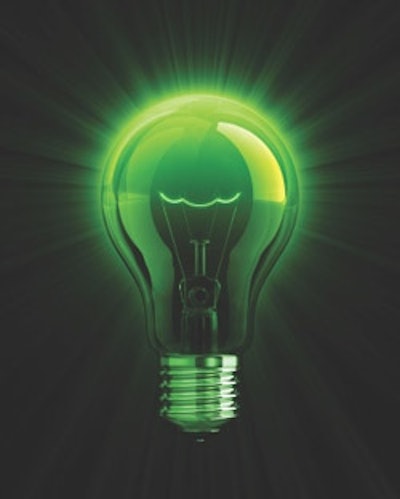
Responses related to training and to checklists were among the most
frequent, including the following recommendations, which we hope you
will find useful for your next project.
"Send your factory personnel to the equipment manufacturer for training before you receive shipment of your new machines," says Bryan Sinicrope, vice president, sales and marketing, A-B-C Packaging Machine Corp. "This gives your employees a good understanding of the equipment and a better comfort level during start-up and operation. Training is especially important when putting in a new line or when installing multiple machines, as factory personnel have a lot to learn and understand. If they have prior training on the individual machines, it makes things go much more smoothly."
Paul King, Weber Marking Systems' manager of labeling systems, assembled an extensive list of things to consider when planning an install, which we've summarized, along with a separate checklist for start-ups that you can read below. King says that a lot of the preparation for equipment installation really boils down to taking a commonsense approach, and includes the following:
• It costs you money to install or start up a piece of equipment, so ensure that everyone who needs to be there is present.
• Check and double-check that you have all of the equipment on-site before even scheduling the install.
• Do not gamble that a critical piece of equipment or a critical resource will show up just-in-time.
• Check equipment dimensions: Will it fit in the door? Will it fit in the install location?
• Can it be moved to the installed location from the receiving dock? Is it blocking an aisle?
• Does the operator have complete access to the equipment? And does the service tech have the needed access after the unit is installed?
• Make sure that you understand the electrical, pneumatic, and other requirements of the equipment.
• Check location for needed resources in relations to equipment location.
• Do these need to be changed before the day of installation?
• Check with the vendor on what company resources they will need prior to install.
• Do they need electrical assistance?
• Do they need they need pneumatic assistance?
• Schedule the installation when company resources are available or make company resources available.
• Remember, you are paying for both your employees’ time and your vendor’s time. Do not waste it.
Terry Zarnowski, sales and marketing director, Schneider Packaging Equipment, offers this advice: To minimize start-up time and to maximize success, it is important to use the actual product produced from upstream equipment that the machine will see in actual production. Otherwise it is possible that the product’s ‘personality’ can change, affecting how a product flows through downstream equipment.
Chris Rempe, senior product manager, Automated Packaging Systems, listed these key steps:
1. Ensure that the proper utilities (air, power, etc.) are present before the installation begins. For equipment requiring compressed air, it's essential that the air be clean and dry.
2. Wait until the installation and training have been completed before scheduling full production. Delays can occur for a variety of reasons; do not assume that everything will go perfectly.
3. Take full advantage of the training provided during installation. Make sure that representatives from all shifts have been trained and have a thorough understanding of the machinery operation. This will minimize the learning curve and maximize productivity.
4. When equipment from more than one manufacturer is being integrated on-site, encourage those companies to talk to each other well before the equipment is delivered. This will help ensure that the pieces will work together both mechanically and electrically.
Bob Ries, product manager for Thermo Fisher Scientific, shared the following checklist:
• Make sure you read in detail the quote describing all the features of the system you bought. This will assure it will do everything you need.
• Request a layout drawing of the system prior to install. This will verify line height, direction, clearances, and the location of key things like reject devices and operator interfaces.
• Ask the vendor for a preinstallation survey or checklist. This will force you to go over everything the vendor will need before they arrive.
• Hire the manufacturer of the equipment for the installation and beware of third parties that are not qualified or certified. This is particularly important if you are trying to schedule installation during a short shutdown period.
