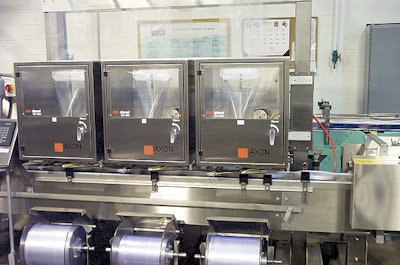
The other improvements at Peak Foods are upgrades to the tamper-evident shrink-banding operations. Peak’s single four-headed bander was replaced by two three-head tamper-band applicators from Axon Corp. Peak’s production flow is split equally to each three-head bander. One 7’-long heat tunnel was retained from the prior setup, and a new tunnel has been added.
Peak general manager Steve Vogel says that each unit can handle half of the production flow with as few as two heads, so the extra head on each provides production “headroom,” so to speak. The units automatically switch flow to the third head if one of the two heads acts up, according to Vogel. “This means that we don’t disrupt our production flow,” he says. “It’s worked beautifully.”
Vogel is especially appreciative of Axon’s new design. Previously, the bowls were transported on a tabletop conveyor between flights and a siderail. The band was dispensed over the bowl and rested atop the rail and the moving flights. The bands were “tacked” to the bowl with spot heaters before moving from the flighted section to the shrink tunnel. Vogel explains that it wasn’t uncommon for the band to become lopsided as the bowl conveyed inside the heat tunnel.