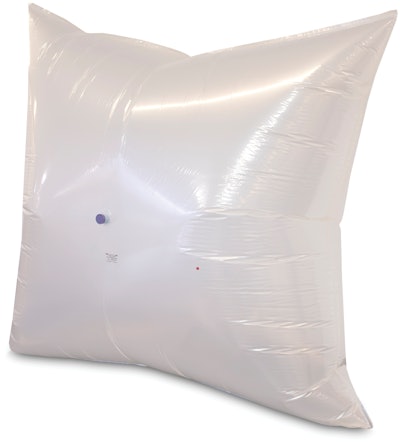
Designed for aqueous, low-viscosity food products that are sensitive to oxygen, this bag provides the clarity and durability required by the distribution chain through which it moves. It replaces multilayer laminations that, because they typically include a metallized substrate for barrier purposes, can’t offer the see-through feature that Shield Pack offers. Currently the Shield Pack is available in one size capable of holding 300+ pounds, but other sizes could be made. Amcor ships these bags to its food manufacturing customers folded flat in corrugated shippers. Customers filling them encase each one in an IBC plywood crate.
Amcor makes the bag from a triple-barrier material that is 10.8 mils thick and has an Oxygen Transmission Rate of less than 0.04 cc of O2/100 in2/24 hr at 73ºF, 80% RH, 1 atm. It consists of these four independent free-floating plies:
• a blown coextrusion of LLDPE/Nylon/EVOH/Nylon/LLDPE
• an identical coextrusion of LLDPE/Nylon/EVOH/Nylon/LLDPE
• a blown coextrusion of LLDPE/EVOH/LLDPE
• monolayer LLDPE
On an automated bag-making line, Amcor unwinds eight coextrusion blown film layers—four for the top of the bag and four for the bottom—into tooling that shapes the bag and heat seals the layers together around the entire perimeter. Also inserted on this system is the fitment used for filling and dispensing.