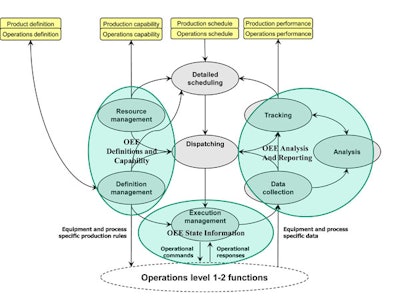
Since January, a group consisting mainly of technology providers, integrators, and builders and buyers of packaging machinery have been hammering out what they call the MES (OEE, Reliability) Definition Team Charter. The key goal behind the team's efforts is to define MES functions in a standard way.
In August, ISA-95 chairman Keith Unger will present the Charter to the ISA-95 committee. That committee is focusing on completion of ISA-95 Part 4, which revolves around the object model and attributes needed to support MOM (Manufacturing Operation Management), the term that is beginning to replace MES (Manufacturing Execution System). Last week I caught up with Stone Technologies' Kirk Weiss, who is the project manager of the MES (OEE, Reliability) Definition Team Charter, to learn more about what the group has been up to.
"We want to put together definitions so everybody has a common language for exchanging information related to Overall Equipment Effectiveness and reliability," says Weiss. "That way, when we get information from the control layer on the state of a piece of equipment, it will be in a standard form that the applications above would be able to consume and then generate actionable reports on."
And why has that information not been readily available in the past?
"Mainly because there's too many one-offs," says Weiss. "Each control vendor tends to do their own thing to such an extent that vital information is simply not available. Then you have to have somebody go in and develop it at the control layer and configure that information within some system that would track or report on OEE type information."
What it all comes down to, says Weiss, is that there has been a dramatic shift in our understanding of the information packaged goods manufacturers need and when they need it.
"It's a different way of looking at where problems really are and how quickly they can be addressed," says Weiss. "In the past people would have a team conduct an audit of a manufacturing operation. But it's no longer acceptable to capture information throughout the day and then enter it into a spread sheet that night or the next day. That time lag leads to efficiency losses you can never recover."
The diagram shown here, says Weiss, illustrates the correlation between the OEE footprint and the generic ISA-95 MOM.