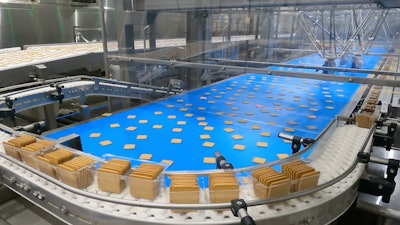
A family-owned contract manufacturer launched in 2007 and based in Caldwell, Idaho, ZoRoCo Packaging is all about making and packaging food—cookies, crackers, snacks, granola, blended baking mixes, and a variety of frozen foods. “Shaping the future of contract food manufacturing” is how they define their business, which is executed in three facilities: frozen, gluten-free, and “free-from.”
“We’re a little different in that we don’t really do anything under our own brand,” says company president Cordy Rost. “We manufacture for brands out there that bring their IP to us.”
A good example of the firm’s client base is New York-based Partake Foods. It was created in 2016 by Denise Woodard, who previously held a high-ranking job at Coca-Cola. But when her daughter was diagnosed with multiple food allergies, she created a company that exists to offer a selection of delicious foods that are certified gluten free, non-GMO, vegan, and free of the top 9 allergens. It was ZoRoCo’s expertise in gluten- and allergen-free food production that drew Woodard and Rost together.
“Partake was an integral part of bringing this new line to life,” says Rost. “We created a win/win for both companies.”
The new line he refers to, located in ZoRoCo’s free-from plant, is a highly automated production and packaging line used to make and package either square-shaped crackers or round cookies. Ahead of the packaging equipment are two key processing machines, both from Reading Bakery. One is a rotary molder that produces crackers and wafers, and the other is a wire-cut system that slices dough as it is extruded through a die plate, thus creating uniformly sized cookies. Regardless of whether crackers or cookies are in production, the same 1.5-m wide linear steel band oven from Reading Bakery takes care of baking.
Baked items exit the oven and proceed through cooling and primary packaging on a sophisticated robotic system supplied by Royal Houdijk. The ambient cooling conveyor, which is 1.2 m wide and stretches some 150 ft, ends with a section that takes the product through a 180-degree turn so that it is now moving back in the opposite direction. As soon as it completes its 180-degree turn, the product is transferred from the ambient cooling conveyor onto the 1.2 m-wide main conveyor of the Royal Houdijk COOKIEBOT.
Just upstream of this COOKIEBOT main conveyor is a conveyor section that offers what Houdijk’s area sales manager Dan DeJac calls the FIFO Inflow Buffer. “If there’s a downstream stop at the flow wrapper, for example, a signal is sent to our system that tells the 180-degree belt of the Inflow Buffer to automatically traverse away from the COOKIEBOT infeed, effectively extending the length of the cooling conveyor,” says DeJac. “This provides about five minutes of buffer time. Once the flow wrapper is back up and running, our system receives a signal telling the 180-degree belt of the Inflow Buffer to retract back to its ordinary length at a predetermined speed. It’s important to note that the only way this can work is by carefully designing overcapacity into the robotic pick-and-place solution so that we can fully deplete all the product we’ve buffered once the downstream stop has been addressed.”
Five robotic modules
As for the COOKIEBOT, it’s a vision-guided robotic pick-and-place system made up of independent robotic modules. The number of modules can vary according to customer requirements, and modules can be added if need be. But at ZoRoCo, there are five of these modules. Each module has two delta-style robots, designed and fabricated by Royal Houdijk, whose end effectors automatically stack product into slugs and place the slugs into polystyrene trays ready for flow wrapping. The trays are automatically denested by a Tramper machine tightly integrated into the overall system by Houdijk.Shown here are crackers moving toward the viewer from the white cooling belt and eventually to the main conveyor belt of the COOKIEBOT. Two-celled 18-count trays of crackers are moving left to right toward a decline conveyor leading to a flow wrapper further downstream.
“We’ve partnered with Tramper for decades now, and like any third-party OEM that we partner with the equipment has to offer toolless changeover, have superior sanitary design, and comply with the same electrical standards that we offer in the equipment that we design and build ourselves,” says DeJac. “This machine, the D-3100, uses vacuum pickup cups to pick four trays at a time from overhead magazines. The four picking tools then rotate 180 degrees to place trays single-file in a flighted conveyor that runs parallel to but in the opposite direction of the COOKIEBOT’S main conveyor. So product is loaded into trays counter-flow to the incoming product supply.”
