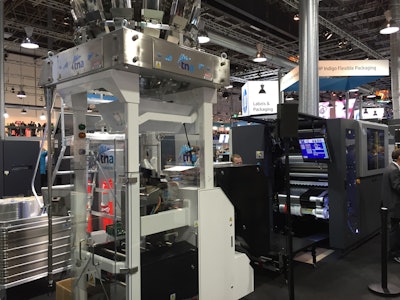
Produced by Messe Dusseldorf (www.mdna.com), drupa has a heavier dose of packaging than ever before. One exhibitor based in France put it this way: “In years past we’ve seen an ‘ink-jet drupa,’ which was followed by a ‘digital drupa.’ But this year is clearly the ‘packaging drupa.'”
Two good examples of printing technology aimed squarely at the packaging sector were in evidence at Hall 17, which was occupied entirely by HP. On display and in operation was HP’s Pack Ready concept, which eliminates the cure time ordinarily required when substrates are being laminated together. Because the Pack Ready laminator creates a film that doesn’t require curing, it connects directly to an in-line vertical form/fill/seal machine to produce pouches with no work-in-process downtime. At drupa, a vf/f/s machine from tna was producing single-size snack bags from a roll-fed substrate that was coming right out of the Pack Ready laminating system (see photo).
Also shown by HP was a digital print and embellishment system that will be released to the marketplace in late 2017. It adds digital embellishments to the printing pass, enabling a fully digital production line with a single point of control for labels including foiling, spot varnish, and more. Unlike conventional analog printing and embellishment--which requires a high level of expertise in various print technologies and takes considerable time and effort—HP Indigo’s Digital Combination printing will considerably reduce the level of complexity with all parameters set and controlled by the press. “One file goes to the system, so process flow is optimized,” says Christian Menegon, Worldwide Business Development Manager at HP Indigo.
This system represents yet another arrow in the quiver of Consumer Packaged Goods companies seeking to use personalization as a means of engaging the consumer. “It’s no longer enough to target ‘consumers,’” says Menegon. “Brand owners now want to target each consumer individually. So personalization and customization will continue to be a shaping influence in packaging for some time to come. The biggest hurdle that has to be overcome right now is that the manufacturing environment just isn’t conducive to this kind of thing. Brand owners have the will to personalize but not the ability, due largely to supply chain issues. In the short run, they can get over this hurdle by relying on third party suppliers or contract arrangements. But in time I expect they will figure out ways to execute on personalization in-house.”
While HP’s digital embellishment capabilities are still in the development stage, MGI has been selling and installing its system for some years now. In fact, MGI with its JETVarnish 3D/iFoil Digital Enhancement Press was named winner of the newly inaugurated Leadership in Innovation Award in this year’s DuPont Packaging Awards Competition. But now the firm, based in France but with offices in Florida, has come up with an entirely new concept called Alphajet. Scheduled to be installed in a beta site by the end of the year, Alphajet has a unique transport system whereby 18 trays take sheet-fed paper through a number of digital printing stations whose print heads are from Memjet, Kyocera, and Konica Minolta. Also in place is MGI’s digital foiling station so that a folding carton, for example, can be embellished. But wait, there’s more. The Alphajet also incorporates “intelligent printing” because incorporated into it is a station where a Ceradrop (www.ceradrop.fr/en) Digital Materials Deposition Platform adds printed electronics on the back of a carton substrate. As if that weren’t enough, the system also includes Aerosol Jet technology that permits it to digitally print cans or other multidimensional objects.
At the Eastman Kodak (www.kodak.com) booth, the Uteco (www.uteco.com) Sapphire press for labels was making its debut. According to Don Allred, Director of Sales & Marketing at Kodak, this press can print film labels with water-based inks at production speeds to 600 feet/min, something no other press can do. Kodak’s digital ink-jet print heads (see photo), its inks, and its chemistry know-how where primers are concerned all play key roles in the press’s ability to run at such speeds. Also crucial is the technology used to overcome the inherent tendency for film to stretch and thus cause registration problems as it goes through the print stations. According to Allred, some 30 servo motors are deployed in a way that allows the film rollers to be so finely and positively controlled that contact tension is always held to perfection, even at 600 feet/min.