaizen, and other Lean manufacturing-related tools for continued improvements.
5. Packaging optimization: Design considerations in packaging include the ability to choose and optimize the materials you use. For example, shaving millimeters from a container can produce changes almost imperceptible to consumers' eyes, while providing significant weight and size reduction benefits across the supply chain. This applies to new packages as well as reverse engineering on existing packages. The keys are to poly design features to reduce weight; include the package's aspect ratio during your design and retain skilled personnel who understand material sciences. "Computer simulation," Banjeree said, "is going to be very important going forward." Finite element analysis will be one particularly relevant tool.
6. De-bottlenecking solutions to increase line speed: Identify bottlenecks on your production line at every step, including labeling; leaflet insertion; sizing; end-of-line processes and, as cited above, packaging material choices. Consider de-bottlenecking, also, by rethinking your conveyors, including factors such as modifying conveyor length or using multi-lane or helical conveyors. On the latter, Banjeree cited the use of longer or helical conveyors as a factor in reducing space and increasing line efficiency.
7. End-of-line solutions: How your end-of-line is set up will tell you a lot about efficiency," said Banjeree, adding that "while you can speed-up [upstream operations], you can't do anything" to increase line productivity if your end-of-line operations limit your capacity. Options for overcoming constrains include hand packing, case forming and semi-automatic case tapers and full automation of case erectors, case packers, case taping and stretch wrapping.
8. Sustainability in supply-chain: Trends favor the use of recyclable materials, more energy efficient machines to reduce carbon footprint and lightweighting. Bajeree also advised packaging professionals to look not just at using materials from today's sustainable sources but to "ooh to the future" to find emerging solutions. To reduce energy use, use materials where possible that require lower manufacturing temperatures.
9. SKU rationalization and portfolio management: Banjeree cited the "20/80 rule" in which "20% of business delivers 80% of profits." This can apply to 20% of efforts relating to of development and design driving 80% of the benefits. One example he cited was the use of multilingual labels where applicable. Banjeree cited the label for Corega brand denture-cleaning paste (see photo above), which used a multilingual pack to reduce complexity with packaging suppliers as well as in the plant, where changeovers once took a 20% toll on line productivity.
10. Warehouse management and transport efficiency: Tips include the use of standard and reusable pallets, use of floor space as well as height, adherence to first-in/first-out practices and understanding that the shortest distance in miles may not be there most efficient distance to route vehicles. Globally, Banjeree cited trends to watch in Asia (flexible laminates and sachets); Africa (cartons using recycled board); North America (concentrates and smaller-size packs) and Northern Europe (recyclable packaging).
Continued, future considerations include late-stage customization; increased application of digital technologies; advanced robotics and other flexibility-enhancing automation solutions; greater application of information technology to packaging efforts; more sustainable designs and the use of intelligent materials.