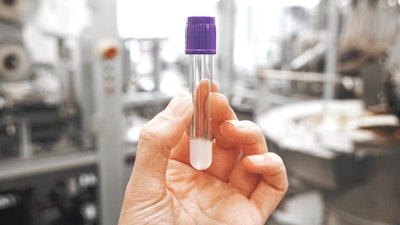
This content was written and submitted by the supplier. It has only been modified to comply with this publication’s space and style.
Optima Automation recently completed a comprehensive system to assemble blood collection tubes, including the dosing of additives. This consists of an OPTIMA BCT-200 processing line and an OPTIMA BCA-200 assembly machine. It was not possible to perform the Eastern European customer's Factory Acceptance Test (FAT) with them being present at Optima due to the pandemic. The machine acceptance was carried out online and streamed live for the customer to avoid any risk of delaying the project.
In healthcare, blood diagnostics are very important. Important information on the course of Covid-19 infection is also being obtained currently by blood tests. The quality of blood diagnostics does not just depend on the test itself, for example its sensitivity. Likewise, a blood collection tube must meet strict qualitative criteria in production in order to be able to provide safe, conclusive results. Optima Automation has developed a system especially for blood collection tubes which combines all the functions required and perfectly coordinates the individual processes.
In the Eastern European customer's current project, Optima Automation's modular machine base was able to cover the entire process, from the assembly of the closing caps to the packaging of finished blood collection tubes. Part of the customer's requirements was high performance and high flexibility.
The first element in the solution is the OPTIMA BCA-200 assembly machine for the blood collection tube caps, which are made up of several components. The OPTIMA BCA-200 precisely assembles these components by pressing in rubber plugs into the caps. Several cap formats can be processed by the machine. Furthermore, the fully assembled caps are tested inline.
Perfect interaction of the two machines
Once again, all the process steps required for assembling and packaging the blood collection tubes are integrated in the linear OPTIMA BCT-200. In terms of product quality, the dosing of the liquid to gel-like additives, the integrated drying and the sealing under vacuum are to be pointed out. In addition, numerous features and design details contribute to both high product quality and high machine efficiency. Such as the precise feeding and assembly functions as well as the specific design of the workpiece carriers and grippers. Hygiene functions and various in-process controls are included in the machine concept as well. To provide a total solution, the line also covers labeling, packing in polystyrene trays and shrink wrapping.
In order to keep the operator efforts as low as possible, the individual product parts are stored on the line as bulk. Specific sorting units and separating solutions, which are also made by Optima Automation and are tailor-made for the line, are used to automatically feed the individual parts into the linear system. This solution from a single source ensures that the interfaces are designed in the most effective way possible. This makes a significant contribution to the subsequent smooth running of the process. The flexible system can be changed over to different product formats in a short period of time.
Live on site: a virtual FAT for the customer
Optima Automation organized a virtual FAT for the customer under pandemic conditions. Consequently, the system functions could be tested over two days in December, and their compliance with the contract specifications was demonstrated. Optima Automation had defined a process for this in advance with the customer. Using a variety of cameras, webcams and headsets for live streaming, the customer was involved extensively. The customer had an overall view of the system and was able to follow details and processes and ask technical questions. Included in the FAT was a document review and a continuous operation of the system. A plan for subsequent commissioning also was agreed. Delivery to the customer's site was still able to take place in December. The final commissioning of the system by Optima Automation staff at the customer's site has already begun, despite the worsening pandemic conditions throughout spring 2021.