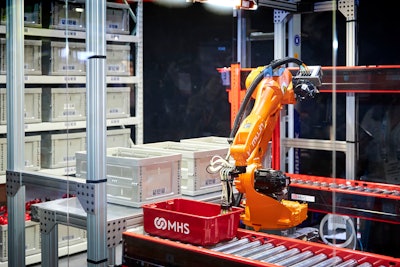
This content was written and submitted by the supplier. It has only been modified to comply with this publication’s space and style.
The system features automation strategies that can be applied to many common storage, picking, and order kitting workflows in e-commerce fulfillment and other distribution settings.
MHS’ goods-to-robot system offers rapid deployment, low total cost of ownership, operational efficiency gains of up to 400% compared to manual processes and increased product storage density by enabling product picking out of double-deep storage.
The system leverages the strengths of MHS integration and advanced robotic technologies including mobile enabled case storage and retrieval and pick-and-place. In addition to design, installation, and validation by MHS, the system is powered by a warehouse control system (WCS) and warehouse execution system (WES) that integrates the various automated components and robotics technology together to work as a smart, efficient system.
A zero-pressure accumulation conveyor from MHS feeds totes to and from the order fill station. Mobile robots transport totes between storage and a piece-picking robot. The robot picks each item for the order from a source tote, packs it and signals to the WCS/WES that the conveyor can move the completed order to the outbound location. The robotic arm uses vision, grasp intelligence and dynamic path planning to autonomously pick items cleanly and consistently – no colliding with the tote or inability to pick all items in the tote.