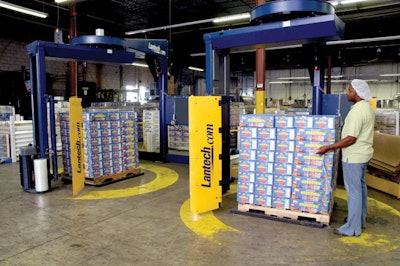
Kisko Products, Markham, Ontario, Canada, produces frozen juice bars and other premium juice products for grocery store distribution throughout North America. One of Kisko’s most successful products is Kisko Freezies—juice packaged in clear polypropylene tubes produced on a form/fill/seal machine (PP film and f/f/s equipment suppliers undisclosed). Consumers freeze the liquid products in their home freezers to prepare them for consumption.
Kisko mixes all the liquid Freezies’ ingredients on-site, using 100% juices such as orange, mango, black cherry, grape, apple, and pear. The sealed tubes of liquid then are packed in multi-count cartons which are cased (carton and casing suppliers undisclosed), and then palletized for shipment.
Kisko’s vp of operations Randy Josephs notes, “Our company’s aging turntable pallet stretch wrappers were slow and inefficient in the prestretch of film, so ongoing material costs were high. We knew that new equipment could cut our film use significantly and improve overall efficiency, and we started to look at available options.”
Safety first
Kisko’s cases are hand-palletized in loads up to a 40 x 48 x 70-in maximum height, or in half-loads. Because the pallet loads weigh up to 1,800 lb and are relatively top-heavy and unstable, Kisko focused on rotary-arm stretch wrappers to replace the turntable machines.
“At the time we started looking at new equipment, all the rotary-arm wrapping machines on the market required a safety fence around them,” recalls Josephs. “We put a premium on safety as it relates to our transport packaging. But apart from the added cost and floor space needed for the fence, it’s never a perfect solution because someone will always find a way to defeat a safety perimeter while the machine is running or being serviced. Even after a stop, the arms on most stretch wrapping machines will continue to rotate for one-half of a revolution or more. And you don’t want to be the person whose sleeve or pant leg just got snagged on that arm. Also, we manually apply corner boards to our pallet loads-which further complicates the operation of a fenced-in machine.”
Then Kisko learned that Lantech, Inc. (www.lantech.com) had introduced the S-Series™ straddle stretch wrapping system with a large shock-absorbing safety shield on the rotary arm and a drive system that stops the rotation immediately, if there is any pressure on the safety shield.
Kisko investigated this new equipment. Josephs concludes, “These machines proved as safe or safer than those with a perimeter fence. They cost less because there’s less hardware. And they take less floor space. We had budgeted for one fenced-in machine. But for just a little more money, we could afford two of the unfenced Lantech S-300 machines. This gave us needed redundancy and extra capacity for growth because just one of these machines provides greater output than our two older turntable machines combined.”
The S-300 is a free-standing wrapping system that requires no wall mounting and takes up just 188 sq ft. It can wrap load sizes up to 76-in-high at 25 to 35/hour. All the operator has to do is attach the film to the load. An Auto Film Cut-off mechanism lets the operator hop back on the lift truck after starting the wrap. Film savings are accomplished with electronically controlled prestretch, which is 200% for Kisko’s 70-g film.
The machine provides a 14-in-wide clearance between the moving wrap arm and the machine’s single vertical column to protect any worker who might get between the column and the arm. “The safety system on the S-300 amazed even the inspector from Canada’s Ministry of Labor, who initially said the machine needed to be fenced in,” notes Josephs. “The arm turns as fast as any fenced machine, but stops dead in its tracks if the bumper strikes anything in its path. The ability to have this level of safety without a perimeter fence is such an advantage.”