• Determine in advance what performance tests you want to run after the system is installed.
John Eaton of Smurfit-Stone Corp. advises that companies conduct a "rigorous runoff—extended test runs under production conditions before the equipment is shipped from the vendor." Eaton feels that packagers should insist on the test even if the model matches what they have installed before. He also recommends that the packaging materials used be sourced from the exact plant that will source the real-world supplies.
Trace Bocan, marketing manager of Matthews Marking Products, offered two recommendations:
1. Provide a completion checklist to be signed by both the customer and supplier at the end of the start-up and installation. This ensures that the customer has been satisfied with the installation and that there is agreement that everything was covered by the supplier. It also helps to avoid having customers calling later and suppliers incurring additional costs to revisit.
2. Know ahead of time who will be at the installation and start-up, and have the supplier/customer exchange and record the names of all those present as verification and for any subsequent follow up.
Sales engineer Brian Mack of CIVision, LLC, says, “Make the start-up as simple as possible. If a complete line is being installed, then each part of the line should be qualified independently starting at the beginning.
“If there are different-format products or if changeovers are required, then choose an extreme-format product—large or small—and start up the line from beginning to end and qualify that format. Once qualified, change to the other extreme. Many customers rush through many changeovers trying to touch on each format and end up with a very inefficient test with most of the time spent changing over rather than qualifying the line.”
FlexLink director of marketing Paul Jarossy encourages packagers to get the conveyor vendors involved early, even before they may be ready to talk specific details on their layout. "Most companies install and bolt down the equipment to the floor and then call us," he says. "If they had gotten us involved early, we could have saved them 30 to 50 percent in their floor-space requirements and improved their process."
A checklist for start-ups
The following information is provided by Paul King of Weber Marking specific for start-ups after you've followed his installation advice as noted above:
• It is your equipment–take responsibility for it from the very beginning.
• Make sure your employees take responsibility for it.
• The vendor is leaving tomorrow; you need to know how to run and maintain the equipment.
• Do not plan on starting up a new piece of equipment today and putting it into full production tomorrow.
• There is a learning curve.
• Make sure the operators are there to learn the equipment.
• No distractions–this should be their full-time job during start-up.
• Make sure maintenance is there to learn how to service the equipment.
• If products or supplies are needed to run in the machine during start-up, make sure they are immediately available
• Do not plan on shipping the test product to a customer.
"Send your factory personnel to the equipment manufacturer for training before you receive shipment of your new machines," says Bryan Sinicrope, vice president, sales and marketing, A-B-C Packaging Machine Corp. "This gives your employees a good understanding of the equipment and a better comfort level during start-up and operation. Training is especially important when putting in a new line or when installing multiple machines, as factory personnel have a lot to learn and understand. If they have prior training on the individual machines, it makes things go much more smoothly."
Paul King, Weber Marking Systems' manager of labeling systems, assembled an extensive list of things to consider when planning an install, which we've summarized, along with a separate checklist for start-ups that you can read below. King says that a lot of the preparation for equipment installation really boils down to taking a commonsense approach, and includes the following:
• It costs you money to install or start up a piece of equipment, so ensure that everyone who needs to be there is present.
• Check and double-check that you have all of the equipment on-site before even scheduling the install.
• Do not gamble that a critical piece of equipment or a critical resource will show up just-in-time.
• Check equipment dimensions: Will it fit in the door? Will it fit in the install location?
• Can it be moved to the installed location from the receiving dock? Is it blocking an aisle?
• Does the operator have complete access to the equipment? And does the service tech have the needed access after the unit is installed?
• Make sure that you understand the electrical, pneumatic, and other requirements of the equipment.
• Check location for needed resources in relations to equipment location.
• Do these need to be changed before the day of installation?
• Check with the vendor on what company resources they will need prior to install.
• Do they need electrical assistance?
• Do they need they need pneumatic assistance?
• Schedule the installation when company resources are available or make company resources available.
