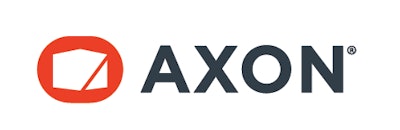
Show Daily Exclusive -
Heat-shrink tunnels from Axon, a ProMach product brand (Booth C-3021) and part of the ProMach Decorative Labeling business line, can process labels, sleeves or bands that conform to container shapes, offering benefits ranging from tamper evidence to 360-degree coverage, from brilliant graphics to efficient product flow.
Automating what could prove a time-consuming process of hand-shrinking bands via use of hot-air guns, these devices offer tremendous labor savings and consistent product appearance.
But not all heat tunnels are the same. Various types offer differing benefits, and realizing the strengths of each type—convective heat, radiant heat and steam heat—enables needs to be matched to the right machine.
Factors to consider include:
• Film type used
• Container material
• Product inside the container
• Environmental concerns
• Product temperature at the time of sleeve application.
WEIGHING THE OPTIONS
Understanding the specifics of each type of heatshrink tunnel can help make the correct decision about what partners best with a given application.
Convective tunnels utilize forced hot air to provide the heat energy required to complete the shrink process. e tunnel usually includes a fan to force air through a heat source, resulting in a heated air stream. Many tunnels feature a recirculation system to pull the heated air back into the process and boost efficiency. In some cases, industrial hot-air guns are used as the heat source and fan.
Infrared tunnels utilize radiant heat to provide the energy required to complete the shrink process. These tunnels utilize various energy sources from quartz panels, tubes and, in some cases, standard calrod-style heating elements with reflectors.
Steam tunnels use live steam to provide energy to complete the shrink process. Most steam tunnels require a separate steam source to provide the steam. For most tamper-evident (TE) band applications, the film used is clear, solid color or both, sometimes with a random print. For these applications, convective or infrared tunnels are normally used, with convective being the most common. As a general rule, aesthetics are less of a concern for TE applications than for sleeve-band applications.
Convective tunnels are suitable for most TE band applications. Infrared tunnels normally are used for higher-speed applications or when thicker, solid-color extruded lm is used. Infrared units typically transfer more heat energy than standard convective tunnels, which can provide a better shrink finish on thicker films. Steam tunnels are rarely used for TE band applications. Some exceptions are when the TE band also serves as a label and when the shrink application occurs in a hazardous environment.
Steam tunnels provide the best results for most sleeve label applications. The benet of steam is that the shrink process occurs at a low temperature, the temperature is consistent, and the heat energy transfer of steam is very high. Steam is recommended for most applications in which a sleeve is applied to a liquid-filled container, especially glass.
Convective tunnels are the most popular due to their ease of use. They also don’t require anything out of the ordinary to operate, unlike steam tunnels which need a steam source. The customer simply supplies the appropriate utilities and, in some cases, a conveyor. When using convective tunnels for labels, a multi-zone tunnel is recommended as it permits different temperatures to be used at different process stages. For most applications, it’s best to start the shrink process at a lower temperature and finish at a higher temperature. The goal is to start the onset of the shrink process slowly to minimize distortion.
Infrared tunnels normally are used in conjunction with other types of tunnels as a finishing unit. Infrared is similar to steam in that it provides a consistent temperature and a high heat energy transfer.
TRUE OR FALSE
The distinctions among machine types are vital to note since certain myths do pervade the industry.
One of the more prevalent myths is that heat tunnels used for standard shrink packaging or bundling are capable of processing TE bands and sleeves. People assume this is true due to a lack of understanding about the different types of packaging methods. A standard tunnel is not as effective because the air-flow requirements differ for each application. Various films also differ in shrink characteristics. The shrink-sleeve tunnel utilizes more of a cyclonic airflow with higher velocity.
Some factors are typically not considered that should be, such as utilities required to operate a heat-shrink tunnel, as well as anticipating
additional products that could be processed through the tunnel in the future.
In addition, environmental concerns will dictate the tunnel’s location. For example, a steam tunnel will increase the humidity in the area around the tunnel and can release excess steam into the room. The end user must take this into consideration.
GETTING SET UP
Superior heat-shrink tunnel suppliers will incorporate several key steps when working with a customer. First, the vendor should fully understand precisely what the customer seeks to accomplish with the machine. Based on this, the supplier should either request samples or pictures of the containers to be processed through the tunnels. Other details, such as speeds required and container dimensions, also need to be considered.
Once a machine is chosen, the vendor should request sample containers and film for tunnel setup and testing. Based on the testing results, the vendor should provide tunnel set-up sheets indicating the parameters used to achieve the best results.
Post-purchase perks should include phone/email support as well as onsite technical service. In addition, operational safety training is recommended for employees assigned to operate tunnels.
One prominent example of a company reaping the benefits of this technology is a co-packer specializing in personal-care multipacking.
The company previously used hot-air tunnels and had been saddled with a high level of rejects. By installing a steam-shrink system, the co-packer realized a substantial reject reduction and provided a higher quality level to its large corporate customer.
The result: a boost in business.
The cutting edge in the heat-shrink tunnel arena is steam evacuation/condensate recovery systems for steam tunnels. The ultimate goal, however, will be achieving the results and cost-effectiveness of steam by using convective or infrared tunnels or combinations of the two.
But for the present, with several tunnel types to choose from, a little foresight can result in a machine that meets needs now and into the future.
For more info, www.axoncorp.com. SD
Editor’s Note: is article was written by Ed Farley, product line manager, Axon