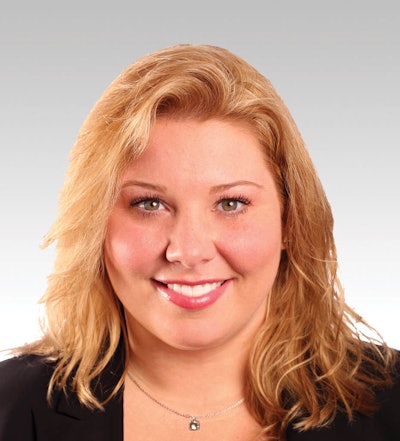
While this small percentage demonstrates the industry as a whole is doing a great job, it is the responsibility of each shipper to do everything they can to ensure the safe, leak-free transportation of their hazardous materials.
The point of hazardous materials packaging is obvious: to contain the “stuff” inside the package during transportation. To meet this goal, DOT requires that packages must pass a battery of performance-oriented tests designed to ensure that each package will arrive safely at its destination under conditions normally experienced in transportation. Once the packages pass these tests, they are certified as UN Specification Packaging and are deemed strong enough to contain the dangers of certain hazardous materials during transportation.
Boxes are one type of non-bulk package (less than 119 gal in capacity). While certain boxes can be used for dry goods with minimal packing material, most are used with an inner package, like bottles, cans, or jars. This arrangement is a combination package, and like all UN packagings, it must pass a battery of performance tests. These include manufacturer-prescribed closures, absorbent, cushioning, etc. These parts function as a system, which derives its strength and durability from the cooperation of its parts.
UN testing procedures are very thorough, but remember, the UN certification applies to this specific combination of packaging materials only. Any change to the intended design of the package system changes the performance of the package, so selecting another bottle, jar, or cushioning intrinsically alters the design of the package and increases the possibility that it will not perform as intended.
This is important to keep in mind when re-shipping products sent to you by others, especially if the box is being opened or broken down; the final package still must be shipped with approved closures, inner packages, absorbent, etc. Sending a partial package after removing a bottle or shipping one of the bottles in another box increases the opportunity for package failure because the package no longer meets the standards to which it was tested.
Of course, every shipment of hazardous materials starts with good package selection, and package manufacturers offer a myriad of options to get your packages to their destination safely. Each possible combination will be tested and UN certified to ensure it meets minimum strength and durability standards. It may be possible to select glass jars or plastic bottles or even metal cans of all different sizes. They may have different mouth shapes and sizes, or different neck, shoulder, or body designs. You may have the option of double- or single-walled fiberboard boxes; wooden, plywood, and metal boxes also may be available. The variety is endless, but ultimately, your selection will be dictated by the intended contents of the package and your specific needs, which includes regulatory compliance.
Compatibility, of course, is paramount when selecting packaging; make sure the packaging you choose will not react dangerously with the material. In other words, if you are going to put acetone in a plastic bottle, ensure that the bottle is not made of a plastic that will melt when in contact with acetone.
Be sure your packages are rated for the materials they will transport. Boxes are rated X, Y, or Z as follows: (X)—PGI, PGII and PGIII; the strongest and most versatile but also the most expensive of the Spec Packages. (Y)—PGII or PGIII only; less strong, less expensive, and less versatile than a package certified as X. (Z)—PGIII only; the least strong and least versatile, but also the least expensive of the spec packages. Last but not least, if you plan to ship by air, do not forget to select packaging that has been pressure tested to 95 kPa (kilopascals).
The point is that any deviation from the packaging standards increases the possibility for failure and loss astronomically and jeopardizes the good name and reputation you have worked to build. Work with your internal experts and package manufacturers to devise foolproof methods for shipping hazardous materials and you will never fear boxes and bottles and jars, oh my!
Wendy Buckley is President and Founder of Specialty Transportation and Regulatory Services. For more information on IoPP, visit www.iopp.org.