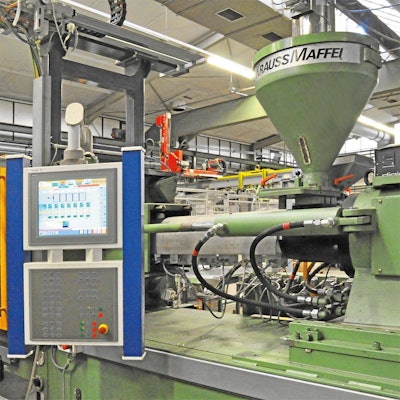
Pneumatics and hydraulics may be too old fashioned for some engineers, but not for Klaus Lange. The operations engineer at Haefner and Krullmann GmbH near Bielefeld, Germany has become a believer in the benefits of bringing hydraulic machinery into the digital age. For he and his colleagues at this producer of thermoplastic spools and environmental containers experienced these benefits firsthand when they joined a growing group of manufacturers who are integrating electric drives with fluid power.
The integration of these technologies occurred at Haefner and Krullmann when the operations team there retrofitted four hydraulic injection-molding machines. For more than 20 years, induction motors had been driving the old swivel-angle and fixed-displacement pumps on the machines. Although the machines were mechanically sound, their motors ran continuously, even when the machines were idle. The pumps run had wasted energy and the practice had just become too costly.
For this reason, management decided that an update was in order. Hence, the four molding machines received new Simotics M-1PH8 servomotors from Siemens AG (www.usa.siemens.com/industry) of Erlangen, Germany and IPVP series hydraulic gear pumps from Voith Turbo H+L Hydraulic GmbH & Co. (www.us.voithturbo.com/hydraulic-systems.htm) KG of Rutesheim, Germany. Each of the synchronous servomotors is driven from a Siemens Sinamics S120 converter equipped with a Sinamics Control Unit 310.
In contrast with the old design, the servomotor is now coupled directly to the hydraulic pump, and “the motor runs only when the piston in the hydraulic cylinder needs to move,” explains Mathias Radziwill, industry business development manager for the plastics group at Siemens . “The positioning of the hydraulic pistons, the adjustment of the pressing speed, and the setting of force values are done without control or proportional valves.”
Consequently, the hydraulic system need not be over-sized, as such systems often are in order to avoid secondary effects such as cavitations, gas venting, and compression loading, Radziwill says.
Besides being right-sized and not running when cylinders are idle, the servomotor concept also saves energy by using a new hydraulic oil that ExxonMobil tested in this application. Because the oil has a viscosity of 32 cp, it generates less heat while the pump is working and can operate at 35 degrees C, rather than 45. Hence, very little cooling is necessary.
Other benefits of the upgrade included the ability to monitor the performance of the pump with a power meter on the Profibus network. Setup technicians, for example, can now see the impact of certain machine settings and, in turn, fine-tune their “feel” for energy-efficient injection molding. Because of these updates, energy consumption fell by 48 percent, and the retrofit paid for itself within a few years.
Vendors report that such savings are routine when variable-speed motors replace conventional motors that run continuously. “A servo pump has a high dynamic performance, increases the machine yield, and reduces energy costs by up to 50 percent,” says Radziwill at Siemens.
In other applications, such as lifting platforms or hydraulic presses, these variable-speed motors have the additional benefit of being able to recover energy stored in the system after a few cycles. “During the fast down-movement of the press ram or lifting platform, hydraulic oil flows via a pump into the oil reservoir,” explains Radziwill. “The servomotor controls speed, and electric power is stored in the intermediate circuit of the servo system during the generator operation of the servomotor.”
Braking also occurs by means of the servomotor. “For the subsequent pressing function, the motors use the braking energy from the intermediate circuit of the servo system that has been stored,” Radziwill continues. “In addition, the spring energy—stored in the compressed hydraulic oil at the end of the press cycle—also drives pump and servomotors in the relief cycle, thereby storing energy in the intermediate circuit.”
Brains and brawn
Pumps are not the only place where builders of molding machines are using hybrids of hydraulic and electric drive technology. Berlin-based Bekum Machine Builder GmbH, for example, has cooperated with Bosch Rexroth AG (www.boschrexroth-us.com) in Germany in developing a different kind of hybrid drive for closing its blow-molding machines. This precision drive can maintain high forces over extended periods, yet execute fast changes in direction.
Key to the design is a hydraulic gearbox between the electric drive and the linear axis for the closing mechanism. Not only does the gearbox convert rotary motion into linear movement, but it also enables switching between rapid and power modes in the stroke. Rather than using a conventional hydraulic tank and displacement unit, this drive relies on a locking mechanism in the hydraulic gearbox to hold the closing force without maintaining torque on the drive and expending more energy than necessary.
