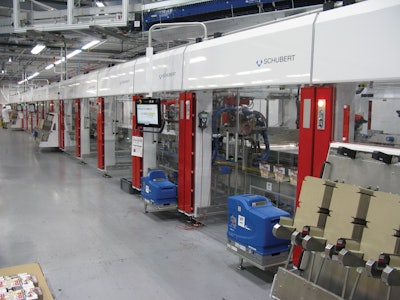
Family owned and forward thinking, Leclerc Foods is a fifth-generation Canadian bakery manufacturer based just outside of Quebec City with plants in four U.S. cities as well. In addition to its own iconic brands, the firm has established a sizeable amount of business on the private-label side of things, to the point that Vice President of Co-Manufacturing and Manufacturing Infrastructure Jean-Sebastien Leclerc estimates that only about 20% of the firm’s output is own-brand product.
Over the past few years Leclerc, along with robotic automation supplier Schubert, has been busy optimizing the cartoning of its film-wrapped energy bars. With the installation this past May of its fifth impressive robotic system, this time at its headquarters plant, Leclerc was able to boost its cartoning speeds from 750 to 1,200 bars/min. The length of the Schubert system is 131 ft, and upon seeing it one’s reaction is to think that it’s rather on the large side—until one learns what it has replaced and how much it has opened up, simplified, automated, and accelerated the cartoning process.
Also essential is how much easier it is to go from a six- to a 12- to an 18-count carton. With so much of Leclerc’s production being of the private-label variety, that kind of flexibility and ease of changeover is priceless.
It’s worth pointing out that the cartoning solution that Leclerc replaced was also a robotic one. But it was considerably less streamlined to say the least, involving as it did two carton erectors, two delta style robotic carton pick-and-place carton loaders, and two carton closers. Not to mention all the conveyor connections needed to tie the two erector/loader/closer lines together.
“We like how compact the footprint of the Schubert system is compared to what we had before,” says Jean-Sebastien Leclerc. “Carton erecting, filling, and closing is all self contained in one machine. Floor space is always an issue, but in the first plant where we installed the Schubert solution, our Tennessee plant, we were especially tight for space, so it was an especially big improvement there. Not only that, just one operator is needed on this entire robotic system.”
Flow wrapping is first
The energy bars are made one floor above the packaging operation. They’re brought down to the packaging floor and fed into two existing flow wrappers. Subsequently they make their way to four parallel infeed conveyors that lead them into the Schubert system, which is characterized by several essential design features:
• First, it operates on a counterflow principle. The bars being being cartoned travel north on the main product conveyor, then south on what Schubert calls “transmoduls,” then north again once they’ve been picked from the transmoduls and placed into cartons, and finally south as filled cartons exit in the opposite direction that individual bars entered.
• Second, while all bars travel down the same main product conveyor, there are actually three tightly integrated cartoning machines picking bars from that conveyor. Each of these machines is made up of six sub-machines responsible for picking, placing, and carton closing.
• Third, bars aren’t picked and placed directly into cartons. Instead, they’re picked from the main product conveyor and placed into transmoduls, which are carriages that are milled from an aluminum block. Each transmodul—600 mm long, 200 mm wide, and 120 mm high—runs on a rail. The power supply is inductive, and all data and signals are transmitted wirelessly, so each transmodul can move freely on its rail. In each of the three cartoning systems there are seven transmodul carriages, and it’s these carriages that deliver wrapped bars in the desired count to a sub-machine that picks the whole group from the carriage and places it in an erected carton. Among the benefits of this approach is that while individual bars move along the main product conveyor in continuous motion, when it comes time to pick a group of bars for placement into a carton, the transmodul from which the bars are picked is stationary.
• The proprietary vision system on the Schubert equipment inspects every bar on the main product conveyor to learn its position so that it can tell the robotic pick heads where they need to go to pick individual bars. The vision system also inspects for quality control, so if bars are stuck together or a bar’s wrapper is open, that bar will not be picked by a robot.
Counterflow in action
Because the TLM cartoning system is based on a counterflow principle, the place where individual energy bars enter is the exact same place where finished cartons are discharged—in the opposite direction, of course. Speaking of infeed, the infeed portions just ahead of the Schubert conveyors consist of four parallel conveyors engineered by ABF Systems Inc. ABF also handled the integration of the checkweighing and printing stations and the overhead conveyor system that takes cartons to a remote case packer. Many of the conveyor connections are made by Dorner, a conveyor OEM with whom ABF has a longstanding partnership.
The sequence of operation on the Schubert system is as follows (be sure to follow along on the video). Incoming bars are on four parallel conveyors narrow edge leading. They drop onto the cartoner’s main product conveyor. Measuring 4 ft across, it runs perpendicular to the four infeed conveyors. This means that now the bars are oriented on the main product conveyor wide edge leading. And because each of the four infeed conveyors is a little bit longer than the one to its left, the bars are now neatly arranged on the main product conveyor in a four-across pattern.
