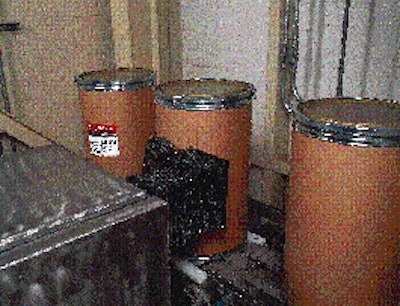
The company's previous printer/applicator started experiencing problems almost immediately. "Dust would get on the print media or printhead, so you'd have bad print or bad transfer," says Dennis Rascon, granular packaging team leader/maintenance coordinator. A year ago, NutraSweet had had enough. It brought in a new Diagraph (St. Louis, MO) Model PA/9060 wide-web labeler with a Zebra (Vernon Hills, IL) 170XI printer. (A second labeler was installed on another line in May.) The unit is tightly sealed inside a gasketed stainless steel cabinet that so far has stood up to the punishing environment. The labeler works with a variety of square and round industrial containers, ranging in size from 12" x 7" corrugated boxes to 30-gal fiber drums. Only a height changeover is required. It's capable of printing and applying NutraSweet's standard 6"x6" drum label, which is a wider label than most standard thermal-transfer label printers can produce. It can also print smaller labels, something NutraSweet's previous printer couldn't do. "It allows us to do more custom labeling for different customers," says Rascon. Print resolution is 300 dpi. All labels carry the specific gross and net weights and a sequential drum number. Unlike the previous labeler, the Diagraph unit is off-the-shelf, which NutraSweet preferred. "The previous applicator was custom-built, and it was very difficult to get parts and service for it." The new labeler is controlled by an existing PLC that controls the entire packaging line. When a product recipe is selected on the PLC, it downloads instructions to the filler. Each drum is individually weighed before and after filling. As the drum breaks a photo beam before the labeler, the PLC downloads the gross and net weight for that drum to the labeler. Once a label is printed, the rollstock unwinds, makes a bend on a bar and emerges through a slit in the cabinet onto a vacuum tamp pad. The pad pivots upward and extends out to meet the drum. The drums, which are produced at a rate of about 30/hr, do not stop for the labeling process. The Diagraph unit manages to hold the label in position, despite strong air currents from air curtains installed over each doorway. "With the other machine the air curtains would blow the label off the pad before it was applied," says Rascon. "Downtime has been greatly reduced with these machines so far, but the real test with us is the test of time," says Rascon. "so far we've been very happy."