The manufacturing skills gap is going to grow worse before it gets better. This is my conclusion from discussions held with machine builders, packagers, and educators during a three day PMMI mechatronics workshop this past week. Representatives in each segment reported that they are seeing increasing demand for skilled workers. Adding to this conclusion is an article in the Wall St. Journal that appeared during the same time period, reporting on the rise in early 2016 in durable goods orders, industrial production, and capital investment.
Many factors remain barriers to attracting, training, and retaining capable people for these high-paying manufacturing jobs. Among those that were discussed during the week are the following.
1) Middle and high school students and their parents have little if any exposure to today's high technology manufacturing because manufacturers no longer offer plant tours, trade shows are off-limits, and career educators have no exposure from which they can offer credible counseling.
2) Skilled veterans do not have access to counseling to help them translate between the vocabularies and standards of manufacturing and the military. While underlying technologies are not that different, what looks like a capacitor on a drawing to a military technician looks like a relay to an industrial technician; and components and processes are called by different names.
3) Corporate and middle managers do not understand the value and importance of experience for manufacturing technology. After four years of college, It takes ten years for a creative engineer to become a truly skilled machine designer. After two years of college, it takes five to ten years for a maintenance technician to hit his or her stride.
4) Manufacturers have not come to understand the need for constant training to keep up with underlying technology changes. Today's industrial components bear little resemblance to those of five years ago. This is an especially critical area for maintenance technicians who may be working across half a dozen generations of equipment from one day to the next.
5) Educators are not inclined to establish programs to teach the skills needed for manufacturing because the costs and complexity of doing so are quite high relative to other programs of study.
6) Manufacturers and educators have not been able to reach an appropriate balance between one-size-fits-all and totally customized solutions.
Can we solve our workforce problem or not?
This just in from On the Edge Blogger and regular contributing editor Keith Campbell.
Mar 7, 2016
Machinery Basics
Annual Outlook Report: Sustainability
The road ahead for CPGs in 2025 and beyond—Packaging World editors review key findings from a survey of 88 brand owners, CPG, and FMCG readers.
Download Now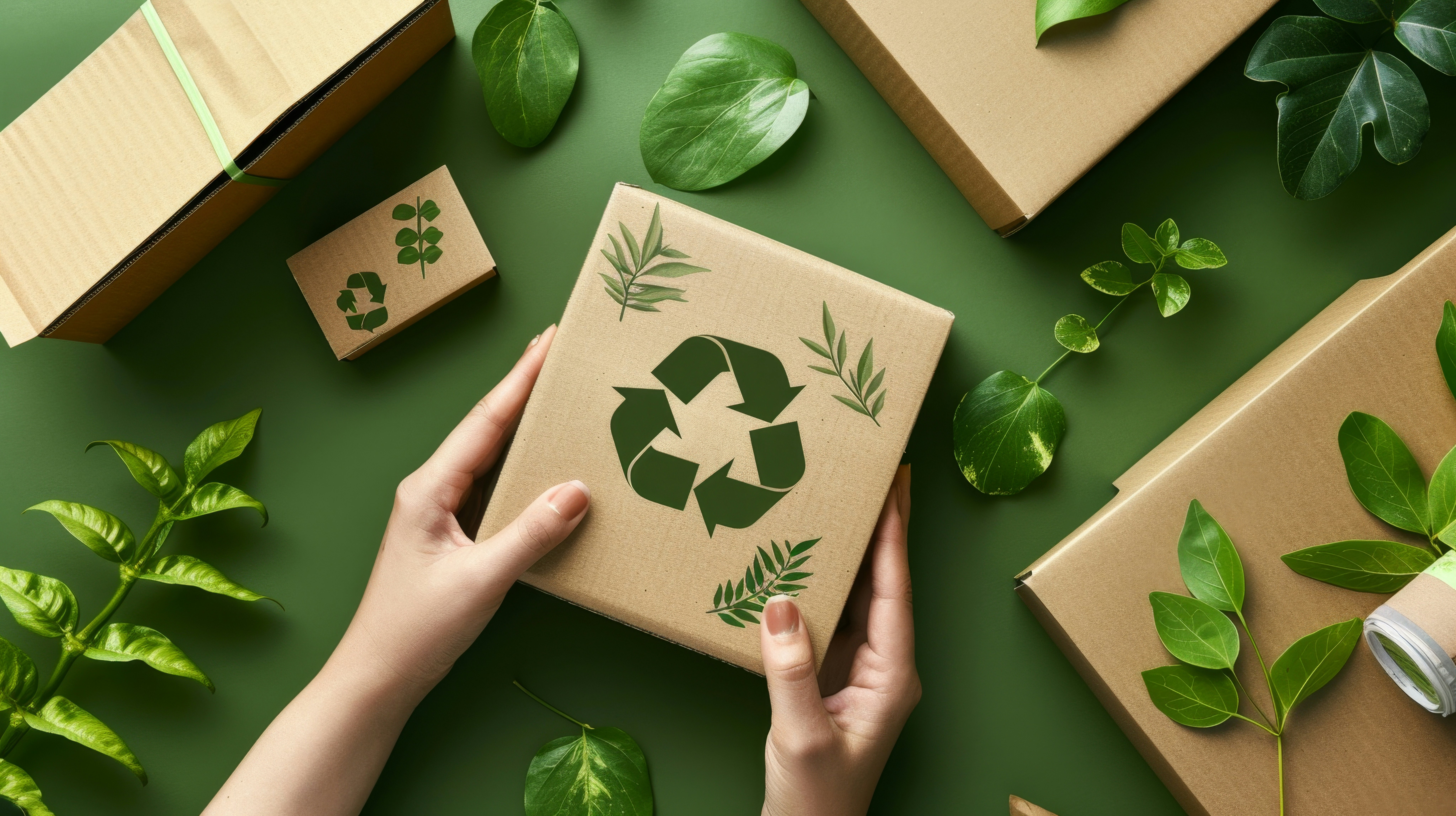
Coding, Marking, and Labeling Innovations Report
Explore our editor-curated report featuring cutting-edge coding, labeling, and RFID innovations from PACK EXPO 2024. Discover high-speed digital printing, sustainable label materials, automated labeling systems, and advanced traceability solutions that are transforming packaging operations across industries.
Access Report