As product transitions from the FIFO Inflow Buffer onto the COOKIEBOT’S main conveyor, a vision system—designed and integrated by Houdijk--inspects each product to validate that it’s not broken or somehow misshapen. If any product on the belt is out of spec, that information is captured by the system’s main controller so that that product is disqualified and ignored by the pick-and-place robots and will drop into a reject bin at the end of the COOKIEBOT’S main conveyor. The vision system also captures the position of each product and sends that data to the main controller so that each robot knows where it needs to position itself to make its next pick.
As impressive as all this automated product handling technology may be, the real magic in the Houdijk COOKIEBOT may be the patented SLUG GRIPPER end effector. Essentially a collating or stacking device that operates gently yet quickly, it has a three-prong picking tool that slides under a baked item and guides it into an indexing mechanism. Then the robot it’s mounted on moves immediately to another baked item on the belt and does the same thing, simply stacking products on top of each other (one by one) and using the SLUG GRIPPER to ensure control of the slug. Once the SLUG GRIPPER has a slug of five cookies or nine crackers, the robot moves to the flighted conveyor known as the fixed-pitch conveyor carrying the polystyrene trays. On the way, the SLUG GRIPPER rotates from a vertical orientation to a horizontal orientation and releases its slug of product into one compartment of a tray. At that point it’s ready to go back in to form another slug. Typically the trays have two compartments for an 18-count cracker offering and three compartments for a 15-count cookie offering.
Quick changeover
Since the crackers are square and the cookies round, ZoRoCo needs to change SLUG GRIPPERS when changing from cookies to crackers. But this is a toolless task that takes about a minute per end effector. Also notable, says DeJac, is that additional SLUG GRIPPERS can be easily supplied in the future. “If ZoRoCo comes to me and says they want to run a two-cell tray with 12 cookies per cell, it’s completely doable. We can also accommodate different shapes or sizes in the future due to the simplicity in being able to quickly develop and change SLUG GRIPPERS.”
Anyone who has been to PACK EXPO lately has seen automated systems using delta-style robots to pick cookies from a belt and place them into trays on a flighted conveyor. But typically those systems operate like this: pick, traverse to tray, place, traverse back to flow of cookies for the next pick. Royal Houdijk believes it has the only patented option available where the entire slug is formed without asking the robot to traverse back and forth from flow of cookies to the tray for each individual cookie. Houdijk’s DeJac points out that from a routine maintenance and wear and tear perspective, this SLUG GRIPPER method has obvious advantages.Shown here are round cookies that the COOKIEBOT is placing into three-cell 15-count trays.
“It also allows us to reduce the overall length of the line,” says DeJac. “If you’re picking one cookie at a time you need a lot more robots to get the job done. I would say, on average, it could be in the range of 20% more robots, because instead of making multiple short movements to collect a complete slug and then carry it to the tray, you have to do a bunch of picks, and you have to allow for the travel time between the tray back to the flow of cookies on the conveyor. So with the SLUG GRIPPER we're condensing the lines, utilizing less robots to handle the same throughput that you would encounter in traditional systems.”
The SLUG GRIPPER end effectors used at SoRoCo are pneumatically actuated. But they can also be servo driven, and Houdijk’s DeJac says the majority of systems being designed and installed now are in fact servo driven, further reducing the time for changeovers.
As for the controls components upon which the COOKIEBOT depends, in this particular application those were supplied by Beckhoff. But DeJac says that the Rockwell platform is Royal Houdijk’s standard. “We also decentralized our control platforms from the main electrical cabinet so that each module has its own controls,” adds DeJac. “So if, for example, you were to lose a PLC card, the whole line wouldn’t have to be shut down. Just that cell would be affected. And because of the overcapacity designed into the line, you would be able to still run at a nominal rate as the COOKIEBOT automatically adjusts the speed of the other robots in the line in that scenario.”
This modular approach to the controls package also lends itself to routine maintenance exercises. For example, if chocolate chip cookies are in production and a SLUG GRIPPER should get contaminated with chocolate, an operator can push a button to bring the two robots in that module to an operator-friendly and safe position to do a quick wipe down or remove the SLUG GRIPPER altogether and replace it with a clean spare.
