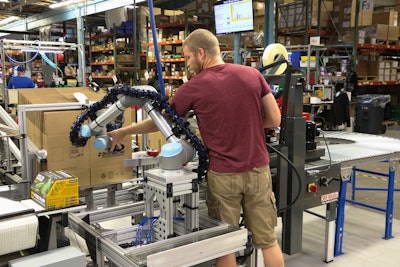
Tucked away in a rural valley in Ashland, OR, where labor is hard to come by, fourth-generation, family-owned company Darex needed to add more products to its lines without hiring more people. The company designs, engineers, and calibrates sharpening machines for drills, knives, and the like, all under one roof. Brands manufactured there include Darex industrial bit sharpeners, Drill Doctor professional and DIY drill bit sharpeners, Work Sharp Outdoor knife and tool sharpeners, and Work Sharp Culinary kitchen knife sharpeners.
Darex is repeatedly voted one of the top businesses in Southern Oregon to work for, despite the fact that for a long time, many of its jobs involved repetitive, ergonomically unfriendly, manual tasks. In 2017, Darex Director of Operations John Griffin sought automation to take his most valuable asset, his floor operators, off of those types of tasks.
“Basically, I needed to do more with the same amount of resources,” he says. Griffin considered automation and started looking into Universal Robots, specifically a series of cobots he had seen at several trade shows. “They appeared to be simple to program, and even vendors that weren’t selling robotics were using these robots in their booths,” he recalls. “So that kind of told me, ‘Wow, this really is the most popular one.’”
One of the reasons for cobots’ widespread use is their built-in safety mechanisms, which automatically stop the cobot arm when it encounters obstacles in its route. Once a risk assessment is performed, the cobots can then operate without safety caging. “We have a small production area, so I wanted to have something that wasn’t going to need a new dedicated space,” says Griffin. “It was great to be able to fit the cobots right into the middle of a production line, without taking up more space than a person would. Now I can have people work right next to the cobots without a bunch of caging.”
Ultimately, the company implemented Universal Robots cobots, first in its screw-driving operations, later in case-erecting and case-packing applications. The project quickly scaled from the initial install into a full-blown automation line with multiple workstations programmed via the Universal Robots PLC and HMI interface. The entire system was developed in-house, and the company continues with DIY solutions built on the Universal Robots platform. But looking back, Darex’s first foray into collaborative robotics two years ago was really just a weather balloon, a test to see what advantages could be realized.
Toe in the water for robotic automation
“Once we had a cobot in the facility, we quickly realized there was a ton of stuff we could do with it. We immediately put it into a position where it was screwing [sharpener] housings together. Traditionally we would have an operator with a pneumatic screw gun retrieving a screw from a screw presenter, sticking it into the machine, and driving it to torque—very monotonous, very ergonomically unfriendly work,” Griffin says. To alleviate the operators from this undesirable task, Darex chose the UR3 tabletop cobot, Universal Robots’ smallest cobot with a reach of 19.7 in. and a payload of 6.6 lb. The company was able to keep the exact same setup with the screw presenter and the screw gun; the only thing that differed was that the cobot was now doing the task. When the job was done manually, operators would sometimes miss screw insertions as the holes in the housings were hard to see into. “The UR3 hits all the screws all the time and if not, it will immediately notify us,” says Sam Jacobson, Production Engineering Supervisor at Darex. “We have definitely seen an increase in product quality due to the cobots.”
When Darex first received the UR3, Griffin was surprised by the out-of-box experience. “One of my engineers received the unit; he essentially took it out of the box and within an hour had it doing something just by goofing around with it,” he recalls. “It was intuitive enough that he was able to get it to do something really quickly. I was very impressed.”
The success of the screw-driving application quickly spurred Darex to look at its whole assembly line in a new light. “Since our first application went so smoothly, we decided to up the ante and add the conveyor system and all the PLCs controlling things like the pneumatic press and add another robot from Universal Robots on the case-packing side of it,” says Jacobson, who looked at several different solutions to control the entire system. “I actually decided to use the Universal Robot controller to program and handle the entire line, using Modbus communication to connect the different PLCs through the cobot’s teach pendant,” he explains. “I could program that entire thing so quickly, I was really happy with that decision.”
