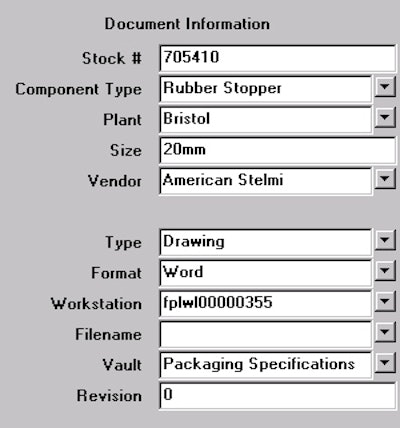
The revision or development of a packaging spec can be triggered from several sources. A plastic bottle vendor, for example, may want to source a different supplier of colorants used in its containers. Or the package engineering department may ask the vendor to switch resin suppliers. Production people at the plant may seek to reduce the size of an outgoing shipping case for a given product so that it handles better on the line. Change requests may originate from quality assurance or purchasing departments, as well. Changes that are minor-such as instructions to vendors on how to package or label the packaging components for delivery to SB's plants-are considered revisions. Structural changes, such as a new material or size, require the creation of a completely new spec, even though it's often based on an existing one. Here are the steps SmithKline Beecham goes through to create a new spec, for example, due to a request by the purchasing department to change resin suppliers for the company's 750-cc high-density polyethylene bottles. 1. A packaging spec coordinator in SB's Philadelphia headquarters pulls up the existing 750-cc bottle spec in NovaManage by typing in the SB stock number. When the software locates the spec, the coordinator double-clicks on it. This calls up the actual spec as a document in Microsoft Word. In plant users that access the system in the field don't even need that word processing program to view the document. Nor do they need AutoCAD, for example, to view CAD files. Instead, a small utility program called a viewer is included with NovaManage that allows users to open up and view (but not change) drawings or specs, regardless of the program in which they were originally created. 2. After the changes are made, the coordinator saves the spec (again, in MS Word) as a new document and "registers" the completed document with NovaManage. That alerts the system to kick off an approval/dissemination process, beginning by assigning the spec a unique item number, since a resin change is considered a structural change. 3. The coordinator chooses an appropriate, pre-configured "work flow." The work flow determines, among other things, which engineers in the package engineering department will review and approve it, and the order in which they do so. 4. The next time the packaging engineer who is designated the first approver logs onto NovaManage (a daily event at the minimum, for most users) he or she will see the spec there, awaiting approval. After reviewing the spec, the engineer approves or rejects the document using a unique "electronic signature" process. That process meets FDA requirements for substituting paper records with electronic records (see www.fda.gov/cder/esig/pt11finr.txt). Essentially, at the approval screen, the approver types in a special password, distinct from the first one used to log onto the system. 5. The document appears on the to-do list of the second approver when he or she logs into NovaManage. The second approver accepts or rejects in the same manner. If the document is rejected, it bounces back to the original author, appearing on that person's to-do list with an explanation of the rejection. 6. If the document is approved by the second approver, it is released into the system and made accessible to all users on the system. 7. Since this is considered a new spec, it is designated version number zero. If it were a revised spec, the previous version of the document is designated as a historical version. While the system is configured to show only the current version of any spec at first glance to minimize confusion, users can see previous versions if desired. 8. Once it's released into the system, the new or revised spec will show up on users' screens, along with any other specs that have been changed or added, when they run a "what's new" query. Since the software controls each step of the process, it is possible to track revisions. "You can see the history of a spec, what revisions took place, who approved them and why," says Gina Butler Galliera, a senior package engineer who works with Pack in SB's corporate headquarters. "It's nice to have a history that's electronic, that's not a paper file that you need to purge every five years. You always have this audit trail." Such an audit trail is the cornerstone of the system's ability to be validated. With a paper-based system, it's nearly impossible to guarantee that users receive the latest specs, which is why a paper-based system can't really be validated, according to Galliera.