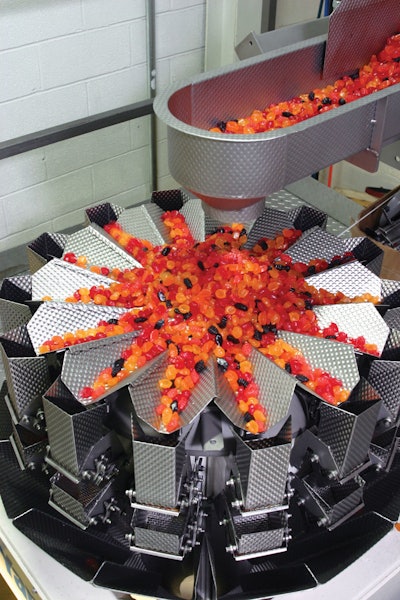
During the early morning of Sunday, August 28, Hurricane Irene roared into New York’s East Coast, dumping torrential rains. The Moodna Creek near Cornwall, NY, north of New York City, quickly flooded, sending a wall of water into the Cornwall Industrial Park, housing Superior Pack Group and several smaller businesses. The flood waters knocked down one wall of Superior’s building, and within just a few hours, the plant was four feet under water. Company management estimated a $2 million loss in equipment and product inventory.
First thing on Monday morning, August 29, company management, including president and CEO Israel Schiff and director of sales Joel Hirsch, had a daunting decision to make. “Do we stay in business,” Hirsch recalls them asking themselves. The answer was a resounding yes—they were not about to abandon their loyal customers. But the quickest way to get back to business was going to be in another facility. That same afternoon, they found an empty plant in nearby Harriman, NY, on enough land to allow for future expansions, should they need it. The lease was signed.
Lightning-fast transition
“There was nothing in the building but electrical power,” says Hirsch. “No plumbing, no air conditioning to maintain temperatures for food products, no security, phone or computer connections.” But the plant was very clean, and contractors were quickly hired to rectify the power problems.
However, getting back to business required equipment, too, and that was an even bigger problem. Some smaller packaging machines, such as ink-jet coders, printers, tapers and sealers “were completely gone,” Hirsch says. Some larger equipment had been knocked down by the force of the flood waters, and assessing the extent of damage necessitated a thorough cleaning first. Superior’s own quality control staff oversaw the cleanup effort, with the company’s entire staff working 24/7 in shifts to accomplish the task. Some equipment, it was determined, could not be salvaged. With others, emergency orders were sent for replacement parts. “We couldn’t even see what parts needed to be replaced until the machines were cleaned,” Hirsch explains. “We started slowly, machine by machine. Everything has been built to standards. Some are custom built.”
Unfortunately, since the hurricane is an act of nature, insurance did not cover the losses or replacements. Instead, Superior applied for Small Business Administration and other federal loans to cover expenses. In addition to losses from inventory and machinery, Superior suffered losses from modifications made to the former building, on which they had a very long lease.