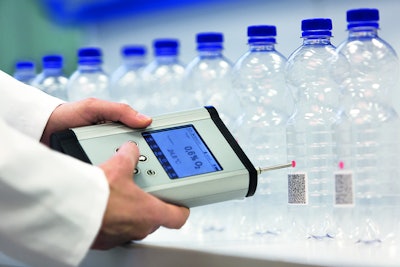
Many goods are sensitive to oxygen and have to be protected by the appropriate packaging. Optical oxygen sensors offer fast and easy analysis, even measuring oxygen traces, when checking packaging materials, the tightness of closures, and the oxygen content in the headspace of packages.
These sensors are available in different designs, for different application purposes, and can be used in filled and empty packaging to determine the permeability of the material or the oxygen content inside the packaging in ppm to ppb ranges.
Optical oxygen sensors contain a thin layer of fluorescent oxygen-sensitive dye. The sensors are excited with light of a certain wavelength and emit fluorescence in response. The presence of oxygen molecules changes the fluorescence signal of the sensor and by measuring the quenching of fluorescence the oxygen concentration in liquid or gaseous samples can be determined. Unlike Clark-type electrodes, optical oxygen sensors do not consume oxygen in the measurement process.
The excitation light and the emitted fluorescence signal of the sensor are transferred via a polymer optical fiber from and to the oxygen meter, which displays the oxygen values. The greatest advantage of chemical optical sensors compared to other measurement techniques is that they can be operated contact-free, i.e. the sensor can be attached to the inside of a transparent container and then be read out through the container wall by holding an optical fiber connected to the oxygen meter to the wall opposite the sensor (see Fig. 1).
There does not have to be direct physical contact between sensor and oxygen meter when measuring in transparent vessels or through optical windows. For non-transparent containers other sensor designs, like the needle-type microsensors can be used. These sensors have the oxygen-sensitive dye coated to the end of an optical fiber housed in a syringe needle.
With this steel needle packaging material can be pierced and the oxygen content in gas and liquid inside the container can be determined (see Fig. 2). Their high spatial resolution and fast response times make these sensors suitable for oxygen measurements in the smallest volumes.
The optical oxygen sensors are available for measurements in normal oxygen range (detection limit 15 ppb dissolved oxygen, 0 – 100 % O2, sensor type PSt3, PreSens GmbH) and for measuring oxygen traces (detection limit 1 ppb dissolved oxygen, 0 – 4.2 % O2, sensor type PSt6, PreSens GmbH).
Finding the right closure and material
Especially in the food and beverage industries, the amount of oxygen inside packaging is of major importance, as it can lead to oxidative deterioration and shorten the shelf life of products. Here optical oxygen sensor spots can be applied in a broad range of applications. Sensor spots are small round foils with 5-mm diameter containing the oxygen-sensitive dye; sensor spots approved for use with food products are available for food and beverage applications.
These sensors are designed for contact-free read-out. In transparent or only slightly colored packaging the sensor spots can be attached to the inside wall, below filling level or in the headspace area of the container. After filling and closing the container the oxygen content inside the product and the headspace can easily be determined from the outside. This technique has already been applied to investigate the oxygen content in glass beverage bottles with different closures—crown caps and swing stoppers. However, oxygen is not only dissolved in the product, or taken up while filling, but it also migrates out of—or permeates through—the packaging material into the product.
Here optical oxygen sensors can be applied to investigate the amount of oxygen ingress in containers. The containers are filled with oxygen-free medium (liquid or gas) and the increase in oxygen content inside the containers is quantified in long-term measurements. If the container is transparent or only slightly colored, an oxygen sensor spot can be glued to its inner surface and the packaging can be closed. For non-transparent or colored containers such as plastic beverage bottles, which can act like a filter for the excitation and emission light, special closures with integrated oxygen sensor are offered.
New oxygen meters with barcode scanner (Fig. 1, Fibox 4 trace, PreSens GmbH) facilitate working with numerous sensors integrated in different vessels. This technique has already been applied to investigate the oxygen barrier properties of differently treated PET bottles, with or without a special coating, and with an oxygen-consuming additive in the bottle material. Results showed that a combination of coating the bottle and adding oxygen scavengers to the bottle material will protect the product best and ensure longest shelf life (see Fig. 3).
Measurements in the product and headspace
Not only PET or glass bottles but every type of container can be investigated with optical oxygen sensors. Needle-type oxygen microsensors offer many advantages in quality control in non-transparent packaging, including blisters or cans, and for measurements in smallest volumes.
A septum is attached to the packaging to avoid oxygen entering the container when piercing through its wall. This type of optical sensor can be used to determine the oxygen content of headspace and liquid inside the packaging in one measurement. With its fast response time stable measurement values can be obtained within seconds when the sensor enters the headspace. Then it can be pushed into the liquid inside the packaging and again the oxygen content now in the liquid phase is determined in a few seconds.
Also when measurements in small volumes have to be conducted, like in blister packaging or vials for pharmaceuticals, these sensors with sensor tips of down to 50 µm diameter are the measurement tool to manage determining the oxygen content. As the sensors do not consume oxygen during the measurement process precise results can be obtained even in volumes of a few mL.
Optical oxygen sensors are versatile and easy-to-use tools for quality assessment during production and filling processes, or for testing material properties and leak tightness of packaging. With optical measurement systems oxygen ingress in packaging can be determined under realistic conditions. (e.g., in carbonized liquids under pressure).
Sequential measurements can be conducted, which means that the equipment is not blocked for the complete measurement time, as is the case with other oxygen measurement techniques. These systems are already applied at many different stages from material research, over production control, to quality assessment of the packaging filled with the final product. In combination with new handheld oxygen meters these sensors are versatile tools for most different requirements in the packaging industries.
--Article by C. Huber, PreSens Precision Sensing GmbH, Regensburg, Germany