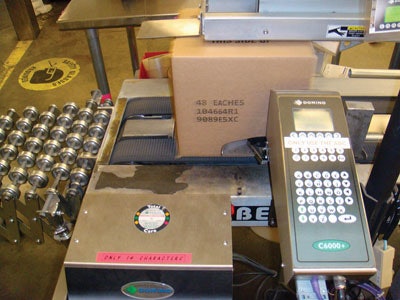
To keep up, it needed to upgrade the facility’s case-coding equipment used to package a variety of supplements, deemed necessary since the existing system was out of date and required continuous and costly maintenance, which increased downtime and reduced productivity.
The operation consisted of three printers on separate manufacturing lines. Each printer had several cables and 5-gallon ink drums. Spills were frequent, and the printers did not have the high-resolution capability necessary for bar coding. Additionally, the printer offered one console from which workers controlled three case-coding operations. Any problem was felt on all three packaging lines.
“As production demands continued to rise, the amount of maintenance required by our existing printers was a hindrance, costing us $14,000 each year,” comments Darryl Allen, the company’s lead mechanic. “We needed to replace the obsolete equipment with new models that were more user-friendly to reduce downtime. Also, we aimed to begin bar coding our products to improve tracking through the supply chain.”
To explore the latest advancements in case coding technology and automation, Allen and a team of eight colleagues traveled to Pack Expo Las Vegas in 2007. As the group shopped among the 1,200 exhibitors, they were able to compare and contrast solutions to find the one that would best meet Nutrilite’s needs. A few months later, Nutrilite purchased six C6000 Multi System case coders from Domino Amjet Inc.
The C6000 Multi System is designed for double-sided case coding. Each system is equipped with a single printhead that has multiple line capacity, providing Nutrilite the versatility to adjust the number of rows or change type sizes and fonts in a single format. The accompanying software allows employees to automatically adjust the formats from their own computers by selecting a preset template with no extra tooling to change. The system’s high-resolution printing capability helps Nutrilite implement bar coding as planned.
Using the old system, data entry time to set up and complete a test run was 20 minutes. With the new equipment, the process is complete in three minutes. The result was a new system that virtually eliminated downtime and a cost savings of $14,000 on maintenance costs per year. Another benefit: Domino sent a representative to the Nutrilite facility to help train staff on operating the new equipment. Employees photographed the session and created a step-by-step visual guide for the education of new employees.