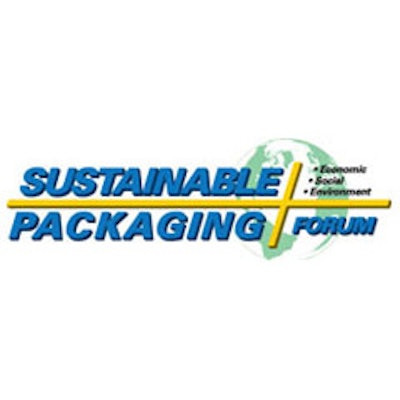
The Sustainable Packaging Forum grapples with the challenges of sustainability and identifies directions, enabling technologies
We’ve all heard about alternative feedstocks, biopolymers, light-weighting and down-gauging to achieve sustainability. But a voice was heard from the wilderness at the fourth annual Sustainable Packaging Conference in Denver. The lone voice was that of the packaging machinery suppliers.
“To learn how materials suppliers, packagers and machinery designers can collaborate to generate sustainable package designs, look no farther than Europe,” stated John Kowal, one of the forum’s supply chain panelists.
He is global marketing manager for Schneider Electric’s ELAU Packaging Solutions, which provides the automation systems that have been helping packaging machinery meet new requirements for many years. ELAU is the only automation supplier specializing exclusively in packaging machinery.
“European materials suppliers actively partner with packaging systems providers to develop practical packaging innovations – like the ‘soft can.’”
The soft can references a collaboration between Huhtamaki for the film structure and design and Optima for the machinery to form and ultrasonic weld a can-shaped flexible package. Called Cyclero, it was the buzz at the last interpack fair in Dusseldorf.
“We need to do more of this kind of collaboration, up front, here in the U.S.,” according to Kowal.
“Much of the technology exists today,” Kowal asserted. “Instead of controlling bottle capping torque to +/- 20%, today’s technology can control torque to 0.02%. That kind of precision makes a huge difference in the ability to down-gauge without creating waste.”
The panelists were:
• Kimberly Harvey , Director, Supply Chain Packaging & Sustainability,
The Kellogg Company
• Brad Rogers, Manager, Sustainable Packaging &
Advanced Materials Research, Frito-Lay
• Glenn Ventrell, Director, Package Innovation & Development, Sara Lee
• Patrick Smorch, Director, Packaging Sustainability, Georgia-Pacific
• Shane Bertsch, Director, Product Development & Global Innovation, HAVI Global Solutions
• Mark Kitzis , Global Account VP, Alcan Packaging
• John Kowal, Global Marketing Manager, ELAU
• Jeff Wooster, Senior Value Chain Manager, The Dow Chemical Co.
Packaging Automation magazine conducted this followup interview to draw out more specific information than the panel arrangement afforded:
PA: How serious is the collaboration gap between Europe and North America when it comes to achieving machineability of new designs?
Kowal: We’ve been informing machine builders, brand owners and package designers about these ventures for a few years now, notably in presentations at the 2006 Package Design form and various PMMI and IoPP events. We shared a number of innovative package samples from Europe, where we’re the market share leader in packaging automation.
We examined things like the former SIG’s Combishape beverage cartoning system, the Tassimo T-Disc single serve beverage cup, ACMA’s pocket sized lozenge dispensing cartons and all manner of flexible packages with built-in handles, resealable closures, dual chambers and the like.
PA: You said that much of the technology is already in the market to achieve sustainability?
Kowal: Absolutely. You’ll find some really simple solutions that the Europeans have practiced for years that we could implement tomorrow. A lot of toothpaste tubes in Europe are packed vertically into trays and wrapped – instead of cartoned and case packed. At the store, the tray becomes the p-o-p display.
There are wrappers available today guaranteeing 10-30% reduction in film usage through gentler handling of thin gauge films and more precise cutting/sealing that produces less edge scrap.
Stick packs actually use less material than sachets, so you can have your single-serve convenience and source reduction, too. The latest stick pack machinery fills much more consistently across all lanes, too. That means reduced give-away as well as not wasting product.
Compared to legacy stick pack machines that require a service tech to fly in and spend 4 days for a changeover, the latest designs change formats with plant personnel in a couple of hours.
Remember, you’re lighting and heating/cooling the space that an idle machine occupies. And you’d be better off using the carbon units saved from that technician’s flight to visit a European packaging trade fair.
PA: Will sustainability then be your theme at PACK EXPO?
Kowal: No, that would be greenwashing. People would see through any automation supplier taking credit for sustainability right away, they wouldn’t have any credibility.
Automation is an important enabling technology, but that’s all.
Our theme will be ‘experience innovation,’ because innovation is what we deliver – and what it will take to support ongoing sustainable initiatives.
PA: What specifically are the future issues that machine builders need to address in sustainable package design?
