We start with what Italy's CAMA Group calls its Breakthrough Generation of machines, specifically the CL 175 cartoner. An alternative to standard top- or side-loading cartoners, it's a pitchless machine powered by a modular, scalable linear motor system that allows for independent control of multiple movers on straight or curvilinear paths. The linear motor is Rockwell's iTrack, which eliminates chains, belts, and gears and replaces them with simple, effective software profiles that redefine speed and flexibility in automation applications. In addition to greatly increased flexibility, the machine has a remarkably small footprint of approximately 13 x 8 ft. By Rockwell's calculations, a more traditional cartoner with comparable capabilities that did not deploy a linear servo motor might have a footprint of 26 x 11.5 ft. Worth noting is that adhesive application on the CL 175 shown at interpack was just as next-gen as the machine's linear servo motor, as CAMA opted for Nordson's Freedom system, a tankless heat-on-demand concept that reduces energy consumption and maintenance-related downtime caused by charred hot melt.
Next-gen cartoning at interpack
There’s no place like interpack to see the latest in packaging machinery controls and automation. Here are just two examples of what the world’s largest packaging show had on display in the cartoning sector.
May 19, 2014
Machinery Basics
Pharmaceutical Innovations Report
Discover the latest breakthrough packaging technologies shaping the pharmaceutical sector. This report dives into cutting-edge innovations, from smart containers that enhance patient safety to eco-friendly materials poised to transform the industry’s sustainability practices. All from PACK EXPO. Learn how forward-thinking strategies are driving efficiency and redefining what’s possible in pharma packaging.
Learn More
2024 PACK EXPO Innovations Reports
Exclusive access: Packaging World editor-curated reports revealing PACK EXPO's most groundbreaking technologies across food, healthcare, and machinery sectors. Each report features truly innovative solutions selected from hundreds of exhibitors by our expert team. Transform your operations with just one click.
Access Now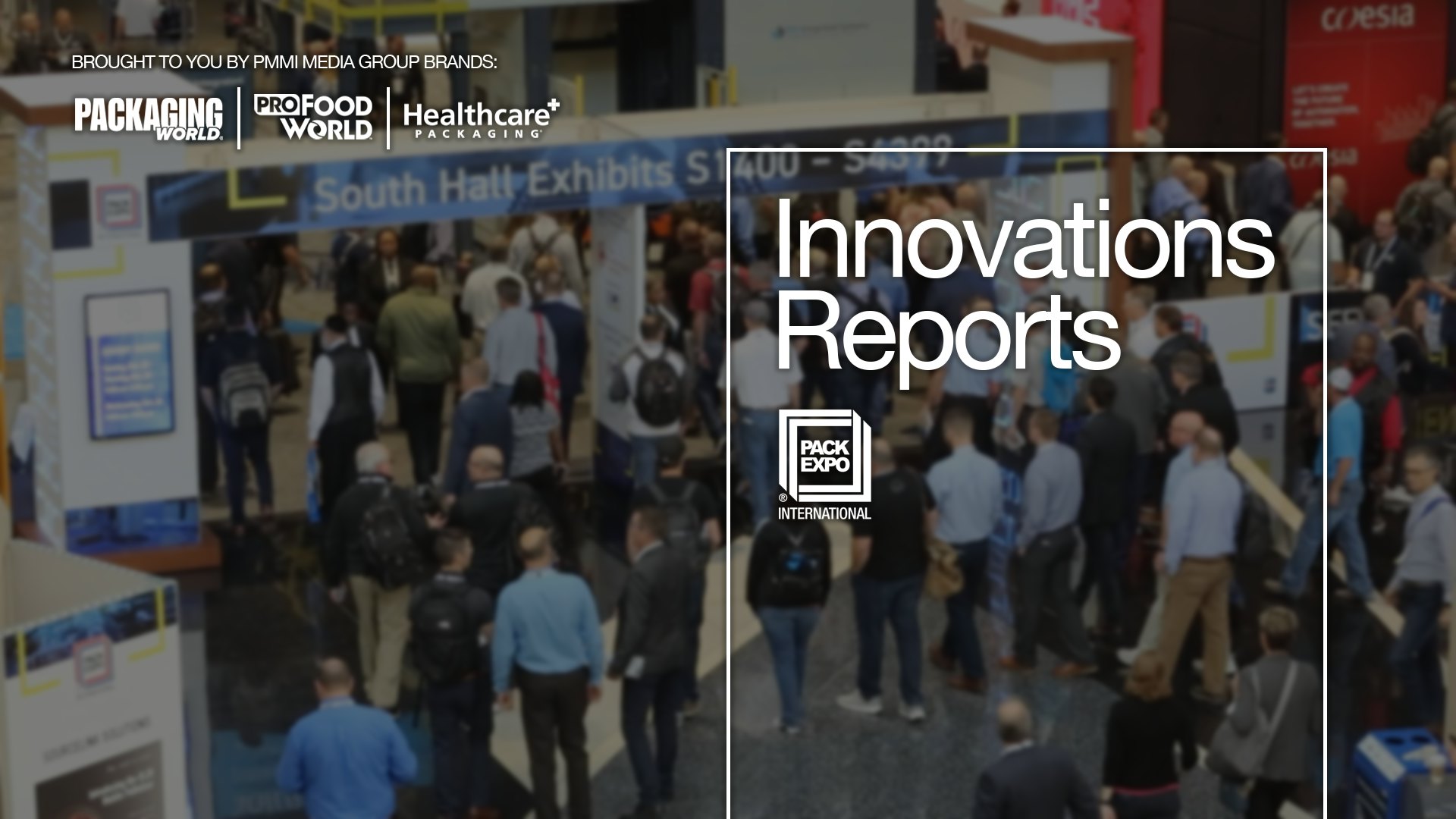