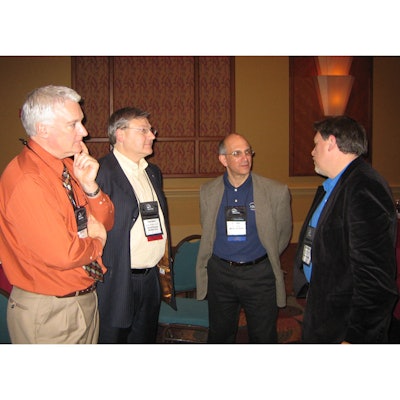
Discussing innovation at the ARC Automation Forum's packaging machinery track are (l to r) Rob Hattin of Edson Packaging Machine
This content was written and submitted by the supplier. It has only been modified to comply with this publication’s space and style.
Packagers applauded ARC Advisory Group for devoting a complete track at their annual forum to packaging machinery.
What the packagers appreciated most was the actionable nature of the sessions, which centered on specific innovations, collaboration with materials suppliers, automation trends, design refinements, sustainability, global operability and mechatronics.
These attendees were corporate engineering leaders, with responsibility for finding new solutions, driving increased profitability and implementing the technologies.
ARC, the major analyst firm in the automation space, does an excellent job of spotting trends -- such as wireless plant floor communications, product lifecycle management, and integrated control platforms.
Enabling innovation
This time, through speakers and panelists from major packaging machinery manufacturers and automation suppliers, ARC drilled down into innovations in packaging machinery and operations.
Rob Hattin of Edson Packaging Machinery showed how the case packer manufacturer had used a ‘skunkworks’ process to design and build a new robotic packaging system in just 97 days and partnered with his automation supplier, Schneider Electric, to support the machinery globally.
Hattin’s journey from pencil sketches to finished robot was the subject of a recent packworld.com article.
Sustainability demands innovation, collaboration
While sustainability remains a hot topic, it became clear that innovative thinking is the real driver in the value equation. For instance, a discussion of ‘sustainable manufacturing’ covered longstanding practices, whereas Optima Machine’s Peter Delain described a sustainable package called the ‘soft can,’ that allows rigid containers to be produced from film stock. Consider that one truck can deliver enough film to replace 75 trucks carrying empty cans, and the energy savings alone become rapidly apparent.
John Kowal, from Schneider Electric’s ELAU Packaging Solutions, emphasized the importance of such collaboration with machinery and automation specialists early in the package development process in order to rapidly launch a viable new package format or material.
The Packaging Machinery Manufacturers Institute’s Tom Egan showed several examples of sustainable packages to demonstrate the broad range of challenges facing machine designers. A number of PMMI member companies were involved, such as Douglas Machine’s Joe Faust.
Automation anticipated future requirements
Packaging materials savings have been the primary target of sustainability initiatives. This is because the high volume of packages makes a 1% improvement significant.
The question is, will the machinery a packager purchases today run materials under development, such as biopolymers or recycled board with vastly different properties, that may be required in the future?
For example, servo capping is an order of magnitude more controllable than conventional clutch capping (+/- .02% compared to +/- 20%). Applying this kind of feedback sensitivity, available from servos today, can offer effective future proofing for unanticipated requirements.
And if difficult packages increase scrap rates, it not only has the obvious negative effect in terms of material reduction, it also leads to downtime that reduces throughput per energy unit used. Frequent stoppages mean a machine may never operate at its rated throughput. The space occupied by a down machine must still be heated and lighted.
Kowal noted that automation solutions can reduce jams and stoppages, reduce the time required to resume operation when a stoppage does occur, and provide an ideal computing platform for measuring and analyzing Overall Equipment Effectiveness (OEE).
About Schneider Electric’s ELAU Packaging Solutions
Schneider Electric’s ELAU Packaging Solutions is the only automaton supplier in the world exclusively focused on the packaging machinery. They offer the only automation system purpose-built for the packaging industry.
Through ELAU, Schneider Electric equips over $1 billion worth of packaging machines annually, with over 45,000 systems already deployed worldwide.
The market demands packaging operations that are more flexible and efficient to fulfill marketing, supply chain and global business strategies. Schneider Electric innovations have enabled a revolution in mechanical, software and hardware modularity to deliver these agile packaging systems.
What the packagers appreciated most was the actionable nature of the sessions, which centered on specific innovations, collaboration with materials suppliers, automation trends, design refinements, sustainability, global operability and mechatronics.
These attendees were corporate engineering leaders, with responsibility for finding new solutions, driving increased profitability and implementing the technologies.
ARC, the major analyst firm in the automation space, does an excellent job of spotting trends -- such as wireless plant floor communications, product lifecycle management, and integrated control platforms.
Enabling innovation
This time, through speakers and panelists from major packaging machinery manufacturers and automation suppliers, ARC drilled down into innovations in packaging machinery and operations.
Rob Hattin of Edson Packaging Machinery showed how the case packer manufacturer had used a ‘skunkworks’ process to design and build a new robotic packaging system in just 97 days and partnered with his automation supplier, Schneider Electric, to support the machinery globally.
Hattin’s journey from pencil sketches to finished robot was the subject of a recent packworld.com article.
Sustainability demands innovation, collaboration
While sustainability remains a hot topic, it became clear that innovative thinking is the real driver in the value equation. For instance, a discussion of ‘sustainable manufacturing’ covered longstanding practices, whereas Optima Machine’s Peter Delain described a sustainable package called the ‘soft can,’ that allows rigid containers to be produced from film stock. Consider that one truck can deliver enough film to replace 75 trucks carrying empty cans, and the energy savings alone become rapidly apparent.
John Kowal, from Schneider Electric’s ELAU Packaging Solutions, emphasized the importance of such collaboration with machinery and automation specialists early in the package development process in order to rapidly launch a viable new package format or material.
The Packaging Machinery Manufacturers Institute’s Tom Egan showed several examples of sustainable packages to demonstrate the broad range of challenges facing machine designers. A number of PMMI member companies were involved, such as Douglas Machine’s Joe Faust.
Automation anticipated future requirements
Packaging materials savings have been the primary target of sustainability initiatives. This is because the high volume of packages makes a 1% improvement significant.
The question is, will the machinery a packager purchases today run materials under development, such as biopolymers or recycled board with vastly different properties, that may be required in the future?
For example, servo capping is an order of magnitude more controllable than conventional clutch capping (+/- .02% compared to +/- 20%). Applying this kind of feedback sensitivity, available from servos today, can offer effective future proofing for unanticipated requirements.
And if difficult packages increase scrap rates, it not only has the obvious negative effect in terms of material reduction, it also leads to downtime that reduces throughput per energy unit used. Frequent stoppages mean a machine may never operate at its rated throughput. The space occupied by a down machine must still be heated and lighted.
Kowal noted that automation solutions can reduce jams and stoppages, reduce the time required to resume operation when a stoppage does occur, and provide an ideal computing platform for measuring and analyzing Overall Equipment Effectiveness (OEE).
About Schneider Electric’s ELAU Packaging Solutions
Schneider Electric’s ELAU Packaging Solutions is the only automaton supplier in the world exclusively focused on the packaging machinery. They offer the only automation system purpose-built for the packaging industry.
Through ELAU, Schneider Electric equips over $1 billion worth of packaging machines annually, with over 45,000 systems already deployed worldwide.
The market demands packaging operations that are more flexible and efficient to fulfill marketing, supply chain and global business strategies. Schneider Electric innovations have enabled a revolution in mechanical, software and hardware modularity to deliver these agile packaging systems.
Companies in this article
Videos from Douglas Machine Inc.