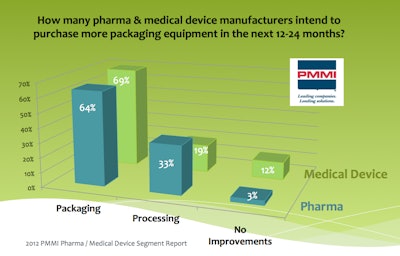
Demand for greater flexibility, cleanability and end-of-line robotics are three key areas driving advances in pharmaceutical and medical device manufacturing and packaging machinery, according to the 2012 Pharma / Medical Device Segment Report—the first since 2008 by the Packaging Machinery Manufacturers Institute (PMMI).
In addition to presenting findings on drug delivery trends, covered in a separate story, researcher and report author Donna Ritson, president of DDR Communications, Lindenhurst, IL, presented key findings on pharma and medical device equipment trends to attendees of the 2012 Pack Expo in Chicago.
Key take-aways
The PMMI research not only indicates manufacturer wants and needs, but provides compelling advice manufacturers should expect of their original equipment manufacturers (OEMs). Ritson presented four key action areas, with bulleted lists of items each category:
1. Build easier to use machines
- Flexible
- Quick and efficient changeovers
- Intuitive diagnostics and operator interface
- Cleanable
- Efficient
- Reliable
- Operator safety
2. Understand the complexities of validation
- Assist with equipment validation
- Supply documentation
- GMP - Good Manufacturing Practices
- Factory Acceptance Testing, & validation/qualification steps (installation, operation, performance)
3. Be a Partner
- Visit the manufacturing facility
- Understand the need for specialized equipment
- Amicable to the changes needed
4. Support aging equipment
- Recommend equipment improvements
- Smarter components and communications
- Parts availability
- Safety standards
These conclusions were drawn based on research findings in several areas, including those summarized below:
Equipment validation: "Validation remains a challenge," Ritson said, as it was in 2008. The top five validation challenges four years ago were product traceability, online diagnostic software; vision inspection systems; remote upgrades of control systems and the integration of validation and documentation. Today, the top five are product traceability; vision inspection systems; online diagnostics; validation documentation and validation standardization. Both share the common need for better validation and the associated documentation.
Mergers & acquisitions: M&A activity has resulted in excess equipment, but will this delay new equipment purchases? It depends who you ask. Among medical device makers, 72% of those surveyed said it yes, while drug-makers are evenly split on the matter; 45% said yes, 45% saying no in PMMI's survey.
Top reasons for purchasing: "New products are the No.1 reason driving pharmaceutical equipment purchases, while device-makers' top reason is replacing aging or obsolete equipment. Combining both groups, data show that purchases to support OEE or Overall Equipment Effectiveness programs remain high on the list, at 4th place this year, 3rd in 2008.
However, there has been a significant shift in purchase drivers in the past four years, as indicated by the survey's rankings. For example, the No. 3 purchasing driver today is to replace aging equipment—something that was 15th on the list in 2008, before the financial crisis. (See Figure, "Top Reasons for Purchasing New or Updating Equipment.")
Targeting robotics for new equipment purchases: Data show that 64% of pharma and 69% of device firms intend to purchase more packaging equipment in the next one to two years. For both pharma and device manufacturers, robotic equipment for end-of-line packaging "remains as important now as it did five years ago," said Ritson.
Spending more or less on equipment? In that same two-year window, the biggest trend is that 61% of pharma companies report that they'll spend more on equipment. This compares to the14% of device-makers who say they'll spend more and 43% who say they'll spend about the same.
Aging equipment: How doe companies manage the challenge of maintaining aging equipment? 50% of manufacturers surveyed said they look to their OEM, or original equipment manufacturer, for support. In light of this result, Ritson cited the need for OEMs to have "a good system for tracking their equipment to know where it is and who needs a retrofit." Other survey respondents said they prefer to replace the equipment (37%), handle updates in-house (9%) and only four percent turn to a third-party contractor.
Key machine improvements needed on the next generation of machinery: What drives improvements: "Flexibility of changeover" has remained the No. 1 driver for the PMMI's 2008, the survey, and Ritson, said. That metric was expressed in 2008 as "easy changeover for varied packaging." Fully 56% of pharma and 50% of device manufacturers noted that the number of SKUs they must produce is on the rise.
After flexibility, desired by 76% of all respondents, the 2012 results showed that easier cleanability is the next most important for pharma manufacturers. Priorities for both pharma and device makers that include, in order, followed with less maintenance and more diagnostic alerts (48%), faster speeds/throughput (22%), improved operator safety (18%), intuitive human-machine interface (11%) and less complex equipment (9%).
Modular equipment: PMMI results show that 72% of pharma and medical device companies "have a significant interest in modular equipment," Ritson said, noting that this improves flexibility and speeds startup times while lessening the equipment footprint in the plant. Of those 72%, nearly half already use machines with modular design, such as machinery in sections for easy configuration or flexible arrangement on the plant floor.
The need for real-time production data: Two out of three companies report the need for machinery capable of capturing and communicating real-time performance data, which is "becoming more important than ever," Ritson said. 40% are doing some form of data collection, while 29% said this need influences their choice of machinery.
Automation standards: Companies are looking to machine standards in order to minimize human contact in three ways: 1) Control systems to manage, command, direct, regulate or inspect the behavior of other devices; 2) Operator interface solutions for more effective operation, control and feedback and 3) safety systems to reduce risk protective measures at the I/O, network CPU (central processing unit) layers. The long-term key, per PMMI and Ritson: "Standards need to be global" when implementing such measures.
Global machine operations: Training remains the most critical factor for machine operators overall. But according to 49% of pharma manufacturers and 61% of device manufacturers, a five year trend continues: There is little interest in language and graphics on machines, however training remains the most critical component for machine operators," research shows.