“We also have a program for servicing and recalibrating the SLUG GRIPPERS,” says DiJac. “Like anything else, there are wear parts, right? We don’t want our customers trying to figure out how or when it’s time to replace bushings or other moving parts. So we supply them with spares so that they can remain in production. They ship SLUG GRIPPERS to our hub in Atlanta where we perform service and recalibration and then ship them back. We also include any respective upgrades as part of this service to always provide customers with the latest hardware available.”Close-up of the SLUG GRIPPER
Extensive benchtop testing
Considering the speed at which the SLUG GRIPPER operates, it’s fair to wonder how it can manage to do what it does without damaging what is, after all, a pretty fragile product. According to DeJac, that has a lot to do with the extensive testing and modeling that goes on before a system is offered. “We design and 3D print our tooling in house, we do our own assembly of the end effector, and then we put it through extensive benchtop testing. If revisions are required, we go back to the drawing board, and only when we’ve verified that we have what we want do we proceed with the project. Part of the process is learning how much force can the cookie or cracker withstand before it shows signs of damage. How fast can we move it vertically before it breaks in half? How much gripping pressure can we apply? All the dynamic forces that the product will be exposed to are taken into account long before we ever get to the point that a customer is ready to place an order. So by the time we’re sitting down to negotiate the purchase, we’re confident in agreeing to a 99% performance guarantee as part of the contract.”
The flighted conveyor carrying filled trays eventually reaches a slight incline so that it can carry the trays over the infeed belt conveyor of the COOKIEBOT while executing a 180-degree turn. The net result is that filled trays, which travel right between the cooling conveyor on one side and the belt conveyor of the COOKIEBOT on the other side, travel in the opposite direction of the cooling conveyor and in the same direction as the COOKIEBOT main conveyor. In short order the filled trays arrive at a Sacmi flow wrapper that wraps them in a clear film overwrap.
Next in the packaging flow is checkweighing by a Loma Systems unit and X-ray metal detection by a system from Thermo Fisher Scientific. Wrapped trays then are conveyed into an ADCO cartoner. Integrated into the cartoner is a Videojet ink-jet coder that puts a date code on each carton. Cartons at this point are manually case packed, but soon to be installed is a case packer from Douglas Machine.
One other element of versatility that distinguishes the COOKIEBOT is that not all product exiting the oven has to get placed in a tray. Some of ZoRoCo’s customers may also want two- or three-count portion packs that reach consumers through a gas station convenience store, or maybe even a single-count cookie pack aimed at airline passengers. If these formats are called for, operators can select a recipe at the HMI screen of the COOKIEBOT that will cause a small portion of the product flow to be diverted in such a way that they bypass the pick-and-place robots and are single-filed into a separate Sacmi flow wrapper than the one used for wrapping trays. This portion pack wrapper also inserts a lightweight paperboard component on which the cookie or cracker sits as it gets wrapped in film.Shown here are round cookies that the COOKIEBOT is placing into three-cell 15-count trays.
‘First experience with robotics’
Running now since Feb. 2024, the new equipment has more than met Rost’s expectations. He credits consultant Curtis Wardhaugh of Medalist Engineering with introducing him to the Houdijk COOKIEBOT. “One of the reasons we opted for Houdijk’s solution was that they contractually agreed to a 98% OEE,” says Rost. “And that’s exactly what they delivered. Keep in mind that this was our first experience with robotics. And we did consider more mechanical as opposed to robotic ways of automating what was a very manual and labor-intensive process. In fact some of the mechanical solutions were considerably less costly. But they didn’t offer the kind of flexibility that we get with the COOKIEBOT, and that was a key driver behind the decisions we made.”
Rost says that when it came time for installation and commissioning of the new equipment and training of ZoRoCo’s employees, Royal Houdijk was very helpful and supportive. It helped, he adds, that Houdijk is a big believer in the POKA-YOKE process analysis tool that more or less fool-proofs procedures by preventing a process from proceeding to the next step until the proper conditions have been met.
“It’s all very straightforward and intuitive,” says Rost. “You go to your HMI and select the program and that’s about it. The operators here love it. Plus Houdijk can connect with us remotely, so there’s been a few times where that has been helpful, too.” PW