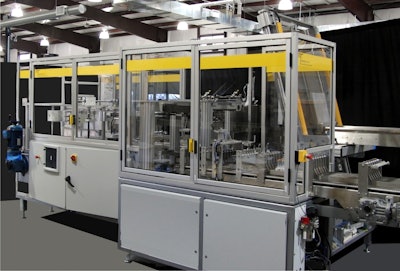
A number of infeed options include bucket conveyors, magazines, and robotic systems that collate and load the product onto the case blank. The system first picks a case blank from the high-capacity case magazine and places it into the case transport. Secondary flaps are folded via servo device in preparation for loading. Products are collated into the required pack pattern before being pushed with a servo‐controlled loading mechanism onto the case blank. The case is closed using a hot‐ melt glue system with servo movement on the traversing action.
The Model WA 10 handles up to 10 cases/min., while the Model WA 30 can handle up to 30 cases/min. The machine is complete with Category 3 interlocked Lexan safety guarding, and the design allows for easy cleaning and maintenance. Changeover is fast, typically under 10 minutes. The compact footprint easily fits into existing packaging lines, allowing manufacturers to automate manual case packing processes without sacrificing costly factory floor space. Designed to meet the needs of pharmaceutical, medical device, diagnostics and cosmetics manufacturers, the system handles cases from 150mm x 100mm x 100mm (A x B x C) to 500mm x 350mm x 250mm. Options such as case coding, case labeling, leaflet or booklet insertion, and case checkweighing create a complete end‐of‐line packaging solution.