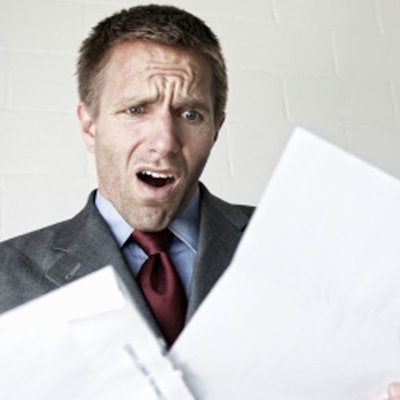
Receiving a Warning Letter from the U.S. Food and Drug Administration is bad enough, but when those Warning Letters are published on the agency’s Web site where companies can read, print out, and use them for competitive advantage, the “incentive” is even greater for companies to take corrective action.
Since 2009, FDA’s increased power and budget have led to more seizures, injunctions, Warning Letters, and recall events, with penalties enforced to discourage future offenses. More inspections and public enforcement actions—even YouTube videos—are part of the new strategy the agency hopes will ultimately help safeguard consumers of healthcare-focused products.
That message was delivered during a Sept. 22 conference presentation entitled, “Surviving a New Era of FDA Enforcement,” held during the Medical Design & Manufacturing Chicago event. The conference session was chaired by Michael Barile, founder and managing partner of Barile & Associates. The company serves clients in the medical device, human tissue, pharmaceutical, and biotechnology industries.
Throughout the day, a reoccurring theme centered on how fast companies must respond to FDA action. Less leniency is being given for the 15-day period to respond to an FDA Warning Letter. In fact, it was noted that an FDA injunction or seizure can now be issued prior to sending a Warning Letter. Another challenge for industry: FDA’s completion of the Warning Letter closeout process once a violation has been satisfactorily addressed is not as prompt as industry would like. A closeout letter from the agency could arm a company with necessary ammunition to counter related competitive challenges.
Barile introduced Nicholas Lyons, assistant to the director of investigations in the Chicago District of the FDA. Lyons confirmed that the agency’s enforcement actions have risen in the last two years. He did point out, however, that “regulatory action requires considerable time and commitment by the FDA.” He advised, “Responding to a Warning Letter requires substantive evidence of corrective actions and evidence about what you intend to do or actions you will take to address a problem.”
He recommended that companies visit FDA's Web site and click on the Warning Letters link to search for the status of Warning Letters and learn from the mistakes of other companies. “There’s a new column with a closeout date on the site. FDA needs to get back to a firm receiving a Warning Letter within six months. We’re trying to get a company back into compliance for the purposes of public safety,” said Lyons.
He offered several information points for companies undergoing FDA inspections. Among them were the following:
• FDA expects you to be in compliance with the Code of Federal Regulations
• Although not mandatory, it can be beneficial to respond to FDA-483 points within 15 business days
• This response letter is reviewed and considered if regulatory action is pending or on follow-up inspections
• Response may provide evidence of corrective actions, implemented procedures (include copies), certificate of destructions, recalls, and any dated commitments to observations
• Responses may address firm-wide FDA-483 points, not just examples to support the specific observations
• It may be helpful to review the FDA Investigations Operations Manual (IOM). The IOM is the primary guidance document on FDA inspection policy and procedures for field investigators.
• The most frequent FDA-483 citations are available by searching “Inspection Observations” on FDA's Web site.
• Do not back-date documents or create records that do not exist
• Provide reasonable justification for decisions and have it documented
• Review issues to determine if they exist firm-wide
• Review FDA Warning Letters
• Ask yourself whether your audit or supplier qualification program provide useful data that allows you to mitigate risk and establish quality.
• Make sure you have a complaint system that identifies complaints that provide reliable data to initiate effective CAPARs that increases the quality of the medical device.