Developments like these promise to give hydraulics a whole new image and, in the process, breathe new life into the technology. “A longstanding prejudice against hydraulics has been that it’s strong, but stupid,” notes Jan Komsta, manager of new technology and simulation at Bosch Rexroth. “This is no longer true. Hydraulic power not only is strong, but also is now efficient, reliable, and high tech.”
This newfound reputation for having intelligence is largely due to the integration of hydraulics with digital controls and smart electric drives, as well as to the development of hydraulic-dedicated control algorithms capable of accounting for the compressibility of hydraulic fluids. “Because of modern closed-loop techniques, including nonlinear ones, it has become easier to control movement and forces very precisely and reliably,” says Komsta.
Onboard electronics also make it possible to integrate valves with other plant automation and to plug hydraulic drives into Profibus or Ethernet. Not only does this ability to communicate with other parts of the plant help hydraulics to fit into flexible automation, but it also permits its participation in such management functions as condition monitoring and diagnostics.
In the case of pneumatic machinery, perhaps the most important development has been the use of fieldbus connected to a programmable logic controller (PLC), according to Bill Janssens, national automotive manager for Festo Corp. (www.festo.com) headquartered in Hauppauge, N.Y. “Our designs tend to have banks of valves—all centralized with a fieldbus interface,” he says. “Wiring is reduced significantly, which in turn reduces installation time and overall cost.”
Tools for optimization
Computing power makes another important contribution to hybrid technology: Software now helps design engineers to size the components and optimize their interaction. These tools can help designers avoid the inefficient over-sizing that is common in both hydraulic and pneumatic systems. For example, “designers of pneumatic systems often say, if a 25-mm bore cylinder works well, I’ll use a 32 to give me some extra force should I ever need it,” offers Janssens.
Consequently, redesigning many pneumatic, as well as many hydraulic, systems with components sized correctly for the required forces and actuation times can save significant amounts of money. Consider a packaging machine that one of Festo’s engineers studied for a machine builder. The engineer analyzed the air consumption to establish benchmarks for the run, idle and off modes. Then, he right-sized the oversized components and eliminated inefficiencies, such as the banks of pressure regulators that had been necessary simply to accommodate the oversized cylinders. He also installed some simple on-off valves and altered the PLC programs to stop the machine from just bleeding air to atmosphere when it was at rest.
“Optimizing the design and reducing unnecessary components reduced 20 percent of the pneumatic cost of the machine,” reports Janssens. “It reduced the compressed air consumption by 25 percent in run mode and about 35 to 40 percent in idle mode.”
For hydraulic applications, advanced software tools can select a suitable motor-drive combination based upon the load and required motion entered by the user. Motion analysis software can also help engineers to optimize performance. “One big challenge in machine design is that there is often an unclear relationship between the selection of mechanical components and system performance,” notes Jim Gegg, global product manager at Rockwell Automation (www.rockwellautomation.com). “With performance and simulation analysis, engineers can investigate machine behavior and select a mechanical design—along with the optimum controls and software—that will maximize performance.”
Some of these tools can also conduct dynamic thermal modeling to account for the affects of temperature. Others, like advanced tuning simulation, can help to predict how the machine will perform in the field by emulating the tuning of an axis in the programming software and simulating the behavior of the load, motor and drive. “The software then factors in mechanical compliance or backlash to provide a realistic performance evaluation,” says Gegg.
Such software and the other innovations that have promoted the integration of hydraulic and electric drives could slow the migration away from hydraulics. “About 20 or 30 years ago, there were some predictions that electrical drives would replace all hydraulics sooner or later,” recalls Komsta at Bosch Rexroth. He dismisses the prediction as having been unrealistic: “It’s hard to imagine how some plants would be able function without fluid power. It can’t be easily replaced where high torques and high power density are required,” he says.
Currently, the practical limit for replacing hydraulics completely with electric motors is usually between 100 kW to 150 kW. “After that, the motors get really large and expensive,” says Robert Muehlfellner, director of automation technology at B&R Industrial Automation Corp. (www.br-automation.com) based in Roswell, Ga. “Plus, you need a drive for each motor.” In hybrid systems, the hydraulic actuators are smaller and less expensive.
Instead, Komsta and his colleagues at Bosch Rexroth see the integration of fluid power with electronic devices as an emerging discipline in its own right and have dubbed it “fluidtronics.”
“This new field in fluid power is developing really fast,” Komsta says.
Don’t let it take you by surprise.
>> Click here to read how replacing pneumatics with servos can improve motion control.