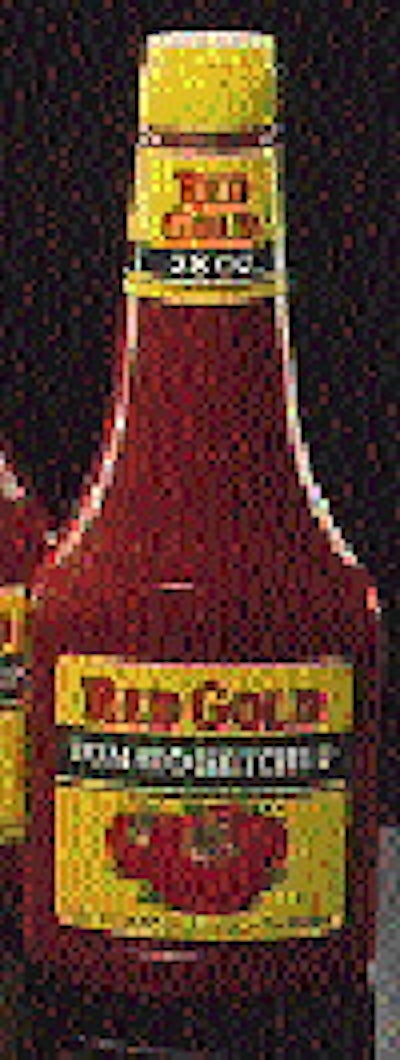
packaging market. But, as with so many statistics one encounters in this business, the numbers depend on what you include or don't include in your calculations. The way we see it, packaging machinery sales and the value of packaging services-design, engineering, contract packaging, distribution, etc.-have to be counted in the total. Most measurements of the packaging business consider only the value of material or container shipments. But, if there were no equipment or services sectors, food packaging would consist of scallop shells, gourds and pigs' bladders. To be sure, material and container sales alone account for more than 90% of the food packaging business. Packaging machinery makes up another 4 to 5% and the ancillary services make up the rest. No wonder packaging developers spend so much time concentrating on food. It's where the action is, where the big battles are fought. And, victories won in the battle to extend food product shelf life, streamline packaging lines, source-reduce containers, get food in the hands of consumers faster and fresher and simplify opening and reclosure, can be applied to a broad spectrum of packaged goods. Three recent gains in the packaging war to defend foods from environmental attack include: * "Managed barrier" flexible packaging of pre-cut, fresh produce. Fresh fruits and vegetables continue to "live" after they've been harvested-breathing in oxygen and exhaling carbon dioxide. To prolong the post-harvest life of fresh produce, flexible packaging converters such as Cryovac Div., W.R. Grace & Co. (Duncan, SC); Cypress Packaging (Rochester, NY); Deluxe Packages, Inc. (Yuba City, CA); and James River Co. (Milford, OH) are producing a variety of laminated and coextruded film structures designed to "put the produce to sleep" by slowing respiration rates. While traditional "high-barrier" films have oxygen transmission rates (OTRs) in the range of 0.3 to 1.0 cubic centimeter per 100 square inches per 24 hours, the OTRs of this relatively new crop of film structures run from 90 to 1ꯠ. Managed barrier produce films have to be tailored to specific commodities since apples and oranges (broccoli, tomatoes, carrots, etc.) "breathe" at different rates. Pouched salads and salad "kits" including dressings and toppings can now be found in supermarkets everywhere. Dole has been selling fresh cut pineapple in pouches for some time. Now, Met West Agribusiness (Del Rey, CA) is marketing fresh sliced apples nationally (see p. 2). Both Fuji and Granny Smith varieties are offered in zipper-closing polyethylene pouches featuring FreshHold® breathable membranes. FreshHold membranes, developed some years ago by Hercules Inc. (Wilmington, DE), are now being produced by Fresh Valley Technology (Salinas, CA). * Another choice in high barrier polyethylene terephthalate (PET) bottles. Ever since 1990 when H.J. Heinz switched its ketchup out of polypropylene/ethylene vinyl alcohol copolymer/polypropylene (PP/EVOH/PP) bottles into five-layer PET/EVOH/PET/EVOH/PET containers, there's been only one producer of clear, oxygen-barrier PET/EVOH bottles, Continental PET Technologies, Inc. (Florence, KY). No more. Shucking off its glass container and food can operations, American National Can (Chicago, IL) is now concentrating on plastics. For the last year or so ANC has been injection molding preforms and blowing 28-ounce PET/EVOH/PET Gamma bottles in its Batavia, IL, plant for Red Gold, Inc.'s branded and private label ketchups. Now, targeting oxygen-sensitive foods such as "natural juices, cream-based salad dressings, sauces and ketchup," the company is spending $11 million to expand its Bellevue, Ohio, blowmolding plant. Worth watching: ANC's decision to sell preforms so food packagers can blow their own PET/EVOH/PET bottles. Unlike in Europe and South America, that's something few food packagers do in this country. So few, in fact, that blowmolding equipment is generally included in plastic processing, not packaging, business tallies. But ANC hopes in-plant blowmolding advances and the economics of shipping pallets of small, densely packed preforms rather than big, airy bottles will accelerate its entry into the barrier PET bottle market. * Organoclay/polymer blends called "nanocomposites." Nanocor, Inc. (Arlington Heights, IL), a newly formed subsidiary of Amcol International Corp., is working on food-grade nanocomposites for food packaging. Nanocor's early developmental work suggests that nanocomposites dramatically enhance the properties of some plastics without significantly increasing costs. How dramatically? The company is reporting gas barrier improvement in the range of 800% for some nanocomposite films.