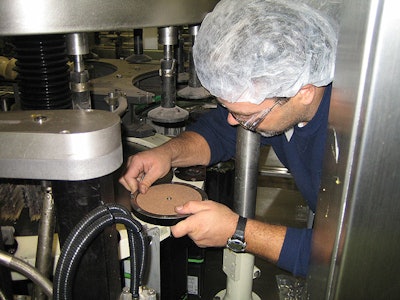
K2 Engineering and ELAU team up to support contract packager’s business strategy
Fast flawless changeovers are important for contract beverage processor Yakama Juice to attract business from major beverage and grocery chain customers. Their ability to do turn-on-a-dime changeovers makes Yakama more competitive in terms of both cost and responsiveness.
A Krones rotary labeler remanufactured by K2 Engineering Group Big Bend Wisconsin has removed the bottleneck from Yakama’s quick change strategy. It is the first labeler ever re-engineered with ELAU’s PacDrive™ SCL integral servo motor/drive technology.
These purpose-built servo modules were developed to make servo automation practical on machines with rotating carousels. The concept is also key to what ELAU has termed the Virtually Zero Cabinet initiative™.
First of many
A number of fillers cappers and labelers manufactured in the U.S. Germany and Italy now use ELAU’s award-winning servo technology including cappers from Krones. But the only place to get a PacDrive-equipped Krones labeler right now is from K2.
K2 managing director Ed Stefaniak and project director high speed rotary labeling equipment. They established K2 specifically to bring their innovative packaging concepts to the beverage industry.
Their first remanufactured servo-equipped labeler went to Selah Washington-based Yakama Juice Company in 2005. And it will certainly not be the last as an undisclosed number of projects are currently in the works.
Fast changeovers broad range of formats
According to Yakama plant manager Jack West they need the labeler to perform 2 to 3 changeovers per day on the line running round 16 oz. 32 oz. and gallon bottles plus rectangular quarts. Both glass and PET bottles use full-wrap hot-melt glue applied paper labels.
They are now making format changes in 15-20 minutes which is a savings of 10-15 minutes per changeover. An operator and mechanic typically double-team the changeovers. The changeover team chases the end of the production run so as the last bottle leaves the labeler they start setting up the labeler for the next run.
Picture perfect changeovers
Changeovers now consist of selecting the photo of the bottle to be labeled on the touchscreen HMI panel and dialing in the label stations and loading the magazines with the new labels. “You just push on the picture of the bottle you want to run so language is not an issue” West notes.
The previous labeler had performed yeoman service for 15 years and is in fact finding a new home. But it was the line’s bottleneck in a size change. Now labeler changeovers are faster than the cooling cycle so the fundamental constraint is the line’s designed capacity. In service for 8 months now the new labeler’s servo systems have performed flawlessly and the machine has a smaller footprint than its predecessor as well.
Infinite range of bottle profiles at high speeds
The line runs round 16 and 32 oz. bottles as well as rectangular bottles. Adding rectangular bottles “changed everything” according to West who was originally reconciled to receiving a machine that could only run rectangular shapes. “When K2 said they could do everything on one machine I was really impressed” West explained “Being able to handle glass as well – that was icing on the cake. We could even run the rectangular bottles faster if the volume on the line was higher.”
Servo-driven bottle plates and feed screw are the key enabling technologies permitting an infinite range of software cam profiles to run whatever bottle shapes and sizes the contract packager may encounter in the future.
The bottle plate servos are mechanically configured in unique K2-developed cartridges a quick-change modular design that includes the PacDrive SCL motor/drive a planetary gearbox and a compression fitting that mounts onto the rotating table with “no hammer” arbor assembly.
Servos the ‘way to go’
As he oversaw two mechanics manually adjusting a clutch-operated conveyor component on another part of the line West told Packaging Automation that “servos are the way to go” for both flexibility and critical performance.
“Timing is critical” West said. “If the timing is off just a bit or the bottle falls off the plate and doesn’t line up for the output star you’ve got trouble. Just a hair too much pressure on the brushes and you’re in trouble.”
The labeler’s servos assure the required precision consistent operation much faster response to control inputs and have required no maintenance or adjustment in the 8 months since the labeler has been installed.
NEXT INSTALLMENT: How the remanufactured servo labelers work.