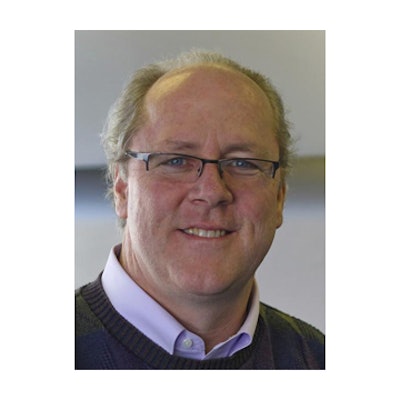
Q: Over the years, we've seen the terms cold chain distribution, temperature-controlled distribution, temperature-sensitive distribution and logistics, etc. Is there an appropriate umbrella term?
Kevin O’Donnell: The terms have evolved with the global growth of the market and with the extension of regulatory reach and oversight—and they continue to do so. There have been a few overarching or all-inclusive phrases that have been introduced to try and capture this but many seem to become obsolete or fall short with scope expansion—“cold chain,” “cool chain,” and “current Good Distribution Practices for Time and Temperature Sensitive Pharmaceutical Products,” to name a few.
Supply chain integrity is one that has been bandied about for the past few years representing a more holistic approach to maintaining the quality of the drug product across the spectrum of many processes, which have grown to include manufacturing, intermediate storage, transportation, distribution, security, environmental sensitivities (temperature, humidity, light, shock, vibration), and soon to climb on board, track and trace. This is due in large part to the way the newer generations of many drugs, particularly the highly specialized biological drug manufacturing processes, have gone from inter-plant to international.
Q: You serve on the IQPC "cold chain pharmaceuticals" advisory board and advise clients to help troubleshoot their challenges in this area. What two or three areas are the most frequently noted obstacles or mistakes you see and how can manufacturers resolve those matters?
Kevin O’Donnell: Many drug manufacturers are deeply embedded in the practice of performing only the required stability studies for establishing efficacy, degradation, shelf life, and expiration dating for their products with little understanding of how these materials behave outside those parameters. Time and cost are often cited as the reasons for not extending the scope of stability studies. For new products, stability testing is generally done during Phase I and Phase II of the clinical trials process and there is tremendous financial pressure to launch as soon as humanly possible. An investment to review stability of legacy products rarely happens. While speed-to-market is a great motivator, such a practice often pigeon-hole’s a drug product’s storage requirements to something very specific—like refrigerated temperatures of 2°C to 8°C. Maintaining that temperature during storage is not difficult but transporting it through an often harsh and largely misunderstood distribution environment is. Companies spend nearly $8.5 billion dollars industry-wide on specialty packaging and logistics for time and temperature-sensitive products.
By reevaluating the stability of many (not all) drug products, companies can save tens of millions of dollars on packaging, can reduce waste, and can improve processes with no threat to product integrity or patient safety.
Another factor is education. As this sector of the healthcare industry continues to expand, so does its complexity. New regulations, expectations and guidance continue to pop-up seemingly from all corners of the supply chain. It can be both overwhelming and intimidating. Understanding the rules in an international market is a challenge that few are prepared to meet.
Q: Your new book refers to the effectiveness of "nature's packaging" that beg the question, "When are we going to learn from those packages?" That sounds great, but how can manufacturers implement packaging that's more inline with natural packaging solutions when it comes to temperature-sensitive products?
Kevin O’Donnell: When indeed. You cannot outwit the laws of physics—although many companies try—or at least assert such claims. Nature, as I have illustrated by many examples in my book, always has the best, most elegant answer. Always. The answer frequently comes down to cost. Packaging (tertiary packaging in general and insulated packaging systems specifically) has long been considered the redheaded stepchild of product delivery—a necessary miscellaneous expense item that is rarely seen as added value to the product. Pound-for-pound and dollar-for-dollar, expanded polystyrene boxes and water-in-a-bag are still the most efficient means of maintaining most products within a desired range of 2°C to 25°C during transport. This is tied to our reliance on crude oil and water. Barring any significant global economic changes, I don’t see any paradigm shift. However, the triad of sustainable materials, reusable tertiary packaging, and sound economic return logistics are what I envision as the future of packaging for this industry.
Q: How do meeting regulatory requirements affect packaging materials, choices, etc?
Kevin O’Donnell: Packaging material choice is generally not driven by regulatory requirements (although the use of rigid polyurethane foam is an example of an insulating material that can be an environmental headache in some countries such as Germany). The question lies in what you want your package to do (performance parameters), and for how long. Total cost of ownership continues to grow in popularity as companies are taking advantage of the benefits of greater capital outlay for more sophisticated and expensive package materials whose costs are offset by greater payload-to-packaging ratios, weight decreases, and transportation/logistics costs savings.
Q; If you had to name one single issue or trend that is the most important for manufacturers of products that must go through the cold chain what would it be and why?
Kevin O’Donnell: Do your homework—know the temperature robustness of your product before you file your biologic license application with regulatory authorities. Such sound scientific justification is generally accepted and can go a long way in the development of your packaging and transportation processes without compromising product quality or patient safety.
Q: How do you define the term "logistics" withincold chain/temperature-controlled distribution?
Kevin O’Donnell: The right product in the right place, at the right time, in the right condition.
Exelsius brings expertise, knowledge and network strength into a range of essential business services designed to meet the requirements of Good Distribution Practices (GDP) in the Life Sciences logistics sector.