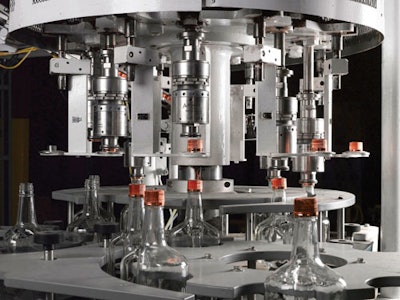
Efficiency boost. Capping headsets installed on rotary capping machines like the one above have boosted efficiency at Titos Han
Companies in this article
Damaged closures were unsightly. Overtightening made the closures a challenge in the hands of consumers. New headsets on rotary cappers solved both problems.