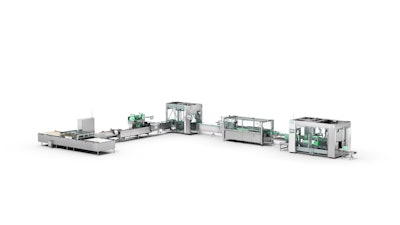
This content was written and submitted by the supplier. It has only been modified to comply with this publication’s space and style.
The DCG’s discharge belt lowered and deposited the cakes gently and in a controlled manner onto the downstream cross belt. Due to its gentle handling, the distribution station is ideally suited for delicate baked goods or sticky bar products.
Once the sliced cakes were discharged onto the packaging leg, the FIT inline module continuously fed them to the flow wrapping machine while preventing products from accumulating along the way. Linear motors ensure gentle handling of the sensitive products. Each mover can be controlled and only accelerates when the product has been safely captured. This means that the individual sliced cakes do not come into contact with each other, which in turn reduces mechanical stress. In addition to gentle handling, the FIT impresses with its high flexibility: Operators can switch between different formats at the push of a button via the HMI.
The sliced cakes were then packed by the Pack 403 flow wrapping machine. Due to fast and tool-free format changes, it is suitable for a wide range of products. At interpack, the Pack 403 packed up to 400 cakes/min in gusseted flow wraps. The recyclable mono material film was heat-sealed.
The subsequent robotic pick-and-place platform RPP ensures a high degree of flexibility. The modular plattform has been tried-and-tested in different systems since 2022 and will now be shown as part of the exhibited line with a new grouping and loading function. The primary packaged cakes are inspected and then continuously placed into the robot's collation chain. Defective packs are discharged instantly. A robot arm picks the individually packaged sliced cakes at 50 cycles/min. The products are seperated at the gripper into groups of two by four. The robot deposits the grouped products in the integrated bucket chain of the endload cartoner. The speed of the robot and the cartoner's infeed chain are fully synchonized. With the showcased application, manufacturers benefit from the flexibility and scalability of Syntegon's robotics platform. In addition to fast and seamless system integration, all RPP versions also meet IP65 protection class and high hygiene standards. This means that it can even cater to applications with demanding cleaning requirements.
As part of the line, Syntegon also presented the latest version of the compact Kliklok BEC endload cartoner. The RPP and BEC were integrated into one unit with the machines connected via Ethernet for easy operation. The endload cartoner packs the pre-grouped sliced cakes and sideloads them at a speed of 100 cartons/min.. Show visitors experiencedthe machine's new technical features: In addition to a new Human Machine Interface (HMI) 4.0 for connection to the digital service portfolio, it also features improved controls. Control technology from Beckhoff in discreet CPU boxes enables cabling without control cabinets – resulting in a compact layout as well as easy system integration. Moreover, Syntegon showcased the BEC with an optimized drive system: With the switch to servo technology, various drive components can be optimally synchronized so that the processes during loading are completely reproducible. In addition, the BEC uses the proven rotary carton infeed system. More precisely when the cartons are drawn up and the products are placed inside, there is less waste and downtime.
Then, the new Elematic 1001 TL Topload case packer loads the packed products into RSC cases – two rows, three cartons each in six layers. The compact case packer is specially designed for ergonomic operation and can be easily integrated into any packaging line. Its wide format range of up to 600 mm in length, 400 mm in width and 350 mm in height allows it to be used for a variety of products. In addition, the Elematic 1001 TL processes pre-glued RSC and HSC blanks of different corrugated board thicknesses. The dotted application of hot-melt glue used to seal the cartons saves around 10 percent of energy and up to 40 percent of glue without sacrificing stability.