As was mentioned previously, the Schubert system is actually three identical cartoners each consisting of six submachines. A look at the first of the three cartoners tells the story of the other two, as well.
The first sub-machine is carton erecting. On the day of our visit, six-count cartons were in production, so each carton consisted of three bars with three more on top. Carton blanks are picked three at a time from three magazines by a Shubert F2 robot and pressed through a forming module. Before entering the forming module, each carton has adhesive applied by a Nordson unit. Out the bottom of the forming module emerge three erected cartons that drop onto one of two parallel vacuum transport conveyors. The forming module reciprocates back and forth so that it can drop three erected cartons onto one vacuum transport conveyor and then three onto the other vacuum transport conveyor. The vacuum, of course, ensures that the position of the cartons is tightly controlled as they are transported to the loading station that comes next.
Arriving in the loading station from the opposite direction in which the cartons are traveling are transmoduls, each one filled with 24 wrapped energy bars that have been picked one at a time from the main product conveyor by a Schubert F4 robot. A Schubert F2 robot uses a combination of vacuum and mechanical picking to lift 24 wrapped bars from a transmodul and place them into four cartons, six per carton, on one of the two vacuum transport conveyors on which the freshly erected cartons rest. The now empty transmodul then advances on a racetrack style arrangement back to its start position so that it can be filled with bars again when its number is called.
On to carton closing
Cartons filled with bars now continue forward to the closing station, again passing Nordson adhesive nozzles along the way. In the closing station, a Schubert F4 robot uses its end effector tooling to close the top and side flaps of four cartons per cycle and compress the flaps against the walls of the cartons. The finished cartons then make a U-turn on a discharge conveyor that descends on a decline so that they can run beneath the main product conveyor.
At the discharge of the Schubert system, then, are three parallel conveyors that carry finished cartons in the direction of existing secondary packaging. One other intriguing bit of equipment on the line is a high-speed automatic feeding system from IntelliFEED that typically comes into play only if one of the three Schubert cartoning machines goes down. When this happens, the bars that the down cartoner would have picked drop off the main product conveyor into a tote. Once the down Schubert is back up and running, the totes of bars are emptied into the IntelliFEED, which then meters them onto the main product conveyor so they can be picked along with all the others.
As for changeover, it’s entirely tool-free and is driven by an electronic recipe management system. Change parts are mounted on a cart that gets wheeled up next to the portion of the Schubert system where the parts are to be mounted. The operator presses a button on the HMI and all glue nozzles, which are mounted on stepper motors, move automatically to the new positions they need to be in. The operator then opens the guard doors, unhooks the tooling that needs to be removed, and loads the new tooling into place. An RFID tag is read to ensure that the tooling being mounted matches what the electronic recipe management system calls for. Should the wrong tooling somehow be mounted, an error message would alert the operator to this fact.
A final note on installation. It was done in what might be called a parallel fashion. In other words, the existing two cartoning lines kept operating as the Schubert system was installed beside them. Then in one weekend, the flow of energy bars was diverted from old to new, and by Monday Leclerc was up and running.
Facebook for factories
Prominently visible at every piece of packaging equipment at Leclerc are large QR codes that are at the heart of a home-grown user-based collaboration solution called Poka. The brainchild of Alexandre Leclerc, brother of Jean-Sebastien Leclerc, it brings a social network quality to the manufacturing space. Which is why Alexandre refers to it as “facebook for factories.”
Every piece of equipment has a profile page. Leclerc employees access the profile page by scanning the QR code with a tablet. Once the profile page is open, the employee sees any and all information relevant to that piece of equipment—not just guides and troubleshooting tips but videos and real-time problem-solving steps that other employees in other Leclerc plants are taking on the same piece of equipment.
Suppose a flow wrapper, for example, is malfunctioning in a way that causes multiple energy bars to be rejected. By scanning the machine’s QR code and accessing the machine’s profile page, an operator in Leclerc’s Tennessee plant can see video of how his counterpart in the Pennsylvania plant encountered and solved the same problem.
“You have Facebook for your personal life, LinkedIn for your professional life, and now Poka as your industrial network,” says Alexandre Leclerc. “That’s the vision we have for this. It’s a way of connecting the supply chain, too. Like if we encounter a problem with a carton erector that we think is caused by the carton supplier. Our operator can tag that supplier in a post on that machine’s profile page and the supplier will see immediately that there is a problem. They can share it with the production line making that carton.”
Each packaging machine’s profile page is like a vault where videos, images, and tips can all be stored. With a quick scan of the machine’s QR code, training and troubleshooting—even a vital tip entered into the profile page by an operator on the previous shift—is at an operator’s fingertips. So Poka becomes a way of developing a culture of sharing equipment improvements and settings.
Once Leclerc Foods realized how valuable a tool Poka was in its own plants, a separate company headed up by Alexandre Leclerc and Antoine Bisson was launched to sell the solution to a broad audience. “We grew from two guys in a garage to now having 32 employees,” says Alexandre Leclerc. Customers, he adds, include the likes of Keurig, Westrock, and Arcelor Mittal.