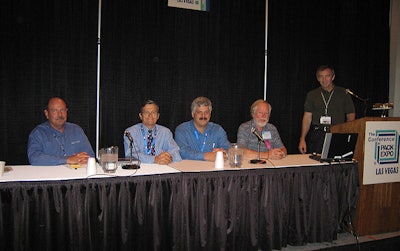
Maxed out on productivity? Try Make2Pack.
At PACK EXPO Las Vegas four participants in the Make2Pack joint working group asserted the proposed standard’s benefits to packagers and packaging machine builders.
The packager’s perspective
Procter & Gamble Technology Leader Dave Chappell the Make2Pack chair used the analogy of an iceberg to describe the impact of manufacturing and packaging operations colliding with an otherwise well integrated supply chain.
Make2Pack is a double entendre meaning both to better integrate ‘making’ with ‘packing’ and to more efficiently ‘make-to-pack’ rather than ‘make-to-stock.’ The latter refers not only to reduced inventory carrying costs but faster time to market with new products and package formats and a host of other enterprise efficiencies.
Chappell described his company’s imperative to bring millions of dollars to the bottom line by making the supply chain more effective and reducing life cycle costs of plant assets.
The implementation will deliver better vertical integration of information between the plant floor manufacturing systems and the Enterprise Resource Planning (ERP) business systems better horizontal integration between equipment as well as automation software that is modular consistent reusable and maintainable.
He also cited Pfizer’s additional reason for representing the ISA SP88 committee in the Make2Pack process. For the pharmaceutical industry time to market is not only critical to revenue and profitability regulatory compliance is a moving target. Industry standards will help producers and equipment suppliers in regulated industries meet current requirements and adapt to as yet undetermined future regulations.
Chappell knows of what he speaks -- he was instrumental in development of the original ISA 88 standard of which Make2Pack is destined to become Part 5. ISA 88 is now an accepted underlying architecture of batch process control systems deployed worldwide.
While Procter & Gamble and Pfizer have assumed the leadership roles they are not alone. The membership list of over 150 individuals includes representatives from Coors DuPont Eli Lilly Genentech Georgia-Pacific Hershey Kraft Masterfoods Nestle Schering Plough and Unilever as well.
The packaging machine builder’s experience
Joe Faust Electrical Engineering Manager for Douglas Machine shared his company’s experience with the underlying software architecture the initial cost to build a foundation of modular software and the resulting benefits.
That experience was eye opening revealing the competitive advantage to Douglas as an early adopter. The methodology is simple. Machine builders can reduce engineering costs and increase consistent quality through the use of libraries of tested reusable software modules that ‘plug’ into a state model as prescribed jointly by the OMAC Packaging and Make2Pack groups.
Combined program development program testing and machine testing with modular software takes 28 to 34 days compared to 50 to 65 days for a conventionally programmed or ‘monolithic’ program.
Programming time is reduced at least by 50% (from 20 to 25 days down to 10) and program testing is reduced by approximately 80% (from 15 to 20 days down to just 3 to 4). The savings potential is clearly derived from better software engineering as the machine testing component remains unaffected at 15-20 days.
Faust cited shorter development time standardized program structure the ability to increase machine features ease of machine upgrades expanding the breadth of machine offerings and protection of intellectual property as benefits to machine builders as well as users.
Faust duly noted the upfront costs as well. First the modular foundation must be developed and for the first modular machine that took 100 days of software development and 30 days of software testing in addition to normal machine testing.
For Faust’s competitors the first barrier to entry is the unwillingness to break with the past of monolithic programming and invest in the future. The second is to shift the paradigm to a team-based mechatronic-thinking design approach that treats mechanical as well as electrical engineering in a modular fashion.
What’s next
In the presentation MARKEM’s Fred Putnam updated the status of the OMAC PackML state model being further developed by the Make2Pack grou back to the ISA 88 standard and recapped OMAC Packaging Workgroup’s contributions.
ELAU’s John Kowal cited ARC Advisory Group’s recent analyses of Make2Pack and the software modularity in packaging machinery a project now in progress featuring Make2Pack principles on an Italian machine specified by a US pharma company at a plant in Ireland a 40% reduction in validation tasks on previous projects and a trend toward robotic functions being embedded in packaging machines using modular software.
Meanwhile the Make2Pack standards developers are working at a brisk pace meeting in person for 3 days each month with monthly teleconferences to inform and seek input from interested parties. The Make2Pack working group will publish a report in the first quarter of 2006 that will be submitted to the ISA’s SP88 committee for review and projected approval by early 2007. At that time the ANSI/ISA standard will be submitted to Europe’s IEC (International Electrotechnical Commission) to become an IEC standard.
For more information visit www.wbf.org/displaycommon.cfm?an=1&subarticlenbr=59