UR5 in place of case erectors
Before choosing Universal Robots’ UR5 mid-sized robot for a case-erecting application, the company considered using more traditional mechanical case erectors. “But they were limited in what they would do, and they only worked on a certain range of cases. We wanted more flexibility,” says Griffin, explaining that folding the cases into shape and adding products in them is a fast-paced task that employees did not like to do for extended periods of time. “While many of our products are shipped out as four packs, some of them are singles, and we do special packaging for certain customers. Amazon, for instance, asks for many of our sharpeners to be in a shippable container [Ships In Own Container (SIOC)] so they don't have to rebox it. We have a lot of different of case-packing configurations, and they’re only getting more numerous.”
The UR5 took over and is now handling the entire case-packing cycle, which starts with the cobot removing each die-cut corrugated shipper out of a cassette and folding it into shape. It places the folded box on a staging platform, pushes it into a squeeze chute that holds the shape of the box without the need for tape, grabs four individual cartons as they arrive on the conveyor, and loads them into the case. When the case is full, the cobot closes the lid and pushes the case through a 3M taping station for both bottom and top taping.
DIY mentality
Griffin stresses the importance of in-house configurability and flexibility for the cobots and corresponding PLC controllers. For instance, Darex added an area sensor made by SICK to the case-packing area. When an operator enters that area, the sensor slows the robot down. Most of the time, operators don’t need to be in the case-packing area, so Griffin has the robot running at full speed. But there are occasions when an operator could need to enter.
“We actually put that sensor in place so that anytime somebody walks into that immediate area, the robot slows down slightly and is more sensitive to external inputs,” Griffin says. Speaking of DIY, the end effector on the U5 case erector itself was also an in-house job. The 3D-printed end effector uses a pneumatic suction configuration from McMaster-Carr to open and fold corrugated cases and pack them.
“We have several 3D printers in house,” Griffin says. “We have a lot of fixturing that's 3D printed, and we can quickly prototype items with them, so they’re a pretty great feature to have on site.”
The next task Darex is looking to automate—again with an in-house solution, of course—is palletizing cases as they exit the tape-sealing station on the outbound conveyor. “Many of our products, cartons, and cases, though not identical, are very similar in size and shape, so it seems like that would be a good next application,” Griffin says. “It would also keep our employees from having to reach and bend over all the time. Looking at the assembly line we’ve already created, we could also easily take that and replicate it two or three more times in our production area and accomplish the same thing with other products.
“We would probably buy another cobot from Universal Robots for that since we have had great luck with that particular brand, and we already have several people who do the integration and programming for UR robots, so we have some institutional knowledge there.”
End of line and what’s next
As the cases arrive into the case-packing station, they are conveyed via a conveyor to a checkweigher, where they are weighed to ensure there are no missing or extraneous items within the carton. If under- or over-weights occur, a signal from the check station is sent to the UR5 to set the carton aside. “Instead of just alarming out and stopping the entire line, we get rid of the case and go right back to what we were doing. It’s a really neat feature that we programmed into it,” Griffin says.
After the packed, taped cases leave the tape sealer, shipping labels are affixed by hand. Each day the company may change configurations five or six times, and Amazon-bound SIOC shippers present another wrinkle (see Dealing with Amazon below).
“We obviously have a different label for each configuration. Currently, that is done manually, but as part of our next iteration, we are adding that automatic labeling capacity to our automated line,” Griffin says. “This will be in-line right after the tape sealer. The product will flow through that, become automatically labeled, and then will be ready for palletizing.”
Currently, palletizing involves 288 units hand-configured per pallet. They're palletized in production, then wheeled back to shipping. Once Darex receives the purchase order from Amazon, it then can construct the label or reconstruct the pallet.
“That's the function that we're going to automate,” Griffin says. “But first, we are taking our two manual lines and reconfiguring those with a conveyor system, which feels like the first step in getting the movement of product automated. Then we’re looking at automated stretch wrappers and more. Then our plan is to have all products basically flow into a case-packing station, so everything flows down three assembly lines, gets conveyed to a case-packing station—where it’s likely that we'll have two UR5s case-packing the products—and then palletizing gets done by one or two [heavier-payload] UR10s.”
