Improving maintenance and reliability effectiveness is a sure way to improve asset utilization. A recent post by David Clayton of ARC Advisory Group put it this way: “ARC believes end users can enjoy a step change in maintenance and reliability effectiveness by adopting recently developed advanced machine learning platforms. Integrating machine learning techniques and cognitive analytics provides end users advance warning of impending equipment failure, enabling companies adequate time to remediate the problem prior to failure to avoid costly unplanned downtime.
“Recent advances in data science, artificial intelligence, and computing power have converged to enable commercialization of algorithms to provide human-like analysis of large data sets (structured or unstructured) at machine speeds. Cognitive analytics refers to a set of innovations inspired by the way the human brain thinks. It strives to provide machines with the ability to process complex unstructured data sets by continuously learning and drawing conclusions from new data entering the system as well as from previous insight. Ultimately, cognitive analytics breaks away from traditional rules-based models to new models relying on hypothesis generation based on multiple data sets that codifies human instincts and experience into machine learning.”
Among the technology suppliers offering up solutions in the cognitive analytics space, said Clayton in his post, is SparkCognition. I talked with Usman K. Shuja, Vice President of Market Development at SparkCognition, about how his firm’s software might play a helpful role in packaging operations. He explained that it was essentially a matter of collecting sensor outputs—optical sensors, heat sensors, mechanical sensors, etc—and understanding them so as to correlate them with impending failures.
“At any given point, based on sensor outputs from machines, we can provide insight on the health of an asset, specifically when an asset is likely to fail and here are the reasons why,” says Shuja. “This helps an end user get ahead of the failure and either replace the asset or call in for preventive maintenance.”
Shuja distinguishes between “hard” and “soft” failures. “The hard failure is where something goes down completely,” he explains “But it’s also important to understand the soft failure, where you’re going from 100 cases per minute to 94 cases per minute.” When that happens, the data provided by line sensors can pinpoint where the problem is and what needs to be changed or repaired. SparkCognition’s software is what correlates sensor data so that this kind of pinpointing can take place, says Shuja.
“What usually happens is that the sensors on a packaging line are connected to a data acquisition system made by companies like National Instruments or Rockwell Automation,” says Shuja. “We then connect with their system to analyze the data.
“There’s value on the table to be picked up. If you use the right analytics and you have the right sensors in place, you can really push efficiencies to a high level.”
Cognitive analytics—‘there’s value on the table to be picked up’
Improving maintenance and reliability effectiveness is a sure way to improve asset utilization.
Jun 27, 2016
Machinery Basics
Smart Filling Equipment Selection Guide
Discover the six critical factors that determine filling equipment success and avoid costly selection mistakes that drain profits.
Read More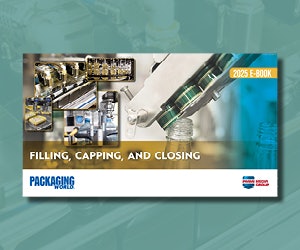
Researched List: Engineering Services Firms
Looking for engineering services? Our curated list features 100+ companies specializing in civil, process, structural, and electrical engineering. Many also offer construction, design, and architecture services. Download to access company names, markets served, key services, contact information, and more!
Download Now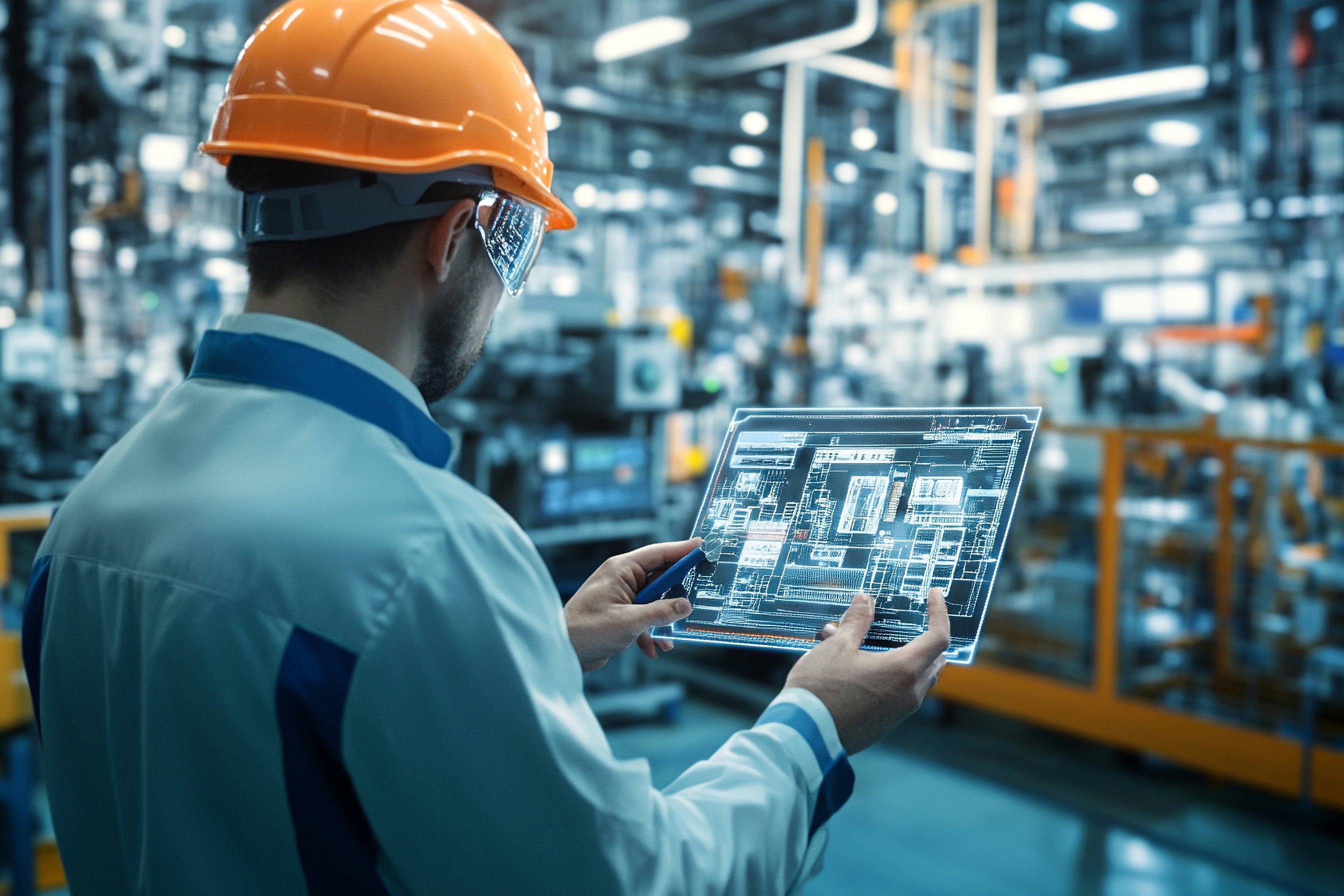