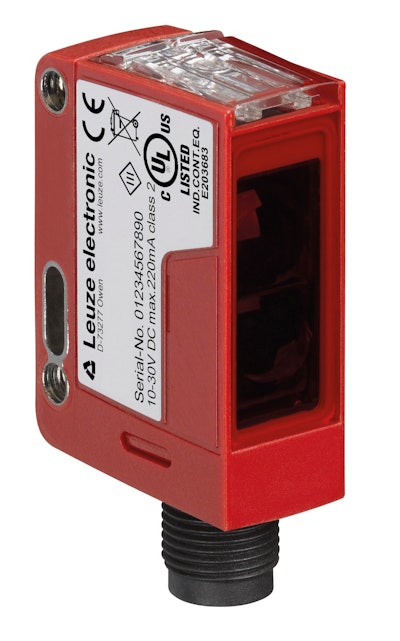
This content was written and submitted by the supplier. It has only been modified to comply with this publication’s space and style.
Sensors must continuously and reliably detect a wide range of products and films on the conveyor belts of primary and secondary packaging machines for confectionery and baked goods (hf/f/s, f/s, thermoform, or vf/f/s). The packaging machines keep running without interruption, even if the product or packaging material changes.
Leuze developed the DRT 25C dynamic reference diffuse sensor with its innovative detection method for precisely this area of application. The sensor works with three light spots and uses reference technology. The latter references the conveyor belt instead of the product and that is what makes this technology so unique. In the first step, the surface characteristics of the belt are taught in. This enables the sensor to subsequently detect all objects that do not correspond to the belt surface as "deviations", even if the conveyor belt is dirty or vibrating. With this approach, the surface properties of the products, such as the color, gloss, or transparency do not influence the detection. The DRT 25C uses its three light spots to reliably detect the entire spectrum: small, flat, or also tall and spherical products. Even irregular shapes and contours or products with openings, e.g. cookie curls, are detected. Thanks to the wide scanning range, these are also detected as a continuous piece.
The reliable detection of objects – even those with challenging shapes and surfaces – guarantees a high machine throughput and prevents system standstills. Even under difficult conditions such as vibrations or contamination on the conveyor belt. No realignment of the sensor is needed when products or packaging materials are changed over. This significantly reduces the setup time required and enables higher product volumes. The DRT 25C is quickly and easily set up due to automatic teaching by means of the teach button. With a universal mounting position for all objects. Additional functions can be conveniently integrated into the machine control via IO-Link. For example a warning message for excessive debris, use of the counter built into the sensor, or locking the teach button.