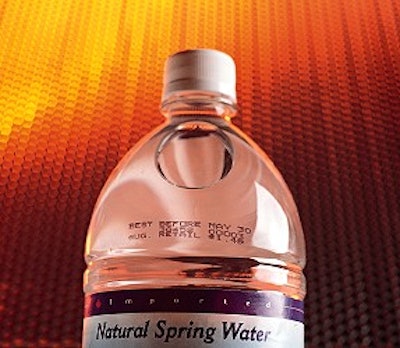
On the surface, it seems clear-cut. You’ve got a new product running on your line, so you calibrate and adjust all the equipment including your trusty continuous ink-jet (CIJ) printer for coding the packages. All that’s left is to get the line started, right?
Before you begin printing codes on the new packages, there are other factors to consider that may require a change in ink:
• Package substrate
• Environment in which you’re printing
• Ink drying time requirements
• Code durability requirements
• Industry standards, along with related regulatory or safety restrictions
Once you’ve evaluated this information, you’ll be able to determine which ink is best suited for the application.
What’s the substrate?
All inks are not created equal. There is no truly “one size fits all” ink to work in every CIJ printer and application. Before choosing an ink, you should first consider the substrate to be marked. Paper stock can typically handle most inks, but some plastics can provide a challenge to making inks adhere.
The condition of the substrate when it’s being marked can quickly narrow the list of appropriate inks. Many metals have a microscopically thin layer of lubricant that is present from other processes prior to printing. Depending on the thickness of the lubricant, marking and coding may be affected. For coatings like oil and water, inks have been developed that can penetrate such materials. But that’s not just a chemistry problem; it’s also a physics problem. The drops of ink aren’t being shot hard enough by the printer to penetrate the lubricant.
Where are you printing?
Another concern is the physical environment of the plant and the conditions at the time of printing, especially the air around the printhead. Not all inks adhere equally well in every condition; factors like moisture, temperature, humidity and dust can all have a negative effect. These conditions will rule out some inks, but there are others tailor-made to such situations. The key is to choose the right ink for the situation.
Additionally, technology is available that can help a printer work more optimally in plants that may have a significant amount of dust in the air. Keep in mind, too, that if conditions change, that could necessitate a change in ink.
How fast does it have to dry?
Drying times are also crucial. It’s not enough to say that it has to be fast; the speed needs to be quantified. The most important data to have is the amount of time between when the code is printed and when the code first touches something. It could be a person’s hand, another product or a roller, but that needs to be determined.
The typical time lapse is 2 to 5 seconds from printing of the code to the first touch, so inks must dry that quickly. That may sound fast, but there are some high-speed operations where the drying time is measured in tenths of a second. New ink could be required if your drying needs change.
How durable does it need to be?
A mark or code also has to be durable. It may have to survive chemical soakings, abrasions or environmental extremes like water and sunlight. The cradle-to-grave marking and coding trend continues to grow in many industries, which requires highly durable inks that can stand up to the toughest chemicals and abrasions in order to survive for the life of the product. These inks are usually used in conjunction with a specific type of printer for maximum effectiveness. Perhaps your goal is to create a chemical-resistant code that’s going to be subjected to solvents, oils and alcohols. In that situation, the best choice may be ink formulated to cure via heat or ultraviolet radiation.
If you’re exporting your products, there is a possibility you’ll have to mark or code them with ink that can be removed later, yet one that also adheres well and doesn’t rub off. The returnable bottle market is one example. When bottles are returned to the manufacturer or copacker, the mark or code is removed in order to reuse them. A caustic bath will do the job, but certain inks can be removed with water, a less intensive process.
What are your industry standards?
Also important to consider are standards specific to your industry, along with regulatory or safety restrictions concerning flammability or volatile organic compounds (VOCs), like solvents that evaporate into the air after printing. That means the chemistry that goes into developing an ink must be altered to remove or reduce chemicals that would violate these regulations.
When in doubt about meeting the requirements of regulations, standards or safety restrictions, employ the help of an experienced ink and printer manufacturer.
Have special needs?
Every industry has special needs that require special solutions. Perhaps you want to create a “covert code,” where you want to be able to track a product, but your copacker doesn’t want your code visible on the product because it’s going to apply its own code. The best choice is an invisible code created with fluorescent ink that is visible in a special lighting source, like ultraviolet light (UV or black light).
That’s just the beginning, however. Inks are available that change color when exposed to steam heat, which is especially common in the food industry for quality control measures. A canned product cooked via high-pressure steam can change the code from black to another color, like red, to indicate the product is completely cooked. Opaque inks are ideal for printing white and yellow codes on dark substrates. Some opaque inks require a unique printer because they are based on heavy pigments instead of dyes.
Food grade inks may be required on a package that comes in contact with food. Typically, such inks are used for marking and coding on the inside of a package. Some inks can even be kosher-certified.
Click here to read the entire article at Videojet's Web site.
Written by Dan Laird, technical support chemist, Videojet Technologies Inc.