• Remember, you are paying for both your employees’ time and your vendor’s time. Do not waste it.
Terry Zarnowski, sales and marketing director, Schneider Packaging Equipment, offers this advice: To minimize start-up time and to maximize success, it is important to use the actual product produced from upstream equipment that the machine will see in actual production. Otherwise it is possible that the product’s ‘personality’ can change, affecting how a product flows through downstream equipment.
Chris Rempe, senior product manager, Automated Packaging Systems, listed these key steps:
1. Ensure that the proper utilities (air, power, etc.) are present before the installation begins. For equipment requiring compressed air, it's essential that the air be clean and dry.
2. Wait until the installation and training have been completed before scheduling full production. Delays can occur for a variety of reasons; do not assume that everything will go perfectly.
3. Take full advantage of the training provided during installation. Make sure that representatives from all shifts have been trained and have a thorough understanding of the machinery operation. This will minimize the learning curve and maximize productivity.
4. When equipment from more than one manufacturer is being integrated on-site, encourage those companies to talk to each other well before the equipment is delivered. This will help ensure that the pieces will work together both mechanically and electrically.
Bob Ries, product manager for Thermo Fisher Scientific, shared the following checklist:
• Make sure you read in detail the quote describing all the features of the system you bought. This will assure it will do everything you need.
• Request a layout drawing of the system prior to install. This will verify line height, direction, clearances, and the location of key things like reject devices and operator interfaces.
• Ask the vendor for a preinstallation survey or checklist. This will force you to go over everything the vendor will need before they arrive.
• Hire the manufacturer of the equipment for the installation and beware of third parties that are not qualified or certified. This is particularly important if you are trying to schedule installation during a short shutdown period.
• Determine in advance what performance tests you want to run after the system is installed.
John Eaton of Smurfit-Stone Corp. advises that companies conduct a "rigorous runoff—extended test runs under production conditions before the equipment is shipped from the vendor." Eaton feels that packagers should insist on the test even if the model matches what they have installed before. He also recommends that the packaging materials used be sourced from the exact plant that will source the real-world supplies.
Trace Bocan, marketing manager of Matthews Marking Products, offered two recommendations:
1. Provide a completion checklist to be signed by both the customer and supplier at the end of the start-up and installation. This ensures that the customer has been satisfied with the installation and that there is agreement that everything was covered by the supplier. It also helps to avoid having customers calling later and suppliers incurring additional costs to revisit.
2. Know ahead of time who will be at the installation and start-up, and have the supplier/customer exchange and record the names of all those present as verification and for any subsequent follow up.
Sales engineer Brian Mack of CIVision, LLC, says, “Make the start-up as simple as possible. If a complete line is being installed, then each part of the line should be qualified independently starting at the beginning.
“If there are different-format products or if changeovers are required, then choose an extreme-format product—large or small—and start up the line from beginning to end and qualify that format. Once qualified, change to the other extreme. Many customers rush through many changeovers trying to touch on each format and end up with a very inefficient test with most of the time spent changing over rather than qualifying the line.”
FlexLink director of marketing Paul Jarossy encourages packagers to get the conveyor vendors involved early, even before they may be ready to talk specific details on their layout. "Most companies install and bolt down the equipment to the floor and then call us," he says. "If they had gotten us involved early, we could have saved them 30 to 50 percent in their floor-space requirements and improved their process."
A checklist for start-ups
The following information is provided by Paul King of Weber Marking specific for start-ups after you've followed his installation advice as noted above:
• It is your equipment–take responsibility for it from the very beginning.
• Make sure your employees take responsibility for it.
• The vendor is leaving tomorrow; you need to know how to run and maintain the equipment.
• Do not plan on starting up a new piece of equipment today and putting it into full production tomorrow.
• There is a learning curve.
• Make sure the operators are there to learn the equipment.
• No distractions–this should be their full-time job during start-up.
• Make sure maintenance is there to learn how to service the equipment.
• If products or supplies are needed to run in the machine during start-up, make sure they are immediately available
• Do not plan on shipping the test product to a customer.