Dealing with Amazon
“Amazon orders come in on any given day, and two days later, we have to ship out the product. For us, that sometimes means 10,000 or 20,000 packages, and each one of those gets a special label,” Griffin says. “We don't have the capacity to build those all at once. So we prebuild things. Once we get the Amazon order, we create the label, hand-apply those labels to each box in that two-day time frame and prepare those for shipping. We are looking at creating a station that would robotically unload a pallet, add a label, and re-palletize. That functionality should be one of our next projects, as far as automation goes.”
The company ships to Amazon in two styles: The first is a SIOC corrugated container that the product is directly placed into. There is no other carton, nor any ornamentation.
“We also ship to Amazon a product in a printed container that you could display at retail. Then that is put into another corrugated case. So Amazon is ordering both ways,” Griffin says. “They are increasing the SIOC versus the retail version. So it is slowly becoming more and more SIOC, but it's not completely one way or the other yet.”
Both styles go through the automated packaging line and use the UR3 robot for the screw-driving application. However, the single SIOC-style shippers naturally skip the robotic case-packing station near the end of the line.
ROI in less than a year, 30% efficiency increase
Not having to spend resources on expensive and cumbersome safety guarding also helped make the collaborative robots attractive price-wise. “For the ROI on purchasing the cobots, I initially predicted it would take about 16 months,” says Griffin, who was happy to see the UR cobots pay for themselves in less than a year. “I’m very pleased with what we did. There are several benefits of us having added automation to our production line. We’re running about 30-percent more efficiently on that particular production line. I have more flexibility, as it takes fewer staff to run that line, so I can focus people into different areas and run different products.” Instead of only building that product twice a week, Darex can now build it four times per week.
The contest to become Darex’s new robot technician
When Darex initially bought the cobots, the production supervisor was trying to think of ways to get the production team excited about having a robot amongst them. He also needed a dedicated staff member on the line to be the robot technician who could oversee all robot operations. “So I came up with this little competition,” says Griffin. “I gave everybody the UR Academy web address, told them to study up on this and invited them to compete for the job, using the knowledge from the Academy.” The UR Academy consists of nine interactive, online modules that cover the basic UR cobot programming and setup. Three weeks later, Darex held several rounds of contests where employees were required to program the cobots to perform simple pick-and-place tasks. The winner was 26-year-old Brittany Mohrman who had enthusiastically joined the contest. “It was really exciting to get the opportunity to do something different, so I jumped right in, learned all I could, aiming to beat out the competition,” she says, admitting she was initially a bit intimidated by the cobot. “But it was so interesting to see what you can make it do, and how you can change it in so many different ways. The UR training taught me things like understanding different program cycles, adjusting waypoint changes, and knowing where the tool center point of gravity on the robot is. My job is definitely more interesting now.”
How UR came to control the assembly line
Sam Jacobson, Production Engineering Supervisor at Darex, had several different options when considering how to control the assembly line with the conveyor and all the different substations. “I considered ladder logic and different programming options using external computers, but then I started investigating and learning about Modbus,” he says. “When I learned that UR had that functionality, I quickly decided to make UR the main controller.” This approach allowed Jacobson to set up a PLC at each station on the assembly line and, through a switch on the PLC, control all the inputs and outputs directly through the UR cobot’s teach pendant using the Modbus communication protocol. “All I have to do on the UR teach pendant is hit a button, and I can turn off or on any output and look at any of the inputs on any of my sensors in real time all across the entire conveyor line,” he explains.
Jacobsen read up on the Modbus setup using free materials and example programs on UR’s support website, but went into this project with no prior robotic programming exposure. “It was a lot of fun, really. The way the block diagram and everything is set up, showing a flow, makes it super easy and intuitive to do,” he says, emphasizing the step-by-step approach. “You can do something really simple and set up a bunch of waypoints, but as you delve more into the programming, you can figure out ways to do it more efficiently by using for-loops and if statements. But you don’t have to do that stuff right away. I started simple and then gradually added more complicated stuff such as threads where you’re doing simultaneous programs. That makes it really powerful.”