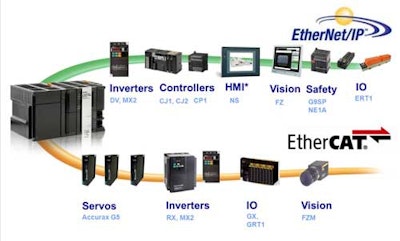
This content was written and submitted by the supplier. It has only been modified to comply with this publication’s space and style.
Machine builders, manufacturers, and systems integrators continue to migrate their industrial automation to Ethernet-based, networked I/O from hardwired discrete and analog signal installations, according to a recent independent survey.¹ Over the past decade, they recognized and took advantage of the cost and labor reductions, as well as improved up-time from faster troubleshooting that Ethernet-based systems provide.
Across all groups involved in the building and implementation of next-generation machines, the importance of high-speed networking and the availability of compliant hardware is a given. Even long-time users of fieldbus networks such as DeviceNet, Profibus, AS-i and Modbus are beginning to shift to Ethernet-based networks. The reasons why are compelling: reduced labor costs, standardization of one network media type for the entire machine, fewer wiring mistakes, smaller main machine panels, and higher throughput
According to Jay Hughes, senior application engineer at Omron Industrial Automation, the transition to networked remote I/O began about three or four years ago and is moving rapidly from traditional fieldbus networks to several Ethernet-based networks such as EtherNet/IP, EtherCAT, and PROFINET.
“People have traditionally built with DeviceNet, and a base of users and developers have continued to do so. However, EtherNet/IP has gained momentum and is replacing some DeviceNet for I/O communications in new applications,” notes Hughes.
The advantages of moving from traditional fieldbus networks to an Ethernet-based topology are considerable:
• Reduced cabling costs
Ethernet cable is much less expensive than most other cable choices.
• Fewer wiring mistakes
Pre-terminated Ethernet cables are easier to work with—and less prone to
wiring mistakes or improper network power design, reducing
inefficiencies that result in delayed machine delivery.
• Standardization of infrastructure
Both EtherNet/IP I/O and PROFINET I/O are designed to coexist with other
protocols on an Ethernet infrastructure, so machine builders only need
to run one Ethernet network to support remote I/O, HMIs, Safety, Motion
and SCADA software.
“From my experience, 80 to 85 percent of machine builders are using some sort of distributed, networked I/O solution,” says Hughes. “A host of networks are available, and networked I/O solutions are reducing costs. Reducing labor costs remains paramount to an OEM, so they are finding it a lot less expensive to buy a networked product upfront than spend time wiring a non-networked solution afterwards.”
Other factors include material and physical costs. The cost of copper has increased by almost 70 percent in the last two years, making it more expensive to buy wire. The high cost of wire is driving people to remote networked I/O solutions, enabling them to consolidate numerous I/O wires into a single network cable. Furthermore, the ability to use smaller control panels is significant. Larger panels cost more, and all customers are expecting machines to have a smaller footprint with increased functionality to reduce panel size. Reducing the size of control cabinets is less expensive and uses less of a customer’s floor space as well. Many manufacturing facilities are trying to increase equipment density—get more machines into a given space.