Kowal: First, will the machine you buy today have the capacity to run unanticipated new materials five years from now? It could be board with a higher recycled content. It could be polymers that are thicker or have coarser surfaces or lower tolerances to the heat in sealing bars and shrink ovens. It could be renewable materials like bamboo and sea grass.
Machinery should have the capacity to meet unanticipated requirements because the odds are much higher that we will encounter new materials compared to five years ago. That is largely a matter of the control system, to have the sensitivity, sensor feedback and bandwidth to adapt with precision and without sacrificing production efficiency.
Speaking of efficiency, OEE is a great way to get at the low hanging fruit of sustainability by reducing scrap and increasing throughput. Remember, you’re not just throwing packaging material away – quite often, especially in dairy and meat, you’re also scrapping product that is getting more expensive on a daily basis.
PA: Schneider Electric and ELAU have been sponsoring our OEE workshops, led by Paul Zepf. But you don’t make an OEE product per se.
Kowal: Our message is to just start somewhere, see improvement and keep going. Don’t wait. And you know what? I’ve attended four of our OEE workshops and the participants are rolling up their shirtsleeves. They’re taking home straightforward solutions that they can implement immediately, without buying software or consulting services.”
Where do we fit in? We have an automation platform much more conducive to data acquisition and on-machine analysis than the status quo. We also make it very easy to implement the ISA 88.05 standard and OPC to get at the actionable information in a timely way.
PA: But OEE is nothing new, right?
Kowal: OEE has been used in manufacturing for decades. Manufacturing people practice product lifecycle management, too – so why not packaging?
Consumer products are designed for source reduction, manufacturability, recycled content and recyclability. CAD/CAM has been looking at product design in the context of automated manufacturing machinery and assembly systems. And manufacturing operations are the target of ‘lean’ strategies to increase efficiency.
Why not packaging? You could call it sustainability, good engineering practice or just sound business strategy. In the end, even if you didn’t care about sustainability in terms of the environment, from a cost standpoint you sure want to ‘make the most of your energy.’
PA: The last statement is his parent company Schneider Electric’s new campaign, ‘Make the most of your energy,’ referring to Schneider’s range of energy saving electrical products and energy management solutions for the entire facility – ranging from building automation and lighting to industrial automation.
About ELAU packaging solutions
ELAU, Schneider Electric’s packaging specialist, equips over $1 billion worth of packaging machines annually. Currently, over 40,000 purpose-built ELAU packaging automation systems are deployed in machinery worldwide.
Through ELAU, Schneider Electric is the only controls supplier with a dedicated business unit focused exclusively on the automation of packaging machinery.
The market demands packaging operations that are more flexible, efficient and sustainable to fulfill marketing, supply chain and global business strategies. ELAU innovations have enabled a revolution in mechanical, software and hardware modularity to deliver these agile packaging systems.
For more information, visit www.elau.com or email [email protected].
“To learn how materials suppliers, packagers and machinery designers can collaborate to generate sustainable package designs, look no farther than Europe,” stated John Kowal, one of the forum’s supply chain panelists.
He is global marketing manager for Schneider Electric’s ELAU Packaging Solutions, which provides the automation systems that have been helping packaging machinery meet new requirements for many years. ELAU is the only automation supplier specializing exclusively in packaging machinery.
“European materials suppliers actively partner with packaging systems providers to develop practical packaging innovations – like the ‘soft can.’”
The soft can references a collaboration between Huhtamaki for the film structure and design and Optima for the machinery to form and ultrasonic weld a can-shaped flexible package. Called Cyclero, it was the buzz at the last interpack fair in Dusseldorf.
“We need to do more of this kind of collaboration, up front, here in the U.S.,” according to Kowal.
“Much of the technology exists today,” Kowal asserted. “Instead of controlling bottle capping torque to +/- 20%, today’s technology can control torque to 0.02%. That kind of precision makes a huge difference in the ability to down-gauge without creating waste.”
The panelists were:
• Kimberly Harvey , Director, Supply Chain Packaging & Sustainability,
The Kellogg Company
• Brad Rogers, Manager, Sustainable Packaging &
Advanced Materials Research, Frito-Lay
• Glenn Ventrell, Director, Package Innovation & Development, Sara Lee
• Patrick Smorch, Director, Packaging Sustainability, Georgia-Pacific
• Shane Bertsch, Director, Product Development & Global Innovation, HAVI Global Solutions
• Mark Kitzis , Global Account VP, Alcan Packaging
• John Kowal, Global Marketing Manager, ELAU
• Jeff Wooster, Senior Value Chain Manager, The Dow Chemical Co.
Packaging Automation magazine conducted this followup interview to draw out more specific information than the panel arrangement afforded:
PA: How serious is the collaboration gap between Europe and North America when it comes to achieving machineability of new designs?
