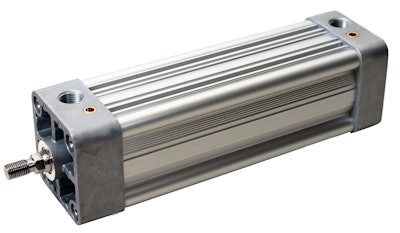
This content was written and submitted by the supplier. It has only been modified to comply with this publication’s space and style.
With its aluminum body construction and a steel piston rod, Emerson’s pneumatic cylinder features state-of-the-art pneumatic cushioning technology that allows an ideal cushion adjustment to slow down the piston to a stop by the time it reaches the endcap. Ideal cushioning reduces the time it takes the cylinder to complete a stroke, allowing an improvement in efficiency that significantly boosts machine speed and lowers endcap hammer. Ideal cushioning also reduces cycle time and enables the TM5 cylinders to carry higher loads without sacrificing cylinder performance.
The NPFA-compliant cylinder incurs less stress and there is no end-of-stroke bounce or end-cap slamming, which is a main source of cylinder wear, slowness and noise. Ideal cushioning thus lengthens cylinder operating life and reduces downtime related to cylinder failure. Additionally, it reduces machine noise and vibration while reducing energy consumption.
“The all-new TM5 TaskMaster gives machine builders and end-user manufacturers the tools to make their machines faster and more reliable,” said James Ward, vice president engineering, machine automation, Americas, at Emerson. “It´s the highest performing and most reliable TaskMaster cylinder ever produced, so it gives them an opportunity to build a competitive advantage.”