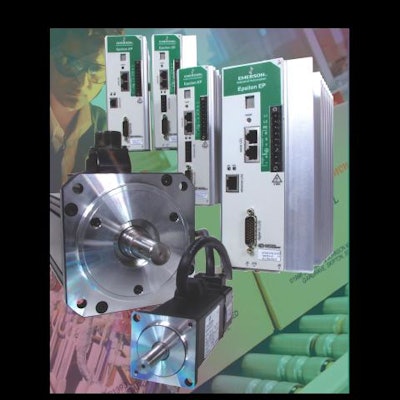
Drives now offer Position Tracker™, which can replace a PLC-based
position control module with a simple analog signal or fieldbus
register. Typically, a servo drive controls a motor’s velocity or
torque based upon an analog command input. An external position
controller is needed to calculate the position error and adjust the
analog command to cause the motor to adjust its actual position. With
the Position Tracker™ mode, the closed loop feature of the position
controller has been brought into Epsilon EP. The user simply needs to
feed the drive an analog or fieldbus signal that is proportional to
absolute motor position. No complex ladder logic to send acceleration,
velocity and position information, users must predefine the maximum
values of acceleration and velocity in PowerTools Pro software, then
send the position information via analog input or over the network
(Modbus RTU, Modbus TCP/IP, EtherNet/IP, Profibus DP or DeviceNet), and
the drive will command the motor to that exact position.
Companies in this product