We start with what Italy's CAMA Group calls its Breakthrough Generation of machines, specifically the CL 175 cartoner. An alternative to standard top- or side-loading cartoners, it's a pitchless machine powered by a modular, scalable linear motor system that allows for independent control of multiple movers on straight or curvilinear paths. The linear motor is Rockwell's iTrack, which eliminates chains, belts, and gears and replaces them with simple, effective software profiles that redefine speed and flexibility in automation applications. In addition to greatly increased flexibility, the machine has a remarkably small footprint of approximately 13 x 8 ft. By Rockwell's calculations, a more traditional cartoner with comparable capabilities that did not deploy a linear servo motor might have a footprint of 26 x 11.5 ft. Worth noting is that adhesive application on the CL 175 shown at interpack was just as next-gen as the machine's linear servo motor, as CAMA opted for Nordson's Freedom system, a tankless heat-on-demand concept that reduces energy consumption and maintenance-related downtime caused by charred hot melt.
Next-gen cartoning at interpack
There’s no place like interpack to see the latest in packaging machinery controls and automation. Here are just two examples of what the world’s largest packaging show had on display in the cartoning sector.
May 19, 2014
Machinery Basics
Break out of the ordinary: see what’s new in packaging & processing!
At PACK EXPO Las Vegas, you’ll see machinery in action and new tech from 2,300 suppliers, collaborate with experts and explore transformative solutions. Join us this September to experience a breakthrough in packaging and processing.
REGISTER NOW AND SAVE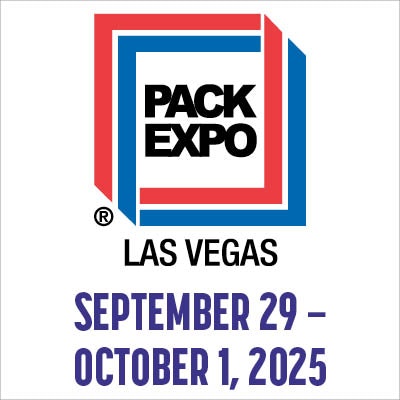
Annual Outlook Report: Sustainability
The road ahead for CPGs in 2025 and beyond—<i>Packaging World</i> editors review key findings from a survey of 88 brand owners, CPG, and FMCG readers.
Download Now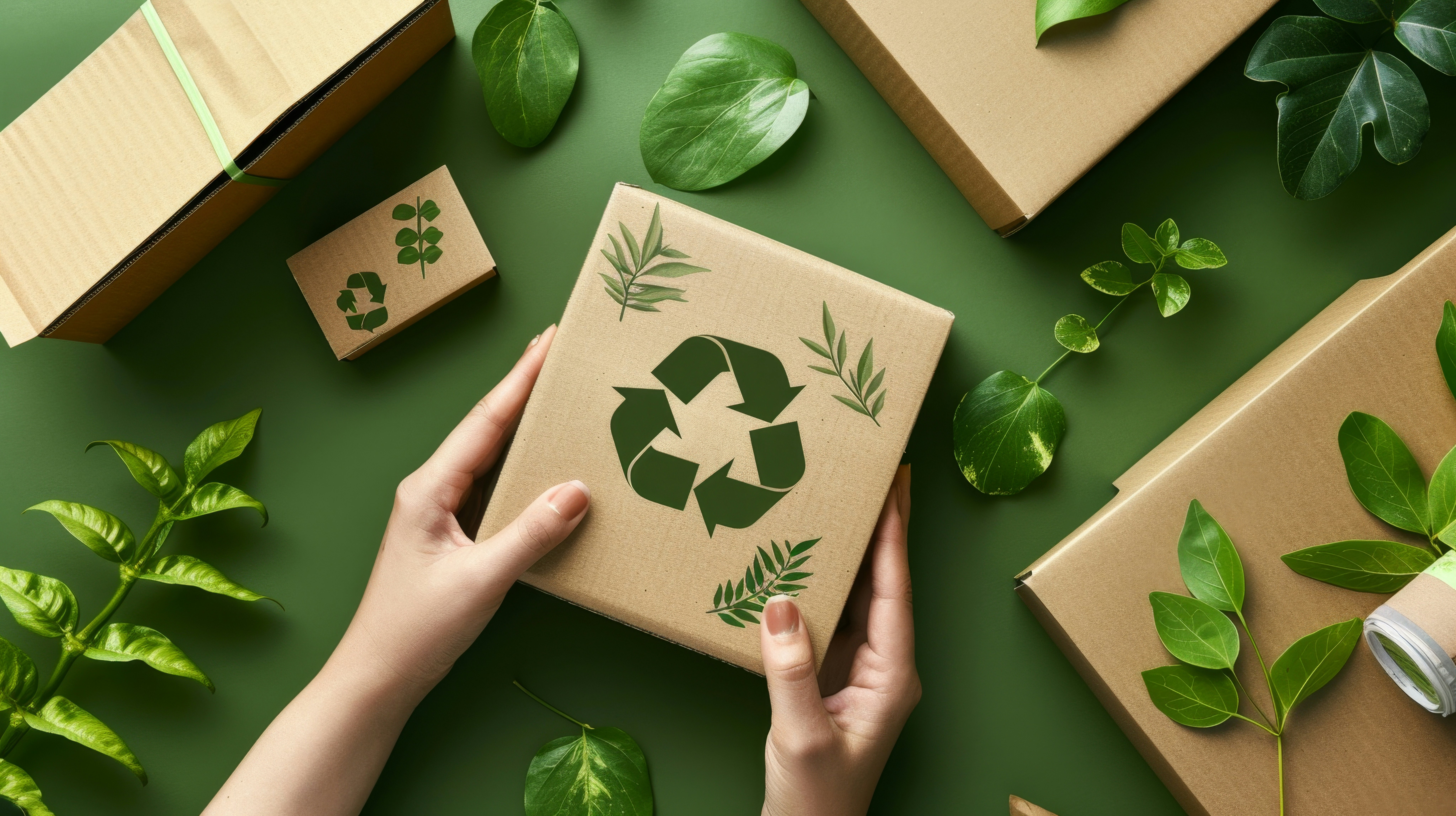