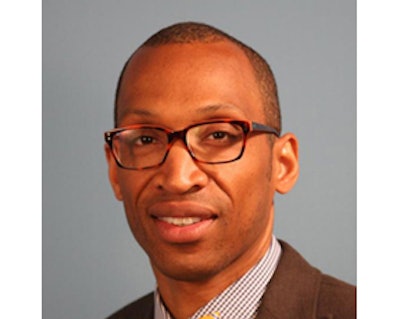
As new dosage forms and pharmaceutical drug products have evolved over recent decades, container closure systems used to make, store, transport, and administer finished products to patients have needed to keep pace with those changes.
Perhaps one of the most transformative trends in pharma in recent years has been the explosive growth in biologic drug development. While these medicines have opened doors for treating many different cancers, autoimmune disorders, and chronic diseases such as diabetes, biologics have presented some new challenges related to packaging systems.
Biologic drugs are not a new concept—legacy biologics such as heparin, insulin, and some vaccines have been available for therapeutic use for some time. However, more modern biologics—including monoclonal antibodies, protein therapies and cell- and tissue-based regenerative medicines—are prompting manufacturers to examine the impact of packaging material selection early in the product development process. By considering these factors early on, manufacturers can help to ensure the safety and effectiveness of their products in the final packaging system.
The use of living organisms in making biologics is a significant contributor to stability issues associated with these drugs, compared to the traditional pharmaceuticals based on small molecules made through chemistry routes. In addition, changes to manufacturing processes and conditions (e.g., transport to a different facility) can have an impact on biologic drug quality.
Leachables from container closure systems should also be considered when dealing with biologics. Since many biologics are very large proteins, their make-up can contain both hydrophilic and hydrophobic areas. Leachables can bind to these areas and potentially cause structural changes to a protein, potentially altering its function as a biological drug.
While it is important to know whether a container closure system has the potential to interact with a finished biologic product, it is also important for the manufacturer to determine if a packaging system is suitable for use. Thus, packagers must consider how container closure systems and the materials used in their construction can impact the quality of the biologic products they hold.
The U.S. Pharmacopeial Convention (USP) is currently developing and revising general chapters related to container closure systems in its compendia of standards—U.S. Pharmacopeia—National Formulary (USP–NF). Central to the revision and creation of these chapters is the assumption that if manufacturers begin with good materials of construction that are well-characterized, users will end up with good packaging systems that are suitable for use.
Previously outdated, USP’s General Chapter <661> Containers—Plastics has undergone a recent revision to incorporate information helpful to users in determining the suitability of packaging materials. The revised General Chapter <661> has been renamed Plastic Packaging Systems and Their Materials of Construction. It will provide the testing rationale for plastic materials of construction and packaging systems used for the pharmaceutical industry.
USP also is developing related subchapters: <661.1> Plastic Materials of Construction and <661.2> Plastic Packaging Systems for Pharmaceuticals. General Chapter <661.1> will help determine whether a material is deemed well-characterized by establishing its identity, biocompatibility (biological reactivity), general physicochemical properties, additives and extractable metals. General Chapter <661.2> will provide test methods and standards for plastic packaging systems. All three chapters were open for public comment from September 1, 2014 to November 30, 2014, and USP is currently reviewing the comments received.
Two additional subchapters are planned for the future: <661.3> Plastic Systems Used for Manufacturing Pharmaceutical Products and <661.4> Plastic Medical Devices Used to Deliver or Administer Pharmaceutical Products.