Kowal: We’ve been informing machine builders, brand owners and package designers about these ventures for a few years now, notably in presentations at the 2006 Package Design form and various PMMI and IoPP events. We shared a number of innovative package samples from Europe, where we’re the market share leader in packaging automation.
We examined things like the former SIG’s Combishape beverage cartoning system, the Tassimo T-Disc single serve beverage cup, ACMA’s pocket sized lozenge dispensing cartons and all manner of flexible packages with built-in handles, resealable closures, dual chambers and the like.
PA: You said that much of the technology is already in the market to achieve sustainability?
Kowal: Absolutely. You’ll find some really simple solutions that the Europeans have practiced for years that we could implement tomorrow. A lot of toothpaste tubes in Europe are packed vertically into trays and wrapped – instead of cartoned and case packed. At the store, the tray becomes the p-o-p display.
There are wrappers available today guaranteeing 10-30% reduction in film usage through gentler handling of thin gauge films and more precise cutting/sealing that produces less edge scrap.
Stick packs actually use less material than sachets, so you can have your single-serve convenience and source reduction, too. The latest stick pack machinery fills much more consistently across all lanes, too. That means reduced give-away as well as not wasting product.
Compared to legacy stick pack machines that require a service tech to fly in and spend 4 days for a changeover, the latest designs change formats with plant personnel in a couple of hours.
Remember, you’re lighting and heating/cooling the space that an idle machine occupies. And you’d be better off using the carbon units saved from that technician’s flight to visit a European packaging trade fair.
PA: Will sustainability then be your theme at PACK EXPO?
Kowal: No, that would be greenwashing. People would see through any automation supplier taking credit for sustainability right away, they wouldn’t have any credibility.
Automation is an important enabling technology, but that’s all.
Our theme will be ‘experience innovation,’ because innovation is what we deliver – and what it will take to support ongoing sustainable initiatives.
PA: What specifically are the future issues that machine builders need to address in sustainable package design?
Kowal: First, will the machine you buy today have the capacity to run unanticipated new materials five years from now? It could be board with a higher recycled content. It could be polymers that are thicker or have coarser surfaces or lower tolerances to the heat in sealing bars and shrink ovens. It could be renewable materials like bamboo and sea grass.
Machinery should have the capacity to meet unanticipated requirements because the odds are much higher that we will encounter new materials compared to five years ago. That is largely a matter of the control system, to have the sensitivity, sensor feedback and bandwidth to adapt with precision and without sacrificing production efficiency.
Speaking of efficiency, OEE is a great way to get at the low hanging fruit of sustainability by reducing scrap and increasing throughput. Remember, you’re not just throwing packaging material away – quite often, especially in dairy and meat, you’re also scrapping product that is getting more expensive on a daily basis.
PA: Schneider Electric and ELAU have been sponsoring our OEE workshops, led by Paul Zepf. But you don’t make an OEE product per se.
Kowal: Our message is to just start somewhere, see improvement and keep going. Don’t wait. And you know what? I’ve attended four of our OEE workshops and the participants are rolling up their shirtsleeves. They’re taking home straightforward solutions that they can implement immediately, without buying software or consulting services.”
Where do we fit in? We have an automation platform much more conducive to data acquisition and on-machine analysis than the status quo. We also make it very easy to implement the ISA 88.05 standard and OPC to get at the actionable information in a timely way.
PA: But OEE is nothing new, right?
Kowal: OEE has been used in manufacturing for decades. Manufacturing people practice product lifecycle management, too – so why not packaging?
Consumer products are designed for source reduction, manufacturability, recycled content and recyclability. CAD/CAM has been looking at product design in the context of automated manufacturing machinery and assembly systems. And manufacturing operations are the target of ‘lean’ strategies to increase efficiency.
Why not packaging? You could call it sustainability, good engineering practice or just sound business strategy. In the end, even if you didn’t care about sustainability in terms of the environment, from a cost standpoint you sure want to ‘make the most of your energy.’
PA: The last statement is his parent company Schneider Electric’s new campaign, ‘Make the most of your energy,’ referring to Schneider’s range of energy saving electrical products and energy management solutions for the entire facility – ranging from building automation and lighting to industrial automation.
About ELAU packaging solutions
ELAU, Schneider Electric’s packaging specialist, equips over $1 billion worth of packaging machines annually. Currently, over 40,000 purpose-built ELAU packaging automation systems are deployed in machinery worldwide.
Through ELAU, Schneider Electric is the only controls supplier with a dedicated business unit focused exclusively on the automation of packaging machinery.
The market demands packaging operations that are more flexible, efficient and sustainable to fulfill marketing, supply chain and global business strategies. ELAU innovations have enabled a revolution in mechanical, software and hardware modularity to deliver these agile packaging systems.
For more information, visit www.elau.com or email [email protected].
Companies in this article