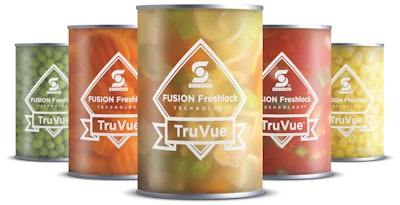
For rigid plastic packaging supplier Plastic Technologies, Inc., understanding the needs of its customer base means looking outside its areas of expertise to understand changing market trends as well as complementary packaging equipment and materials innovations. From February 8-10 in Henderson, NV, PTI and co-producer SBA-CCI, a polyester packaging consultancy, held The Packaging Conference to share these market drivers and new technologies with the event’s more than 220 attendees that included brand owners, material and equipment suppliers, and other industry professionals.
The 2016 edition of the event, taglined “where business opportunities and technology meet,” covered issues such as package design, recycling, e-commerce, and new material and equipment technologies, and provided analysis of various markets.
Since its launch in 2008, The Packaging Conference has earned the reputation of being a venue for breaking news. Among the suppliers presenting new products, Sonoco unveiled its TruVue retortable clear plastic can, and packaging equipment manufacturers Nissei ASB and 915 Labs LLC presented their recent technology platforms for retort PET and Microwave Assisted Thermal Sterilization (MATS), respectively.
Clear PET retort jar
Developed to address the demise of the center of the store, Sonoco’s TruVue™ plastic can with Fusion FreshLock Technology™ takes its cues from the fresh areas of the store and brings them back to the center. Said Steve Gendreau, Division Vice President, Sales & Marketing – Global Plastic for Sonoco, the clear retort can provides disruptive innovation with the potential to create renewed relevance to the canned food category. The market, he said, represents a ±30 billion-unit opportunity, encompassing applications such as fruit, vegetables, pet food, and soup, among others.
The TruVue can is made from a five-layer plastic substrate comprised of polypropylene and ethylene vinyl alcohol and incorporates an easy-open steel lid and bottom closure. The technology involves a crimp seam plus an induction-seal end application. Labeling options include pressure-sensitive film or paper labels, and full-body wraparound film labels. According to Sonoco, it is the first clear can to withstand the rigors of continuous retort systems without overpressure, performing in high-temperature and high-pressure environments.
“Consumers love it,” said Gendreau. “We found a 70-percent approval rating over metal cans. Perception is reality; consumers believe it’s going to taste better because the brand owner trusts them enough to show them the product.”
Double-blow PET retort technology
In another presentation, “First Installation of a Retort PET Line,” Jamie Pace, VP – General Manager, Nissei ASB, talked about the company’s double-blow technology for hot-fill wide mouth jars. The process, according to Nissei, addresses the challenges of developing a crystallized neck that remains free from deformation that could lead to leakage.
ASB double-blow technology involves three steps that include preform molding, neck crystallization, and stretch blow molding, accomplished through the use of preform molder, neck crystallizer, and a double-blow reheat machines, respectively. Among the advantages of the technology, the double-blow process allows a finished container to be filled and pasteurized at temperatures up to 205°F and provides the highest sidewall crystallinity (40 to 41%), 1.3-times the barrier improvement, and longer stability in storage. In addition, for a 350-mL jar, the weight is one-sixth that of a glass jar, resulting in significant transportation energy and CO2 reductions.
During his presentation, Pace presented a case study of what he believes is the largest PET retort container: a 1-gal jar for Öncü tomato and pepper pastes from Acemoglu in Turkey. The company is producing both the 1-gal and a 1.5-L container using four preform machines, two crystallizers, and six blow molders at speeds to 3,600 hr. The pastes in the retort jars have a 12-month shelf life.
MATS food processing technology
Calling it a disruptive and tipping-point technology, Kevin Peterson, VP of 915 Labs LLC, introduced the company’s Microwave Assisted Thermal Sterilization technology in his presentation, “MATS Technology: Revolutionizing Food Processing.” The process from 915 Labs, now in the commercialization stage, is said to vastly improve the quality, taste, nutritional value, and safety of packaged and prepared food.