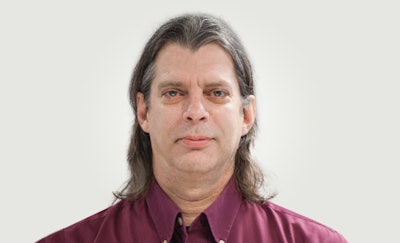
Are you in control of your Clean-In-Place (CIP) systems and are they transparent enough to tell you the full story?
Over the years, I have seen many CIP Systems programmed in a variety of ways. And while the intention is always the same—to get stuff cleaned reliably and efficiently—the process is often difficult to follow. Such was the case for one of our customers, a major dairy manufacturer. Struggling to meet the demands of production and sanitation, they needed to modify their CIP systems to allow for better control over all aspects of the cleaning process, as well as have the flexibility for future process additions. The problem, however, was that their multiple CIP systems had been developed by different programmers over the years. As a result, making a simple modification to the system had become a tedious and time-consuming endeavor. Tasked with developing a standard that could be applied to each system, our team determined that leveraging a time-tested Avanceon approach—creating pin charts, would be a quick and efficient solution, provide ease of use, and give the customer the most visibility and flexibility in their cleaning process.
Once implemented on the initial pilot phases, the impact was immediate. The sanitation manager is now qualified and able to review and optimize each circuit-cleaning sequence through a simple-to-use interface. Today, cleaning optimization takes minutes where, historically, it would require—over the course of hours—the time and skill set of an engineer to implement. In addition, the manufacturing team can now analyze the historical data of each cleaning process and identify areas where further optimization measures will have the most impact to the operations, showing steps to be taken to further reduce chemicals, water usage, and overall costs. Recently, they found a way to save 10-15 minutes of rinsing per tank wash and—at the same time—achieve better results! Let that sink in. Saving time and water with more predictable results!
It starts with lowering the veil of complexity and opening transparency to the system. Once the people who touch the process daily know what the systems are doing, they can identify and fix the issues that have been plaguing its efficiency and effectiveness—and sometimes discover issues of which they were not previously aware.
Let us know if you have taken a similar approach to improving your operations be it CIP or other. We’d love to compare notes!
Eric Gruber is a principal engineer at Avanceon, a certified member of the Control System Integrators Association (CSIA). For more information about Avanceon, visit its profile on the CSIA Industrial Automation Exchange.