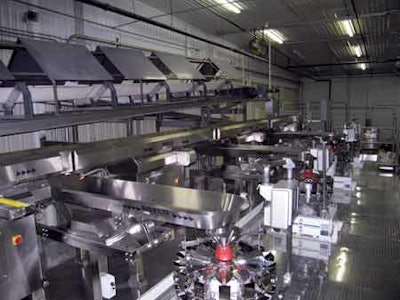
Richmond Baking, Richmond, IN, one of the largest baked goods manufacturers in the United States, produces cookies and crackers for retail markets, as well as industrial-ingredient coating systems for meat, fish, vegetable, and dessert processors. The company's preprinted, heat-sealable rollstock bag material structures and suppliers are considered proprietary.
Two years ago, the company recognized a need to increase bagging speeds on its cookie/cracker packaging lines. William Quigg, president of Richmond Baking, notes, “The scales we were using maintained desired throughputs, but the baggers we had in place were intended for large cereal bags and did not provide the bag-per-minute (bpm) rate required for our cookies. We need a minimum of 90 per minute to maintain satisfactory packaging efficiency.”
Two-phase upgrade
A colleague of Quigg suggested that Richmond Baking consider Robag bagging equipment manufactured by TNA (www.tnarobag.com). The baker put the equipment to the test and decided to purchase two Robag 3 vertical form/fill/seal machines.
As a result of this packaging equipment upgrade, Richmond Baking was able to negotiate a number of contracts to produce 1⁄2-oz bags of cookies and crackers, including snack crackers, cheese crackers, oyster crackers, animal crackers, and chocolate chip cookies (contract customer identities not disclosed). But taking on these contract packing jobs also necessitated a further packaging line expansion to achieve 300% more production capacity. Based on the positive results of the first upgrade, Richmond acquired four more Robag 3 machines and a TNA “Roflo” distribution system that feeds combination scales from Yamato (www.yamatocorp.com).